李红星,刘晓飞,许亚军
1 电气负载平衡优化研究的数学模型及核心原理 直流调速系统负载平衡问题的技术日益成熟,这里主要针对交流调速系统进行研究。笔者采用了类似直流系统的双闭环动态响应系统为模型:速度外环和转矩内环双闭环。其原理图如图1所示。
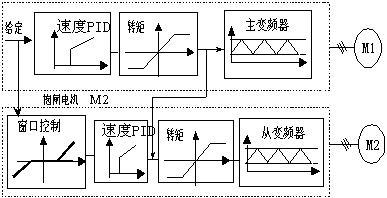
图1 系统核心原理图
因为MASTER的转矩调节器输出是FOLLOWER(从机)转矩调节器的给定值,因此如果MASTER电机负载增大或减小,同轴运行控制系统能自动使FOLLOWER电机自动减小或增大负载,保持电机之间及两台变频器之间在任何情况下都能平衡分配负载。 在正常的运行范围内,FOLLOWER的速度调节器(speed controller)输出为零,从机时刻跟随MASTER的转矩给定(torque ref1),保持了负载的平衡。如果主从机速度略有偏差(速度给定值-实际转速值),且速度偏差处于一定的窗口范围内,FOLLOWER的窗口控制(window control)将使从机速度调节器的输入和输出保持为零,从机跟随主机的转矩给定(torque ref1),满足负载的速度平衡要求。 如果速度偏差超出窗口范围,窗口控制把偏差与速度调节器相连,速度调节器输出增加或减少内部转矩给定,停止转速的进一上升或下降,直至达到新的平衡。 2 中板精整线翻板机目前存在状况 中板机组精整线翻板机是由两台交流电机驱动,两台减速箱一级轴之间通过齿轮硬性连接同步拖动机械设备,是重载频繁升降的重要设备。电机及运行参数见表1,型号为YZR315M-10 75kW 164A 582RPM。
表1 改造前技术数据
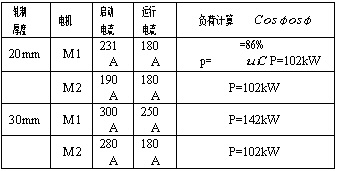
由表1可知,由于控制采用交流电子开关柜控制系统,全压启动电流较大,电气负载严重不平衡,产生了翻板机的承载机构支杆经常性折断和扭曲变形,严重的机械冲击力造成减速箱的固定地脚松动而左右摆动,电机地脚掰断等,这使设备的维修周期缩短,生产效率降低。 3 系统改造设计及要求 (1) 变频器选型 因为是同轴驱动相同的负载,所以两台变频器频率输出、频率变化都应该保持严格的同步关系。如果其中一台电机负载增大或减小,同轴运行控制系统能自动使该台电机自动减小或增大负载,保持电机之间及两台变频器之间在任何情况下都能平衡分配负载。 笔者对变频器进行了严格选型,从日本富士、法国施耐德到ABB公司的变频器中,全方位进行研究:功率系统、控制触发系统、保护系统、电机识别系统、应用程序集成系统、网络拓展系统。考虑到ABB ACS604 系列变频调速器具有独特的方面: ① DTC(direct torque control)技术和模糊控制理论合二为一,性能优于矢量控制变频器。 ② 具有标准的内置交流电抗器,大大降低了变频器的电磁辐射及电流冲击。 ③ 应用程序集有独特的主/从应用宏,主/从应用宏是为多电机传动应用而设计的,其系统由若干变频器共同驱动,同时电机轴经由齿轮、链条、皮带等相互连接。由于有了主/从应用宏,保证了电气负载在电机之间均匀分配。 所以,采用ABB ACS604变频调速器,并为将来系统电机功率的增容作了进一步考虑,最后选用ABB ACS604系列160kW变频调速器来突破中板精整线翻板机电气负载平衡的问题。 (2) 系统设计简图和控制原理简图 中板机组翻板机传动系统是由两台交流电机拖动,确定负载重的电机作为主电机,实施速度控制,另一台作为从电机,实施转矩控制,从电机动态跟随主电机转矩的变化而变化,有效地控制负载的平衡。该系统方案的主电路如图2所示,控制电路如图3所示。 4 系统调试要点与体会 (1) 建立主从关系的参数 主机中:60组的01、02、07、08项分别设为Master、Speed、202、213;从机中:10组的01、02项均为Comm.module;60组的01、02、07、08项分别设为Follower、Torque、202、213。 (2) 主从之间的给定 主机中:11组的01、03、06项分别设为Ref1、keypad、keypad;从机中:11组的01、03、06项分别设为Ref1、Comm Ref、Comm Ref。 (3) 主从之间的光纤选通 主机中:11组的02项设定为EXT1;从机中:11组的02项设定为EXT2。 (4) 主机不需要电机自动辨识运行,只需从机进行电机自动辨识运行即可。 (5) ACS600的减速类型应选择主机和从机都采用自由惯性停车方式,不能采用斜率方式停车。因为,斜率停车方式下,机械抱闸动作时变频器没有完全停止供电。 (6) ACS604变频器的数据给定采用键盘给定方式,以减少外部电压或电流给定方式带来的误差和故障机率。
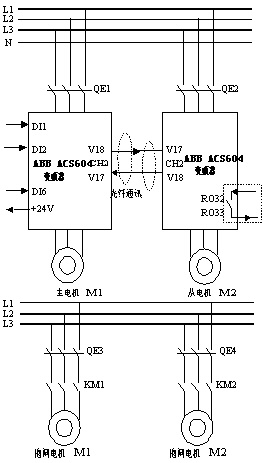
图2 系统方案的主电路
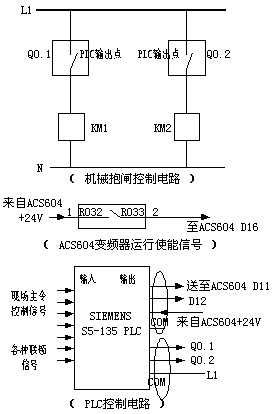
图3 系统方案的控制电路
5 运行实际效果 控制系统改造后,经过实际生产运行观察电机特性参见表2。
表2 改造后技术数据
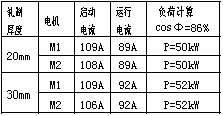
|