李 宏(1972- ) 男,甘肃兰州人,工程师,(浙江国华浙能发电有限公司,浙江 宁波 315612)浙江国华浙能发电有限公司生产技术部,从事电厂热工技术管理工作。
摘要:本文介绍了浙江国华浙能发电有限公司一期4×600MW机组的脱硫岛控制系统的结构和控制范围,并简述了FGD_DCS与脱硫废水PLC之间的通讯接口方式;并以出现的通讯冗余问题为案例,详细介绍了问题的原因和处理的措施;经过程序的修改和完善,有效地解决了机组存在的隐患,提高了机组安全和经济运行的水平。
关键词:600MW机组;FGD_DCS;PLC;通讯
Abstract: This paper introduces the control system architecture and control range of the desulfurization island in Zhejiang Guohua Power Company (4 ×600 MW units), and outlines the communication interface mode between FGD_DCS and desulfurization wastewater PLC. The occurred communication redundant issues are taken as a case study to describe the causes and troubleshooting in detail. The existing hidden trouble is effectively solved in units and the level of unit safety and economic operation are improved by means of procedure modification and perfection.
Key words: 600 MW Unit; FGD_DCS; PLC; Communication
1 前言
浙江国华浙能发电有限公司一期4*600MW机组为国产亚临界燃煤机组,同步建设4台烟气脱硫装置。一期工程于2003年11月27日开工,按照#2、#3、#1、#4号的建设顺序分别在2005年12月、2006年5月、8月和11月完成168小时试运后投入商业运行。
脱硫系统采用日本川崎烟气脱硫技术,脱硫塔塔型为喷淋塔。脱硫工艺系统包括:烟气系统、吸收塔系统、石灰石浆液制备系统、石膏脱水系统、脱硫废水处理等主要工艺系统和浆液排空、工艺水、冷却水、压缩空气等辅助系统。
4台机组的脱硫工艺系统,通过脱硫岛分散控制系统(FGD_DCS)集中控制,产品选用西门子T-XP控制系统,由操作员站、工程师站、冗余配置的数据高速公路及控制器等所组成,不设置常规仪表和硬手操设备,仅保留独立于DCS系统的“紧急开旁路档板”手操按钮。
在脱硫电控综合楼设有四台兼有工程师站功能的本地操作员站,在主厂房集中控制室设置四台FGD_DCS操作员站,运行人员可通过FGD_DCS的操作员站对四台机组脱硫系统进行监视控制,对脱硫废水系统和主机电除尘等系统进行远方监视和操作。
2 脱硫废水工艺控制
宁海电厂脱硫岛,由于采用控制室集中监控方式,因此脱硫废水处无人监控,就地只设有调试接口。现场设备的运行状态及工艺参数直接进入PLC后,与FGD_DCS系统的操作员站进行数据交换。FGD_DCS系统的操作员站可显示现场各设备的状态,包括各流程检测点的运行状态及各测点参数变化,当测量信号和运行状态异常,报警并生成报警记录。
脱硫废水处理系统,包括脱硫装置废水处理、化学加药、污泥脱水三个子系统,其中:
(1)脱硫装置废水处理系统工艺流程
脱硫废水→中和箱(加入石灰乳)→沉降箱(加入FeClSO4和有机硫)→絮凝箱(加入助凝剂)→澄清器→清水pH调整箱→排放。
(2)脱硫废水处理加药系统
石灰乳加药系统;FeClSO4加药系统;助凝剂加药系统;有机硫化物加药系统;盐酸加药系统等。
(3)污泥处理系统流程

脱硫废水控制采用三种控制方式:程控自动、程控点动及就地操作。通过上位站监控现场每一设备,无需人员去现场手操设备,减少了操作员的工作量,实现了方便可靠的控制室集中监控。
3 脱硫控制系统和废水PLC通讯
(1)FGD_DCS侧通讯
FGD_DCS侧通过CM104通讯卡与PLC进行通讯,每次CM104起动时,都可以通过串口建立一次CMLink连接,并由CMLINK.EXE来进行数据的检测和控制,CMLINK.EXE程序文件在CM104的FLASH存储器中。
CmLink的缺省设置为:57600波特率;8位数据位;1位停止位;无奇偶校验;必须激活RTS/CTS控制(硬件协议);终端程序的参数需要设置相同的传输速率。 通讯的物理连接如图1所示。
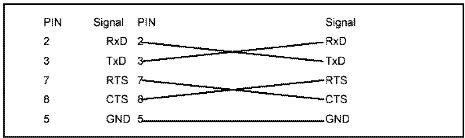
图1 物理连接图
(2)FGD_DCS与PLC之间通讯
脱硫废水控制系统采用AB公司的可编程控制器(PLC),完成对工艺过程的自动控制,设计过程I/O点数共计372点;通过对主要参数PH、浊度等监控和调整,最终实现合格排放。废水控制PLC通过冗余的通讯接口与FGD_DCS进行双向通讯,最终实现通过FGD_DCS操作员站对废水工艺进行远方监视和操作的功能要求。脱硫PLC选用AB ControlLogix5555处理器,PLC内部使用双机热备系统;FGD_DCS与脱硫废水PLC之间的通讯为MODBUS协议,脱硫废水PLC做从站,从站地址是1。通讯结构示意图如图2所示。
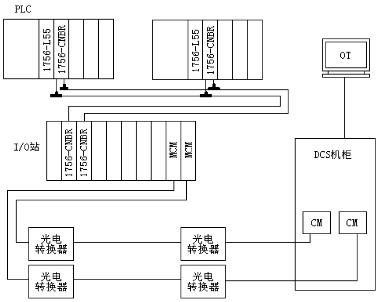
图2 通讯结构示意图
脱硫废水PLC与FGD_DCS之间通讯采用两块MVI56-MCM模块,实现双路通讯。就地设备状态信号通过PLC的MCM模块转换成为MODBUS协议的信号,经过光电转换模块转换成为光信号,通过光缆送到脱硫DCS控制柜,在DCS控制柜内,首先经过光电转换模块转换成为MODBUS协议的电信号,送至DCS的CM模块,最后送到DCS系统。通讯接口采用RS-485光纤通讯,通讯协议为MODBUS。PLC与FGD_DCS之间MODBUS数据通讯格式如表1所示。
表1 PLC与FGD_DCS之间MODBUS数据通讯格式
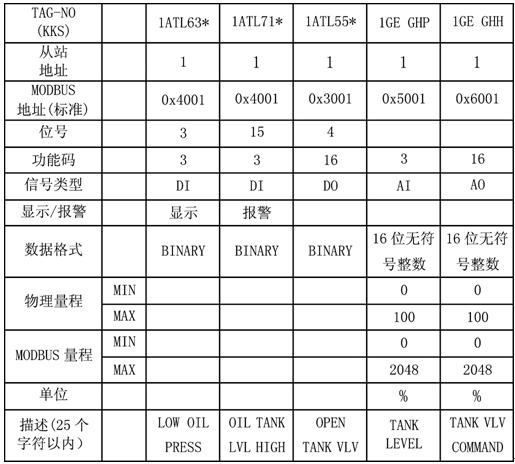
PLC系统采用双机热备配置,PLC 的CPU选用1756-L55M13型号,该系列产品的模块可带电插拔,该系列产品既可以控制本地I/O又可以通过ControlNet网、DeviceNet网及远程I/O网控制远程I/O。宁海电厂选用ControlNet网来控制远程I/O,传输速率可达5Mbps,通讯介质为同轴电缆。
通讯模块MVI56-MCM是Modbus网络和AB PLC之间的一个网关。处理器的数据传送异步于Modbus网络上的数据活动。模块内部具有5000个字的寄存器,用于处理器和Modbus网络之间的数据交换。
在AB PLC 系统中,MVI56-MCM模块共有3个端口P1、P2、P3:
● P1为设置/调试端口,无数据传输
● P2为数据传输端口
● P3为数据传输端口
MVI56-MCM与FGD_DCS通讯通过P2端口实现,即两路Modbus通讯电缆均连在MVI56-MCM模块的P2口。 系统端口原配置信息为设定使用MODBUS端口,定义类型为MODBUS主从方式,无pass-through功能,有效协议为MODBUS-RTU。
4 通讯问题案例分析
原系统的通讯冗余设计,保证了集中控制室对就地设备不间断控制和监视的可靠性,符合就地无人监守,远程自动控制的思想。脱硫岛实现脱硫废水的控制,减轻了运行人员的劳动强度,在很大程度上提高了生产效率。但不同系统之间的通讯,需要建立同一的数据规范和稳定的数据流,以确保其稳定可靠运行。下面就FGD_DCS和PLC之间出现的通讯问题案例进行分析。
由于脱硫废水调试期较短,通讯的一些问题未完全暴露。当自脱硫废水系统投运后,通讯不稳定的情况出现,由两路通讯模块送至PLC的开关量信号,多次出现不一致的现象,导致设备误动或拒动。
例如图3所示的一段程序,实现两台泵(溢流坑#1排污泵与#2排污泵)的投运方式控制。
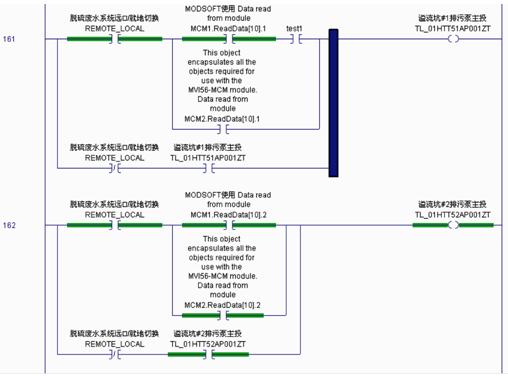
图3
其中MCM2.ReadData[10].1和MCM2.ReadData[10].2 分别代表MCM1和MCM2的一路通讯,其变量的变化是从脱硫DCS系统读取过来的信号。
上述程序可以看出:第161行MCM1.ReadData[10].1和MCM2.ReadData[10].2信号存在同时为“1”的情况,其中任何一路来“1”都是有效的,这样PLC输出#1泵和#2泵主投均投入的现象;而实际操作是运行人员在FGD_DCS画面中选的是#2泵主投,所以图中程序中的MCM1.ReadData[10].1信号为“1”是错误的,按照要求输出应为“0”,所以在问题未解决前,暂时在程序中增加一个空的变量“test1”进行隔离。
双路通讯信号未能有效的相互闭锁对设备控制来说是一个较大的隐患,将造成设备的误启和误跳事件发生,影响工艺系统的稳定运行。发生该问题的主要原因,是中间数据变量未能有效辨识,需要对数据进行判别和数据流重新定义。
5 通讯问题的解决和优化
通过对MVI56-MCM模块参数和程序的仔细检查和深入研究,可以发现原程序中,端口2类型配置为“1”,即MCM1.Port2.Type的设置类型采用SLAVE 方式。
在这种方式下,当MVI56-MCM 模块处于从站驱动模式时,模块可以响应来自于Modbus网络上主站设备发出的数据读和写命令。下面通过图4并结合表1来详细说明进出模块的数据流动。
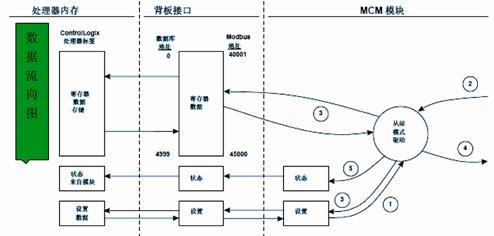
图4
首先MODBUS从站端口驱动从ControlLogix处理器接收设置信息,用这些信息设置串口,并且定义从站节点特征。然后主站设备向模块节点地址发送读或写的命令,端口驱动在接收前进行验证。一旦命令被接收,数据立即传输到从模块的内部数据库;如果是读命令,数据从数据库中读出并创建相应信息;如果是写命令,数据直接写入到数据库中并创建相应信息。当处理过程结束后,模块相应信息到主站。在状态数据库中计数器使梯形逻辑图对从站的状态进行判断。
在原设置的条件下,数据流从站相应驱动后送至寄存器数据缓存,经过状态判断后送往寄存器数据存储。而出现问题的在于判断失效,直接反映在程序上是控制设备的两路通讯信号不能有效识别。
针对上述问题,笔者在新程序中,将端口2的设置,即MCM1.Port2.Type的类型配置为“4”,即格式化pass-through 方式。
在这种模式下,所有写请求会直接传递到处理器,而不是放到数据库里,这就能够避免计数判断或重复判断产生判断失效;在没有中间数据库的条件下,直接传输到控制处理器,解决了系统原来部分点在FGD_DCS操作系统中发生异常的现象。
图5阐明了pass-through 功能开启后从站端口的数据流:
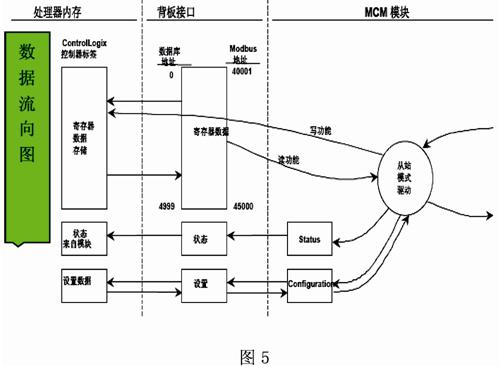
同时,笔者在原程序的基础上,对应Pass-through方式下的通讯设置和处理,分别增加并修改了6个程序段:PowerUp程序段、ModSoftConfig程序段、 ReadData1程序段、 ReadData2程序段、WriteData1程序段、WriteData2程序段等内容(具体程序略)。
在程序设置中,将控制方式由“SLAVE”模式修改为“Pass-through”模式;增加程序启动后状态监视和判断的条件,对读数据及写数据进行统一完善。通过“先进行类型判断,然后与最后值比较,状态判断,统一数据的最终缓冲后直接写入数据存储区”,保证了数据的唯一性。
6 结束语
由于在AB PLC系统的MVI56-MCM通讯模块组态中,采用了新的数据控制流方式,从而有效解决了冗余通讯信号的辨识问题,保证了在FGD_DCS上对脱硫废水系统工艺设备操作的可靠性和逻辑操作中的唯一性。本文可以为在其它类似系统的逻辑组态提供一定的借鉴和参考作用。
电厂热控系统是一个庞大而复杂的系统,随着电厂技术包括DCS、PLC等技术的不断发展和控制范围的不断扩大,许多新的问题将不断涌现。但通过经验的不断积累和信息的交流,热控系统的可靠性也将不断得到提高。
参考文献:
[1]火电厂热工自动化系统试验[M].中国电力出版社,2005.
[2]T_XP工程师手册.南京西门子电站有限公司,2006.
[3]AB PLC 编程手册[M].AB公司,2004.
|