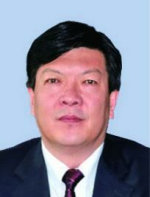
潘钢,男,现任北京国电智深控制技术有限公司总经理。潘钢自1982年大学毕业后一直从事自动化专业工作至今。通过直接参与数百个项目工程,掌握了火电领域自动化专业可行性研究、产品和工艺设计,产品和应用研发、产品制造、产品应用等全过程知识。几十年来,带领团队通过推广应用1000多套国外主要自动化控制系统产品和自主研发的国产自动化控制系统产品,完全掌握了大型自动化控制系统的核心技术,进入国际先进行列。获得多项科技进步奖等多项荣誉,发表论文多篇。
摘要:本文介绍了大连庄河电厂600MW超临界机组一体化平台主辅控DCS系统的总体结构、系统功能和配置情况,并对系统和功能设计上的主要特点进行了分析。 关键词:DCS;EDPF-NT;超临界机组控制;辅控一体化
Abstract: This paper introduces the general structure,system function and configuration of the main and auxiliary shop DCS for the 600MW Supercritical Unit in Dalian Zhuanghe power plant.The main features of the system have been analyzed. Key words: DCS; EDPF-NT; Supercritical Unit Control; Auxiliary Shop Control
1 项目总体情况
国电电力大连庄河发电有限责任公司2×600MW国产超临界机组采用北京国电智深控制技术有限公司(国电智深)自主知识产权的EDPF-NT分散控制系统实现主辅控系统的控制,这是国内第一个采用国产自主化DCS系统的600MW超临界机组项目,也是国内第一个采用一体化系统平台实现600MW超临界机组主控和辅助车间控制的项目。
该项目是《国家科学仪器和工业自动化高技术产业化重大专项-超临界火力发电机组综合自动化系统产业化项目》和《大型火力发电机组分散控制系统国产化项目》的依托工程。同时作为首台套应用于600MW超临界机组的自主化控制系统项目,该项目于2006年4月被国家发改委确定为落实《国务院关于加快振兴装备制造业的若干意见》的第一个技术进步示范工程。
该项目于2006年2月26日正式启动,2006年11月29日中国国电集团工程部组织了国内知名专家参加的出厂验收评审会,与会专家一致认为:“应用EDPF-NT系统设计成套的国电电力大连庄河发电有限责任公司一期2×600MW机组自动控制系统配置合理、技术先进、功能齐全、质量可靠,符合技术规范要求,同意通过出厂验收,可以在600MW级超临界机组上应用”。经过紧张的现场调试工作,2007年8月6日庄河电厂#1机组顺利通过168小时满负荷试运行,#2机组于11月5日通过168小时满负荷试运行,配套辅控系统也同时投运,实现了在集控室对主辅控系统进行集中监控。在168小时满负荷试运行期间,自动投入率95%,保护投入率100%,机组协调控制一直投入并成功实现AGC控制,负荷、主汽压和主汽温等主要参数的控制精度均达到或超过电力行业标准。
2 主控DCS系统
系统总体结构如图1所示。
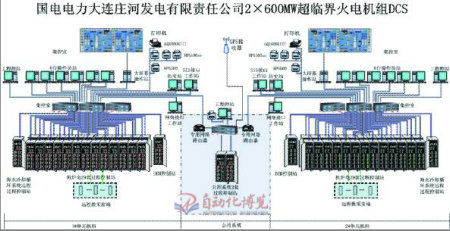
图1 主控DCS系统总体结构图
主控DCS系统分为3个域,#1单元机组域、#2单元机组域和公用系统域。单元机组域和公用系统域之间采用自主研发的专用路由器进行硬隔离。
2.1 系统网络结构
系统网络结构分为两层:
· I/O总线:负责控制器(DPU)和I/O之间的通讯,电气协议采用RS485,通讯速率2Mbps,为冗余I/O总线。采用自主研发的EDPF-NT专用光纤收发器通过光缆连接可将I/O总线扩展到3000米远处。
· 管控网:实时信息主干网,负责DPU之间以及DPU和上位机(操作员站、历史站和工程师站等)之间的信息传输,采用交换型工业以太网,通讯速率100Mbps,冗余容错。
系统网络结构有如下主要特点:
(1)整个系统没有使用专用的服务器,无单点故障点,是较为完善的分布式系统架构。任何故障都将被限制在有限范围内,决不会导致系统崩溃,真正实现了功能分散、危险分散。
(2)管控网采用冗余双网,在软件上采用双收双发的工作方式,双网同时工作,不存在双网切换问题及切换时间问题。
(3)采用专用路由器实现单元机组域和公用系统域之间的硬隔离,保证了单元机组部分与公用系统部分之间的网络相对独立,同时通过路由器,实现了两台单元机组和公用系统之间操作信息和数据信息的有效单向传输,实现了两台单元机组对公用系统的操作备用和操作互锁。
2.2 功能及配置
庄河电厂主控EDPF-NT系统功能包括DAS、FSSS、SCS、ECS、MCS、DEH、ETS、MEH、METS和BPS等,锅炉吹灰由PLC实现,通过通讯方式在DCS系统中进行操作。该套系统实现了锅炉、汽机、给水泵汽机、汽机旁路的控制和保护及电气开关的控制,是目前国内火电厂主控系统采用单套DCS实现功能最齐全的系统之一,在已投运的国产DCS系统中是功能最多的,真正实现了主机的一体化控制。单元机组和公用系统I/O测点数量达到8200点,通讯点数量达3869点,系统标签量达38015点。控制设备776个(其中马达160个、电动门/电磁阀495个、电气开关121个),模拟量调节设备140个。具体测点数量统计见表1。
表1
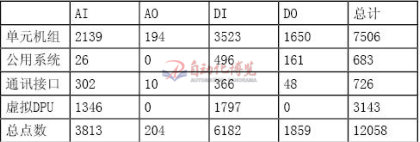
单元机组共配置控制器29对(含DEH控制器2对、MEH控制器2对),公用系统配置控制器2对。公用系统只含电气公用部分,循环水泵房控制纳入对应的单元DCS,其它通常纳入公用系统的内容如燃油泵房、空压机房、汽水取样等全部纳入辅控DCS中。单元机组配置工程师站2台、操作员站6台、历史站1台、大屏幕操作站2台和通讯接口站2台,公用系统配置工程师站1台。各DPU控制内容分配见表2。
表2
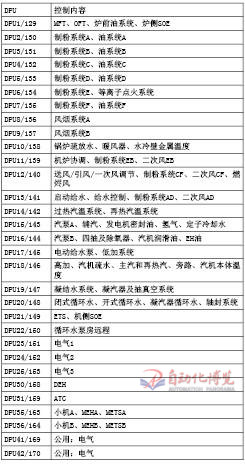
3 辅控DCS系统
庄河电厂辅助车间控制系统(辅控系统)也采用EDPF-NT分散控制系统实现,其中烟气脱硫控制DCS系统采用独立的网络结构,辅控系统其余部分采用一体化网络结构。一体化辅控系统控制范围覆盖水、煤、灰、燃油、暖通、空压机等系统,其中输煤程控、电除尘、启动锅炉、制氢、制氯采用PLC控制,通过专用通讯卡、虚拟DPU通讯方式,采用MODBUS、MODBUS TCP/IP等通讯协议接入辅控DCS系统,实现在集控室对全厂辅助车间进行集中监视和操作的功能。整个网络设计为多层、总线型工业以太网,辅控车间一体化网络结构图见图2。
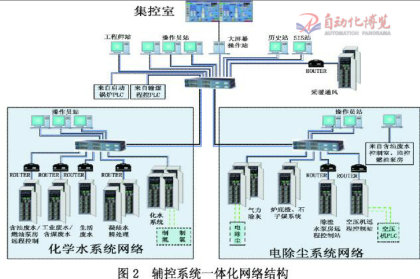
辅助车间DCS系统设计为三层总线网络,最上面一层为集中控制室网络,中间一层为化学水系统网络和电除尘系统网络,最下面一层为各个子车间网络。每层网络均采用冗余双网(A网、B网)。子车间网络通过路由器与中间层网络连接在一起,路由器具有隔离性,以保证操作指令自上向下传递,而同级网络之间不能互相操作。
其中化学水系统网络包括:含油废水/燃油泵房、工业废水、含煤废水、生活废水、凝结水系统、制氢、制氯等系统。化学水控制室设有3台操作员站,实现对以上子系统的监控。电除尘系统网络包括:气力除灰、炉底渣/石子煤、除渣水泵房、空压机以及电除尘等系统。
电除尘控制室设有2台操作员站,实现对以上子系统的监控。采暖通风系统直接接入集中控制室网络。集中控制室设有3台操作员站,1台大屏幕站,1台工程师站,1台历史站,1台通讯接口站,从集中控制室可以对整个网络进行监控。此外,每个辅助车间子系统就地各设有1台操作员站,只能对本子系统进行监控。测点统计见表3。
表3

庄河一体化辅控系统共配置21对控制器。烟气脱硫控制系统I/O测点数量为2960点,共配置10对控制器。
4 主要特点及创新点
4.1 适用于600MW超临界机组控制的EDPF-NT系统的突出特点和创新点
(1)在EDPF-NT系统的研发过程中,坚持自主研发并完全掌握核心技术的技术路线,自主研发了适合于发电厂应用的控制器组态软件及控制算法、上位机操作监控软件、全局分布式实时数据库、历史数据存贮实时数据库、基于以太网的实时通信技术及算法等全部核心软件和DPU控制器、各类信号输入输出I/O模块、连接单元机组与公用系统的路由器等关键硬件,EDPF-NT系统是国内自主化程度最高的系统。
(2)采用国产DCS首次实现了大型火力发电厂辅控系统一体化解决方案,采用先进的网络“域”技术,实现了多层分布的辅助车间级控制和集控室集中监控的目标,达到降低成本、减员增效、信息共享、维护方便的效果,提高了辅助车间自动化控制和管理水平,同时使大型火力发电厂的整体控制水平得到了很大的提高。
(3)通过采用基于任务优先级的实时性能改进策略、网络流量控制优化技术、实时数据二次压缩算法、独特的无需切换的冗余双网技术等多项实时网络应用综合优化技术,最大限度地解决了以太网的不确定性问题,以太网的实时性能有了质的飞跃,保证了系统网络的通畅性和鲁棒性,在庄河电厂600MW超临界机组DCS上的实际使用情况表明EDPF-NT系统采用的工业实时以太网络性能优异、稳定可靠,保障了大型控制系统的可靠稳定。
(4)通过高精度的授时装置(如GPS),获取高精度的对时脉冲和绝对时间信号,经控制器(DPU)为分布的各SOE模块提供高精度的同步时钟信号,确保了分布在不同DPU的所有SOE模块的精确时钟同步,保证了整个系统SOE的分辨率小于1ms。
(5)基于硬件隔离和数据库融合技术的公用系统解决方案完全实现了对公用系统的应用要求,网络结构简单清晰,数据的传输与隔离可靠,组态方便,控制操作简便,并且,该方案还确保了不降低网络与系统的安全性能,完全满足600MW超临界机组的应用需求。
(6)采用算法内嵌的方式实现了跟踪状态、串级跟踪、低选跟踪、高选跟踪、升禁止、降禁止、到达高限、到达低限等8种约束状态的判断及在这些约束状态下的快速返回,使算法具有了能动性,很好地提高了控制回路的响应速度,在算法层面满足了600MW超临界机组对控制快速性的要求,有助于提高控制精度和缩短控制过渡时间。
(7)EDPF-NT硬件系统的DPU控制器和各类I/O模块、测控网络都按航天军工标准进行了一系列强化设计,包括模块的密封封装、电子线路的浮空设计、严格的电气隔离和抗强电设计,有效地保证了系统硬件的可靠性。模拟量输入通道间隔离电压达400V,开关通道间、通道同CPU间的隔离电压达1500V,通道本身可以耐220V交流强电。
4.2 庄河电厂600MW超临界机组DCS系统功能设计的主要特点
庄河电厂DCS系统根据600MW超临界机组过程控制的特点,突出强调了工程方案的安全性设计。超临界机组控制对象复杂、非线性强,工质流和能量流耦合严重,机组蓄热量较小,蒸汽参数高要求参数波动范围小,所有这些都大大增加了超临界机组的控制难度,因此需要对其控制进行优化。
(1)全面考虑工艺过程的安全性设计
在工艺过程的安全性设计方面,重点考虑了如下内容:控制器的适度分散与功能合理分配,重要参数的分控制器监视,以单点、单卡故障、单一参数失效不影响某一工艺系统或整个机组安全性为原则的I/O测点分配,以典型驱动算法功能的完善性和逻辑的严密性为基础的设备控制安全性,热工联锁保护的实现方法,模拟量控制回路考虑控制过程的安全性,内容全面和多重且设置优先级的报警,MFT执行部分继电器逻辑设计,ETS和METS继电器逻辑设计,必要的后备操作手段,电源及接地系统,控制逻辑设计与实现的规范性和标准化,控制器主副站同时掉电的极端情况下应对措施等。
(2)严密的机组主保护系统设计
机组主保护系统包括锅炉安全保护系统(FSSS)、汽机紧急遮断系统(ETS)和发电机主保护系统,这些都是机组保护系统的核心。庄河电厂600MW超临界机组锅炉和汽机保护系统均在DCS系统中实现,这就对DCS系统本身和工程方案的设计都提出了更高的要求。在工程方案设计中,重点把握了如下原则:
①安全性原则
a 保护控制器采用单独控制器,冗余配置。
b 采用控制器逻辑和硬继电器逻辑相结合的实现方式,极为重要的跳闸条件(如手动打闸和ETS中的汽机超速)在控制器逻辑和硬继电器逻辑中同时实现。
c 控制器和硬继电器逻辑均采用两套电源供电。
d 保护动作指令回路采用双套设计。
e 锅炉保护跳闸动作指令设计成3个指令三取二方式;汽机跳闸动作4个指令分别送到液压系统4个AST电磁阀,电磁阀采用“两个先或然后再与”的回路布置方式,4个动作指令分别从不同DO卡件输出。
f 重要联锁设备硬指令回路采用双套设计。
g 手动跳闸按钮采用双按钮的接点先并联再串联方式,每个按钮采用两副接点,每个按钮的两副接点先并联,然后两按钮再串联,提高按钮动作的可靠性。
h 跳闸条件尽可能按三取二逻辑设计,且相关IO点从不同卡件输入。
i 加强电源监视。对控制器的两路电源进行监视。对给硬继电器逻辑供电的两套直流电源在切换前和切换后均进行监视,切换后电源的监视点安排在末端。
②快速性原则
根据保护对象的实际要求,尽量提高保护动作的快速性。锅炉保护控制器处理周期为100ms,汽机保护控制器处理周期为30ms。
③跳闸条件的科学性和完善性
认真研读相关的保护规程,严格依据机炉厂家提供的保护资料,深刻理解其含义和必要性,针对庄河超临界机组的具体实际进行完善和优化,在跳闸条件延时和脉冲的使用上慎重考虑。
④硬跳设备的全面性和必要性
严格根据锅炉防爆规程的要求,凡是直接危急到炉膛安全的设备,全部纳入硬跳设备清单。
⑤跳闸首出原因记忆
对于机炉保护,均设计了跳闸首出原因记忆逻辑,便于准确快速寻找跳闸原因。
图3为依据以上原则设计的庄河电厂600MW超临界汽轮机保护系统ETS的继电器逻辑原理图。
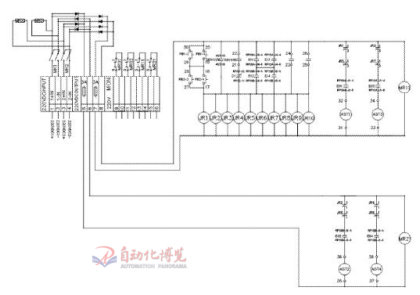
图3 庄河ETS继电器逻辑原理图
(3)对机组协调控制和汽水系统控制进行优化
在协调控制方案中,充分考虑了超临界机组锅炉、汽机特性的差异、燃料、给水的平衡关系和相互影响。给水控制以燃水比为基础,控制住中间点温度(汽水分离器出口微过热汽温),同时考虑给水控制对汽温的影响,将提供快速动态响应的减温喷水与提供稳态汽温调整的燃水比协调起来,使机组燃料和汽水系统控制整体上达到较优水平。启动给水系统按功能组级设计,启动给水系统投入自动后,在机组整个启动、正常运行以及停止过程中,启动给水系统设备完全处于自动控制状态,这有助于实现超临界直流炉从湿态运行到干态运行,以及从干态运行到湿态运行的安全稳定转换。
庄河电厂#1机组168试运期间机炉协调控制、给水控制、过热汽温控制等主要控制回路均已投入,控制精度达到了较高水平。
4.3 庄河电厂辅助车间控制系统采用主厂房控制系统平台(主辅控一体化平台)的主要特点和优点
(1)灵活易用性
由于EDPF-NT系统应用了先进的网络“域”技术,可以方便的在辅助车间一体化系统中加入和退出每个子系统或将子系统重新划分,而不影响整个系统和其它子系统的正常运行,方便了辅控系统的逐步投运以及投运后电厂的检修和维护工作。
采用新一代完全自主产权的聚簇索引技术实时数据库引擎,实现了辅控系统规模大情况下的最高实时数据检索和更新效率,并通过系统内测点名称可重名的动态边界安全保障等功能,解决了辅控各子系统分步实施以及系统在线初始化过程中易出现的冲突和干扰问题,大大增强了辅控系统动态安全性和配置灵活性,方便了辅控各子系统分部实施投运。
(2)系统网络实时、安全、可靠
EDPF-NT系统工业实时以太网采用了多项实时网络应用综合优化技术,现场运行情况表明性能优异、稳定可靠。
(3)系统操作安全,权限设置方便
庄河电厂辅助车间控制系统分为三层,为了系统操作安全,EDPF-NT系统加入了分级操作权限的功能,操作权限可以方便灵活的在不同的层间进行切换(不同的子系统间可以独立切换,不会相互干预),同一时间只有一个层具有操作权限,而且只有得到操作权限的层才能对设备进行操作。
(4)控制器处理能力强
和PLC控制器相比,DCS系统除了具有优秀的开关量运算功能外,同时也提供了强大的模拟量控制功能,可以解决电厂任何复杂的控制方案,并且由于有实时多任务操作系统的支持,对于事件的响应速度更快。
(5)支持多种与第三方设备的通讯接口方式
EDPF-NT系统的冗余虚拟DPU技术和冗余COM卡技术便于实现与各种不同类型大小规模的其它系统的通讯控制。在庄河辅控DCS系统与输煤程控(PLC)等系统的通讯控制上就充分采用了这些技术。同时借助于DCS成熟标准的网络接口技术和开放的性能,辅助车间控制系统很容易将数据传输至全厂实时信息监控系统。
(6)经济效益明显
①由于辅助车间控制系统采用一体化设计,真正实现了辅助车间集中监视和控制,达到资源共享,合并减少或取消就地操作监控点,自动化水平提高,为电厂的减员增效起到了很好的作用,也为电厂的辅控车间级最终取消运行人员进而实现全部监控提供了可能。
②主辅控采用一体化平台,即全部采用EDPF-NT系统,大大降低了备品备件数量,优化了电厂资源配置,减少了维护费用,降低了产品成本,为增强电厂的市场竞争力提供了重要保证。
③主辅控采用一体化平台,对于热控维护人员,可以不用学习和掌握多种控制系统,避免了杂而不精的情况出现,同时减少了培训费用,也降低了热控人员的维护工作强度。
④辅控系统依靠EDPF-NT系统先进的计算机技术、网络通讯技术和控制技术,合理有效地提高了辅助系统的控制水平,提高了辅助车间自动化控制和管理水平,提高了电厂运行的经济性。
5 小结
庄河电厂600MW超临界机组主厂房和辅助车间控制系统的成功投运,是国电智深自主化EDPF-NT系统继2007年初在河北龙山600MW直接空冷亚临界机组上成功应用后,取得的又一项重要突破,是国内第一套成功用于600MW超临界机组上的国产DCS系统,也是国内第一套大规模应用于600MW超临界机组辅助车间一体化控制的DCS系统,具有里程碑的意义。
2008年,国电智深又先后和国华徐州电厂、国电谏壁电厂签订了1000MW超超临界机组DCS系统供货合同,庄河项目的成功为自主化EDPF-NT系统下一步在1000MW超超临界机组的应用打下了坚实的基础。
——转自《自动化博览》
|