关键词:DCS-NET;RSVIEW;OPC
林清泉 男,福建南平铝业有限公司电解分厂电解设备部自动化控制工程师,福建南平铝业有限公司,福建 南平 353000
1 系统概述
南铝1号铸轧机为南平铝业有限公司于1995年引进的意大利FATA HUNTER公司1800×1003超型铸轧机,其年设计产能15kt,可生产1000、3000、5000系列合金铸轧带材。这套设备采用了独特的闭环冷却水系统,很好地解决了超型轧机生产过程中对轧辊冷却能力和辊面温度的特殊要求。设备控制和传动系统均采用美国RELIANCE公司的产品。其中设备控制系统为RELIANCE AUTOMAX DCS控制系统,控制系统网络结构如图1所示。
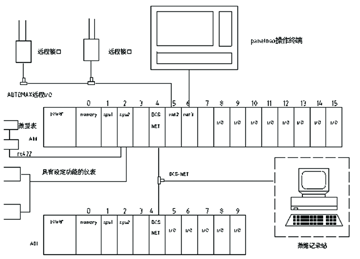
图1 控制系统网络结构图
该控制系统由A00、A01两套Automax控制器(每套控制器配置双中央处理器),一个Panelmax操作终端,一个数据记录站,多个远程I/O站(包括电机控制中心,阀站I/O柜,卷取机操作台等),Automax传动控制器,各类仪表等组成。其中A00为AutoMax主控制器,A01为AutoMax控制器用于铸嘴直流传动装置控制。其中CPU1、CPU2为 Automax processor 57C431模块(中央处理器),其中DCS NET为Automax Network Communications Module 57C404模块(DCS NET通讯模块);其中net2为Automax Remote I/O Communications Module 57C416模块(远程I/O通讯接口模块);其中net3为AutoMate Interface Module 57C417模块(RS-232通讯模块)。
该系统中有四种网络接口方式,第一种网络接口方式即DCS-NET ,它联系了A00 控制器、A01 控制器和原来的数据记录站(现在已无法使用);第二种网络接口方式即AUTOMAX远程I/O网络,它联系着电机控制中心、阀站I/O柜、卷取机操作台等;第三种网络接口方式即RS422网络,它联系着中央处理器与数显仪表;第四种网络接口方式即RS-232,PanelMax操作终端采用的就是通过串行(RS-232)方式连接到控制器系统57C417模块上。
2 存在问题
南铝1号铸轧机操作终端PANELMAX为Reliance老产品,设备已经老化,PANELMAX已经淘汰停产,备品备件无法采购。PANELMAX故障率较高,容易影响生产,原数据记录站已经不能使用,生产部门需要对1#铸轧机生产和设备情况进行历史记录跟踪追溯、故障查询分析以及管理信息系统提供生产实时数据,故决定对其进行改造。
3 改造方案
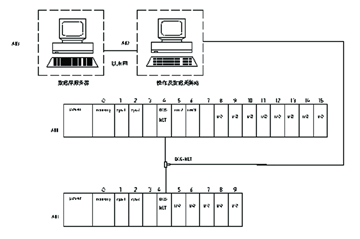
图2 改造方案图
如图2所示, 把原操作终端PANELMAX和原数据记录站取消,替换成操作及数据采集站和数据库服务器。操作及数据采集站位于现场铸轧机台旁,操作及数据采集站增加ROCKWELL公司的DCS-NET板卡,接入原数据记录站的通讯网络DCS-NET上。操作及数据采集站采用ROCKWELL的RSVIEW32组态软件和DCS-NET SERVER驱动软件,重新设计制作上位机软件和编制DCS控制程序。数据库服务器位于监控室内,与操作及数据采集站用工业以太网联系,在数据库服务器上安装有SQLSERVR2000关系型数据库,操作站从控制系统提取的数据就存放SQLSERVER2000数据库内,在数据库服务器也可运行RSVIEW 32读取历史数据库内的生产数据进行远程监控,或通过防火墙隔离后接入公司管理局域网络,再通过VB、DEPHI等从数据库服务器中提出铸轧生产实时数据为上层管理系统使用。
4 新系统的设计与实现
本系统主要针对原来的数据记录站系统进行改造,兼容数据记录站和PanelMax操作终端的功能。原数据记录站系统主要的功能是进行数据采集和存储,并形成报表对生产数据进行记录,但已无法使用。改造后的操作站采用计算机系统,并增加相应组态软件对数据记录站功能进行扩展,除了保持原来对数据记录功能外,还增加了生产数据设置和监控的功能。所以新系统可完全替代PanelMax。
原来的数据记录站通过Reliance公司的DCS-NET板卡连接到Automax的DCS-NET网络。通过DCS-NET网络和两台Automax控制器交换数据。由于原数据记录站只是采集生产过程的数据,即只读功能,而改造后的操作站需要设置生产过程中的参数,所以需要对DCS-NET进行重新配置和组态,使之能够对AUTOMAX内的数据进行读写。另外,改造后的操作站需要完全替代Panelmax的功能,PanelMax上的参数设置都必须在操作站上实现。PanelMax采用的是57C417模块通过串行(RS-232)方式连接到控制器系统,而DCS-NET采用的是57C404(DCS-NET)方式,两个网络连接的数据目标区不是同一个地址,所以需要在AUTOMAX内对任务进行修改,将两方对数据区映射,指向同一个目标地址。
DCS-NET网络地址在AutoMax硬件配置内进行组态。其中AutoMax主控制器在网络中地址为0,为网络的初始化节点。网络建立后由初始化节点对其他的地址1以后的节点进行查询,并对其进行初始化。打开57C404模块的配置窗口,可以看出每个节点占用了64个字的地址映射区,这64个字对于本节点都是可读写。但是对于其他节点,0~31字为只读区,32~64字为读写区。本系统中,将改造的操作站配置了3#、4#、5#共占用了3个节点地址,所以操作站计算机可以有192个字的网络地址空间。通过网络配置(Automax软件上配置),0#初始化节点和1#节点将状态字写入到3#、4#、5#节点的0~31字地址空间。对于0#、1#节点,3#、4#、5#节点的0~31字地址空间为读写区,而对于操作站本身,0~31字地址空间为只读区。完成自动的映射配置后,将配置组态下载到0#节点(初始化节点),DCS-NET网络即可自动完成数据通讯到操作站计算机上。操作站上的计算机只需通过DCS-NET板卡的驱动程序对数据区进行读操作即可获取现场设备的状态。同样的方式,3#、4#、5#节点上的32~64字地址对于操作站为读写区,所以生产参数直接写入到此地址空间即可经DCS-NET网络传送到0#和1#节点参数区。
DCS-NET网络配置完成后,数据的读写和交换均在网络上的数据缓冲区进行,即上述的每个节点拥有的64个字的地址空间。原来的PanelMax采用的是57C417模块RS-232方式连接。57C417模块本身有自己的内部数据缓冲区,PanelMax读写的即是此数据区的内容,和DCS-NET数据区无关联,所以需要在Automax内部建立一个运行任务将PanelMax的数据区映射到DCS-NET中。改造的系统通过新增一个Pas任务,采用BASIC语言编写变量映射语句对两个网络的数据进行读写映射关系即可。
Automax任务对地址读写操作均采用变量的方式,没有直接读写实际的地址。在编写程序之前,组态硬件的时候需要在Automax配置窗口上定义每个地址的变量名。PAS任务直接对变量名进行操作。
完成网络配置和两个网络的变量地址映射程序后,操作站上已经可以对控制器内的数据进行读写操作。也就是说操作站计算机可以和AutoMax控制器进行数据交换,需要完成人机界面的任务。改造的系统在操作站计算机上安装有RSView32组态软件。RSView32组态软件同样属于ROCKWELL公司的产品,可以很好地兼容AutoMax的DCS-NET网络协议。系统驱动层软件为RSLinx软件,RSLinx软件采用驱动的方式连接DCS-NET板卡,读写DCS-NET网络数据。RSLinx软件向上提供OPC接口。OPC接口为标准的软件接口,RSView32组态软件作为OPC客户端连接到此接口即可进行数据交换,而无需关心DCS-NET网络的通讯过程,使系统更为可靠。
RSView32软件本身有一个实时数据库,从DCS-NET网络过来的数据存放到实时数据库中。RSView32软件通过组态画面中的显示元件(数据显示、指示灯、数据输入等)读写实时数据库数据。另外,RSView32软件具有历史数据存储功能,按照一定的时间间隔将实时数据库采集到的数据存储到MS-SQLServer数据库。RSView32本身的曲线控件自动读取MS-SQLServer数据并以曲线的的方式显示生产参数变化趋势。在今后也可将数据服务器通过防火墙隔离后接入公司管理局域网络,再通过VB、DEPHI、ASP等高级语言编程后从数据库服务器中提出铸轧生产历史数据为上层管理系统提供数据服务。
本次改造针对AUTOMAX的PANELMAX操作界面,用计算机替代原来的PANELMAX的全部功能,并在此基础上全面对操作方式、功能及界面等进行升级。总原则上沿袭PANELMAX的操作习惯及画面布局,最大程度上保持操作人员使用方式的适应。并且对原来英文文字说明全部汉化,使之更直观。功能上处理原系统的所有操作功能外,增加了历史记录、数据保存及曲线查询的功能。系统采用计算机连接到AutoMax的DCS-NET网络中进行数据交换,实现生产过程中的数据显示和生产参数的设置,作为PANELMAX操作终端的功能替换。操作上基本与PANELMAX相似,并在内容上有增强。系统实现了参数设置与运行过程中数据显示,报警状态显示等功能。参数设置包括:铸嘴位置、上下辊的辊径、卷径、带材参数、辊参数、合金参数等,通过控制权限切换都能修改所需的数值。根据系统的组成部分,分别显示:前箱、上下辊、卷取及冷却水等相关内容。若干重要参数采用棒图显示,并且在超过上下限时以闪烁的方式突出效果。另外各运行过程画面均用数值显示状态。状态值主要为:温度、速度、电流、水温、预载力以及带材的数据等。计算机中显示的数值均能正确反映设备运行状态。各运行过程状态量均设置了上下限报警值,并且此报警值可通过计算机画面进行调整。相应地在棒图中根据报警值的大小,当过程量超限时均发出报警信号。运行中的上辊、下辊及卷取故障点,如电机故障、编码器故障等,在单独的画面中显示,利于故障原因的查找。系统采用SQL-Server进行生产过程中的数据记录。为更直观地显示运行状态变化趋势,所以按照主机、卷取、带材参数、冷却水、轧制力及前箱等各部分采用趋势曲线的方式进行显示。操作人员可按照时间进行设定查询。对于关键的操作:切换计算机操作权限、退出系统等操作,系统设置了密码功能。密码可由用户自行更改。
5 结束语
南铝1#铸轧机控制系统采用的是美国Reliance公司的DCS控制系统,其通讯协议不开放,系统较老(1994年投产)改造时容易出现意想不到的情况,允许停机调试时间只有4-8小时,停机造成的损失很大。之前国内未有成功改造例子,此次南铝1#铸轧PANELMAX及数据记录站系统的改造成功为国内首例,对国内铸轧机Reliance DCS系统的改造都有很强的借鉴意义。改造后的系统于2006年9月底投入试运行,经过两个多月时间的试运行正式投入使用,改造至今设备运行情况良好。
|