苗立民
时至今日,DCS技术已经十分成熟,越来越多的石化企业将改造为DCS控制。随着DCS应用的深入,对DCS组态的工作也由制造商转向设计院和用户来完成,即通常所说的用户组态。目前,业内人士对DCS用户组态工作的研究还局限于对DCS操作画面组态的研究。本文结合先进控制系统在中原石油化工总厂的成功应用以及作者在实践中的经验,探讨DCS用户组态,提出一些想法。 先进控制系统在中原石油化工总厂的成功应用有三套:1996年FOXBORO I/A’S成功应用于FCCU-2三机组控制,集控制、联锁一体化;1998年HONEYWELL TPS成功应用于FCCU-2装置,同年SMAR EIC-2000成功应用于30t锅炉控制。1999年FCCU-2增加脱硫装置,纳入TPS控制。三套系统自投用至今,一直运行正常,为总厂创造了很高的效益。而这三套系统的组态工作都是用户组态完成的。 一套用户组态的DCS能否被成功应用,提高控制品质,使因其故障造成的影响减小,方便监视和操作,其关键是DCS组态设计的质量。 1 用户组态的内容 DCS用户组态是指在DCS中,按照其厂商提供的功能部件的特点、数量和性能,为完成工程需求,设计、实现并确定有关的排列,包括硬、软件排列。 DCS硬件排列是指DCS输入/输出设备上的接线位置与外部生产过程参数位置之间的分配。DCS软件排列是指对DCS所提供的控制算法或模块的选用、模块间的连接以及系统的调试等。 DCS用户组态是一件十分细致的工作,所要求的知识面 广。在组态过程中,既要了解生产过程对控制的要求,熟悉生产过程,深刻认识各种设备和过程的生产顺序,明确生产过程和仪表的相互关系;还要熟练掌握DCS所提供的各个控制算法或模块功能,以及各功能模块提供的各参数(即软连接信号端子)的相互影响,DCS提供的顺控语言;同时,还要有一定的计算机知识。只有从深度和广度上对DCS、工艺生产过程以及控制要求有了足够清楚的认识,才能更好的完成用户组态工作。 在进行DCS用户组态工作时应注意以下几点: ① 安全性和可靠性设计应贯穿整个用户组态设计的全过程。 ② 在设计时,合理分配输入/输出信号,要为系统扩展、调试做好铺垫,控制模块或算法的组合一定要有扩展余地。 ③ 控制模块或算法的选择要合适,充分发挥DCS的计算、逻辑等功能。选择控制模块或算法时,一定要考虑系统负载因素,选择合适的模块或算法可以减少系统负载和节省内存空间。 2 用户组态的硬件设计 进行用户组态的硬件设计一定要有深度,要纵览全局。在DCS选型时,应对仪表、变送器和执行机构等部件,传输信号电缆和DCS输入/输出卡件有全面的考虑。从工艺的合理性、投资的经济性、运行的可靠性、维修的方便性等进行综合分析。例如,用一体化温度变送器检测过程的温度,由于采用标准电流信号传送,电缆芯数可减少或不采用补偿导线,因此,可在温度检测精度较高时选用。在温度检测点数较多、温度检测元件的类型相同时,采用DCS的温度处理卡件可节省较多的变送器投资费用。因此,仪表和执行机构选型不同,对DCS的硬件选型和控制组态也有不同的影响。 实践证明,在进行DCS组态的硬件设计时,应注意以下几点: ① 确定控制和联锁的关系,选择合适的设备 生产装置从安全角度讲,可分为三个层次,如图1所示。第一层为生产过程层;第二层为过程控制层;第三层为联锁停车保护层。 DCS用户组态在最初的工程设计、设备选型及安装阶段,都要对过程和设备的安全性进行考虑。生产装置本身是安全的第一道防线;控制系统对生产的连续动态控制是安全的第二道防线;在过程控制之上设置一套紧急联锁停车系统,最大限度的保护设备和人身安全是最后一道安全防线。因此,在DCS用户组态时,首先要确定DCS实现控制和联锁系统的形式。目前通常有5种基本形式:① 控制、联锁一体化式;② 控制、联锁通讯网络式;③ DCS+PLC;④ DCS+PLY;⑤ DCS+ESD。 根据资料提供的数据,采用上述5种形式,平均无故障间隔时间(MTBF)及可靠度(R)参见表1。
表1
形式 |
①形 |
②形 |
③形 |
④形 |
⑤形 |
可靠度R |
0.6185 |
0.710 |
0.9185 |
0.9435 |
0.9523 |
MTBF/H |
1.66x104 |
2.3x104 |
0.94x105 |
1.4x105 |
1.6x105 |
具体采取何种形式,需考虑多方面的因素。 ② 硬件故障造成的影响应尽可能小 在用户组态设计时,可靠性设计应贯穿其全过程。由于在系统的实际应用中不可能也不允许对DCS的硬件都采用冗余设计。为此,应考虑硬件的某些部件一旦发生故障时,它对生产过程的影响是否是最小的。例如,FCCU-2三机组联锁信号按机组分为若干组,每个组是各自独立的,组内的联锁条件是所在组内的一个联锁状态。在DCS控制的硬件组态设计时,考虑到独立性问题把各组的联锁信号分别连接到各自的输入/输出部件上,这样,一旦某一输入/输出部件发生故障,仅对相应的组有影响,对其他组的联锁不造成影响。 ③ 合适的输入和输出信号配合,能有效地减小输入/输出部件故障的影响 DCS的设计思想之一是分散控制,合适的输入和输出信号的配合可以使负荷分散。例如,将所有信号按照实际变化率和重要性分配为不同的采样周期,在设计时将不同采样周期的信号合理的组态在一起,使输入/输出部件微处理单元的负荷较均匀,这样会减少硬件因负载过大而发生故障。再如,采用单回路或多回路控制时,为了减少通信的吞吐量,应把有关控制回路的输入/输出信号连接在同一输入/输出部件上,以减小因通信造成的负荷量。当采用数据库共享时,为了减小某一部件故障的影响,可采用对每个回路都分配一个输入或输出信号。在实际应用时应权衡利弊,合适配置。 ④ 方便安装和维护 在设计过程中,诸多因素将影响系统的安装和系统投运后的日常维护。 3 用户组态的软件设计 在设计时应注意下列各点: ① 充分利用DCS所提供的各种控制算法或模块,提高控制质量
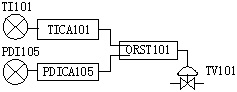
图1 生产装置的安全层次 图2 TICA101与PDICA105超驰控制
针对不同的工艺过程特点,充分利用DCS所提供的各种控制算法或模块,是提高设计水平的重要方法。从理论上来说,控制度升高,控制质量会下降,因此,在DCS中应利用计算机运算方便、离散的控制算法、软连接等优点,提高使用DCS后的控制质量。例如,DCS能方便实现微分先行、积分分离、自整定等控制算法。在设计时,可根据工艺过程的不同要求选用有关的控制算法,使控制质量提高。例如,我们在FCCU-2反再系统上实现了超驰低值选择控制系统。其控制原理如图2所示。 TICA101是提升管反应温度控制,PDICA105是再生塞阀压差控制,ORST101是超驰低值选择控制。这样很容易实现在不同工况下对再生阀TV101控制权的转换,不仅可以维持催化剂的正常流化,还可以防止发生催化剂倒流事故。该回路在组态设计时,对无扰动切换及抗积分饱和问题进行了特殊处理,在使用中可自由切换,无需平衡处理。 ② 采取前馈反馈控制策略 在采用模拟仪表控制工艺过程时,由于前馈控制需要相关的运算单元仪表完成,因此,除了干扰影响很大时才采用外,一般不常采用。由于DCS有运算方便的特长,因此,干扰量如果已经引入DCS,则采用前馈反馈控制策略有利于克服干扰的影响,提高控制质量。通常,采用静态前馈就能大大改善控制品质,静态前馈放大系数也可实施设置。 ③ 采用按计算指标进行控制的控制系统 在采用模拟仪表控制工艺过程时,由于实施按计算指标进行控制的控制系统需要较多的运算单元仪表,因而应用面不广。采用DCS,为按计算指标进行控制提供了有效的运算工具,因此,在DCS组态的软件设计时应对其予以考虑,提高控制品质。例如,在FCCU-2三机组主风流量、气压机入口富气流量的计量检测时,可采用温压补偿运算,使计量更加准确。 ④ 采用纯滞后补偿控制系统 由于DCS能方便实施纯滞后补偿控制系统,因此,在DCS控制组态的软件设计时,应根据对象的纯滞后大小设计相应的控制系统,例如,在随动控制系统中采用史密斯控制方案。对定值控制系统,采用观测补偿器控制方案等。 ⑤ 逻辑开关控制与常规PID控制相结合 在经典的控制方案中,逻辑开关控制与常规PID控制是很少在一起使用的,在DCS中,由于控制组态的方便,使逻辑开关控制与常规PID控制可方便地结合在一起,形成复杂控制系统以适应不同工况下的控制要求。例如,在FCCU-2分馏塔底液面控制方案中利用逻辑开关控制与常规PID控制组合形成的复杂控制方案,如图3所示。
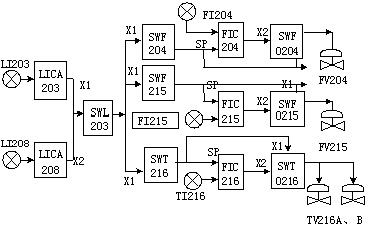
图3 FCCU-2分馏塔底液面控制方案
该方案根据不同工况很容易实现不同的控制方案。组态时对不同方案下的切换进行了平衡处理,可以做到无扰动切换。当控制偏差大于某一限值时,采用开关控制,使偏差迅速减小;当偏差在限值范围内时,控制系统自动切入常规PID控制,与积分分离的控制策略相类似,该控制方法能有效地降低调整时间,提高控制质量。逻辑开关控制与常规PID控制的结合也可在设备的启停过程中实施。例如,设备运行信号使PID控制系统切入自动,设备停止运动时,PID控制系统切入手动。由于在切入手动时,系统保持原阀门开度,因此,设备一旦运行就能迅速地进入正常的运行工况,提高了自动化水平,改善了控制品质。 ⑥ 与操作流程图设计相结合 除了DCS的输入/输出信号应设计有关的数据库元素外,如果工艺操作需要某些中间变量,在控制组态软件设计时也应建立相应数据库元素。例如,经温度压力运算后的计量信号、倒计时信号、操作人员可设置的信号等。这些信号在DCS的过程流程图上显示或被调整,在控制组态设计时应考虑在内。 ⑦ 有条件时,可采用DCS所提供的高级控制算法 随着现代控制理论的研究和深入,把现代控制理论的研究成果应用到DCS的控制中是其控制组态设计的一项重要的工作。基于模型的预测控制算法已有应用,模糊控制算法和自适应控制算法要求和实际的操作水平相适应。在设计选型时,结合操作人员的技能条件,有条件地采用高级算法,充分发挥DCS的优点,不要为求新求高而盲目引进。 ⑧ 留有余地,便于在线调试、修改和扩展 在软件设计时,留有余地是必要的。例如,在与门的输入端增设一个高电平的端子(软连接);在或门输入端增设低电平端子(软连接),这利于在线修改时的扩展,而不必重新组建。 ⑨ 优化设计控制算法或模块的使用数量,减少内存和运算时间 优化设计是在DCS软件设计中非常关键的一步。由于工期限制,加上用户经验较少,所以,DCS用户组态过程中常会出现类似“搭积木”的方式进行软件组态,结果使方案庞大,系统负载较大。因此,在用户组态的后期进行优化设计,选择更加合适的模块或算法,做到方案精简,功能齐全,从而减少内存和运算时间,降低系统负载。
|