高峰 (1966-)
男,浙江建德人,工程师,学士学位,研究方向为自动化,现就职于杭州格林香料化学有限公司。
摘 要:本文以和利时公司HOLLiAS_MACS_DCS系统在精细化工间歇式批量生产项目中的成功应用为背景,介绍了作者如何应用HOLLiAS MACS DCS系统的硬件平台和组态工具,开发出了一套适用于在精细化工设备上进行间歇式批量控制的软件。生产实际应用表明:此套批量控制软件投运后,软件功能满足间歇式批量生产过程的控制要求。
关键词:精细化工;间歇式批量控制;HOLLiAS_MACS_DCS;组态工具;编程语言
Abstract: It is hard to control the Batch Sequence Control Fine Chemicals Procedure in the Fine Chemistry Industry.If adopting single process control model or special control devices used in some process steps, it would be not good to the whole project’s concentrating manage and optimizing control. Hollias_Macs_DCS control system is applied here, which can concentrate manage and optimize control of the whole process line.The application shows that Hollias_Macs_DCS control system can realize Batch Sequence Control in Fine chemical reactor easily and simply, reduce working intensity of the operators, and improve the production efficiency.
Key words: Fine Chemicals Producing; Batch Sequence Control; Hollias_Macs_DCS; Building Tools;Programming Language
1 引言
精细化工因为工艺的特殊要求,经常需要进行间歇式生产,由于其工艺过程复杂、繁琐、原料品种多、而且过程控制参数也千差万别,因此在实际生产中对DCS系统要求非常高,特别是为了方便操作人员的操作和控制,必须使用批量控制软件。由于成熟的商品化批量控制软件包只有国外几家著名的DCS厂家才有,如霍尼韦尔、横河、EMERSON、FOXBORO、ABB等公司,并且都遵循国际上ISA S88批量控制标准。而国内DCS厂家由于起步较晚,几乎都没有批量软件包,间歇式批量控制一直是国内DCS厂家不敢涉及的方面。因此,在国产DCS系统上成功地开发出一套符合精细化工间歇式控制特点的批量控制软件包就变得非常重要。
和利时公司的HOLLiAS_MACS集散控制系统是基于开放的现场总线Profibus DP标准的第四代DCS系统,可以无逢连接PA仪表、带DP通讯口的称重仪表及变频器,大大提高了精细化工行业的测控精度;而控制器具备多控制周期(100ms、250ms、500ms、1s等)功能,可以按精细化工工艺要求设置多种任务,以有效地满足批量控制过程中不同装置或控制的需要;功能完全分散的全数字化系统,应用于精细化工的生产上就可以充分发挥它在控制精度、实时、高效;系统安全、稳定、可靠各方面上所具有的强大优势;HOLLiAS MACS系统也提供在线无扰增量下装功能和离线仿真调试环境,仿真调试可以在仿真模式下程序可脱离控制器单独运行模拟现场运行情况,用户可以在非现场环境中就能对程序代码进行调试,检查其是否满足要求,减少实际生产时的修改量,保证系统稳定运行。因为有了和利时公司的HOLLiAS_MACS_DCS强大的系统平台作保证、特别是在线无扰增量下装和离线仿真调试功能,才能保证作者能成功地开发出符合精细化工间歇式控制特点的批量控制软件包。
2 控制特点
2.1 品种的多样性
在同一个设备里,可以选择不同的批量配方,通过选择不同的批量配方来改变生产过程中的控制参数值和控制步骤,来改变其生产特性,以达到生产不同产品的目地。
2.2 不同的反应时间和反应条件,所选择的批量配方不同
批量配方管理数据库中有不同的反应时间和反应条件,从而使生产设备根据选择的条件进行生产,达到生产不同品种的目的。
2.3 生产过程操作劳动强度大和复杂性强
操作劳动强度和复杂性都较大的一个生产过程,从配料到结束,其时间有时达24小时左右;如果完全靠现场操作,则操作人员的劳动强度非常大,操作也太复杂,容易造成操作失误等;如果在DCS界面手动操作,则操作人员忙于进行画面切换、操作设备的切换,容易产生疲劳后导致操作失误或失控,甚至于造成严重的生产安全事故。
由于精细化工生产装置中存在的这些特殊性和危险性,对DCS自动控制系统的性能和要求提出了更高的标准;如何实现整个车间设备全自动生产:包括复杂多批量配方管理、温度和压力的精确控制等全自动的实现,对国产DCS系统的可靠性、灵活性、软件编程语言、具体如何实施等方面是一个严峻的考验,也是一次质的提升。
本文通过使用和利时公司HOLLiAS_MACS集散控制系统多年的经验和对某精细化工生产工艺的反复深入研究,对整个生产过程进行了全面的分析和解剖,以工艺为轴线,进而提炼、把握其控制的关键点。使笔者最终设计与开发出了一套适用于在精细化工设备上进行间歇式批量控制的软件并对生产过程中的温度和压力进行平稳控制。
3 间歇式批量控制软件和控制方案的设计思路及在编程语言上的实现
3.1 间歇式批量控制软件设计思路
为了体现间歇式批量控制软件在单个生产装置上具有生产多品种产品的生产工艺特点和现场控制要求这一特性,通过HOLLIAS-MAC系统的人机界面软件(FacView)设计了一整套批量控制程序,将系统要求完成的配方名表单(包括品名、进料单体名称、进料量、相关控制参数)、工艺执行顺序表单和人机交互信息表单这三个表单文件保存为DBF数据库格式,操作人员可通过在画面上选择相应的配方名(品名),实现对数据库表单相应参数的显示、修改、下装等功能,达到自动实现批量控制的目地。
配方名表单,包括:品名、原料、工艺参数等相关数据的修改及其保存的方式;
配方名表单(品名)的修改、选择、操作:操作方式要简便,界面要友好,操作人员根据现场不同的实际生产情况,并在相应权限的许可下,可以进行各种参数的调整,满足生产控制对间歇式批量控制的要求;实时监视批量控制程序对品名的选择、工艺过程各参数的选择及其修改等;配方名表单操作人机界面如图1所示。
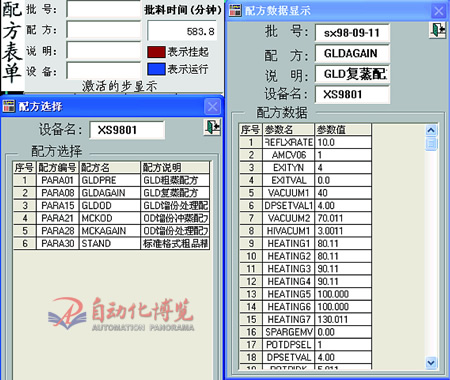
图1 配方名表单操作人机界面
配方名表单(品名)的存储方式:批量配方名表单的保存方式应该体现数据量大、链接性好、容易查找等特点。采用DBF数据库格式来保存数据,不仅能实现大量数据的保存,更能直观地记录各品名、工艺过程参数的数值;配方名表单(品名)的保存方式底层管理表单如图2所示。
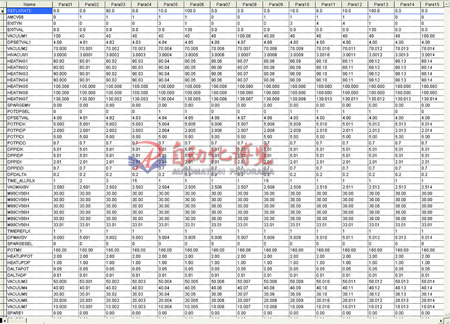
图2 配方名表单底层管理表单
工艺执行顺序表单(步),包括:根据具体的工艺步骤要求而排列的动作先后执行次序等相关数据的修改及其保存的方式;工艺执行顺序表单(步)的修改、选择、运行到下一步、挂起步、跳步、激活步和放弃步的操作:操作方式要简便,界面要友好,操作人员根据现场不同的实际生产情况,并在相应权限的许可下,可以进行各种步的调整,例如:自动运行到下一步、挂起步、向前跳步、向后跳步、激活步、放弃步等,以满足生产过程中灵活调整工艺流程的要求;工艺执行顺序表单操作人机界面如图3所示。
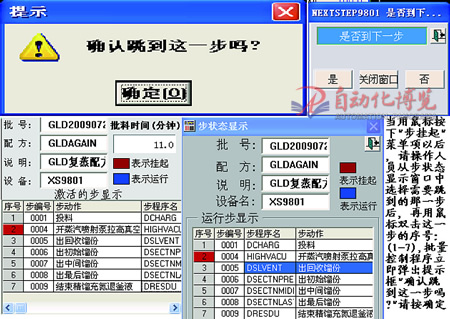 图3 工艺执行顺序表单人机操作界面
工艺执行顺序表单(步)的存储方式:人机交互信息表单(步)的保存方式应该体现数据量大、链接性好、容易查找等特点。采用DBF数据库格式来保存数据,不仅能实现大量数据的保存,更能直观地记录自动运行到下一步、挂起步、向前跳步、向后跳步、激活步、放弃步等步骤的执行情况;底层管理表单如图4所示。

图4 工艺执行顺序表单底层管理表单
人机交互信息表单,包括:具体动作执行时的相关信息的修改及其保存的方式;人机交互信息表单的具体动作执行时的操作:操作方式要简便,界面要友好,操作人员根据现场不同的实际生产情况,并在相应权限的许可下,可以根据人机界面的操作员当前提示信息进行操作,人机交互信息表单的人机操作界面如图5所示。

图5 人机交互信息表单人机操作界面
人机交互信息表单的存储方式:人机交互信息表单的保存方式应该体现数据量大、链接性好、容易查找等特点。采用DBF数据库格式来保存数据,不仅能实现大量数据的保存,更能直观地记录当前步骤的具体执行情况;底层管理表单如图6所示。
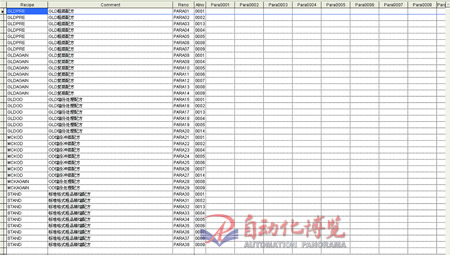
图6 人机交互信息表单底层管理表单
3.2 控制方案思路
精细化工间歇式批量生产项目的工艺特点决定了其控制方案的复杂性,贯穿整个生产过程的关键点是对温度和压力稳定度的要求,要尽量避免温度和压力的忽高忽低或出现短暂的失控现象。从工艺情况分析,分成三个阶段:①原料加完后开始程序升温、拉真空、随后再次加热升温使釜温升高、压力下降;②程序升温完毕后的滴加反应放热升温阶段、保压阶段;③滴加完毕后的保温阶段;这三个阶段的温度和压力稳定性控制的好坏,直接影响到产品的品质和产出率。下面我们分别从这三个阶段来讨论控制方案的异同点和对生产带来的效果。
3.2.1 程序升温控制
根据选择的配方名表单(品名)下装完成并加完原料后,紧接着就是程序升温、拉真空。在规定的时间内,把温度升至设定的温度点、并把压力降低到设定的真空值,为了防止出现超温或压力波动,设定温度的升温曲线和压力的下降曲线尤为重要,考虑到釜内存在惯性和滞后的问题,设定的曲线应该先快后慢,即先快速升温和拉真空降压一段时间,然后放慢速度升温和降压,直至温度和压力接近物料反应点的温度和真空度,这种平缓靠近反应温度和真空度的做法,使超温或压力波动等问题得以解决。为了防止因为反应点的变化,产生突然反应的情况,此时在釜的外盘管已经进行冷热水的切换,并通入了适当的冷却循环水防止超温。其升温曲线如图7所示。
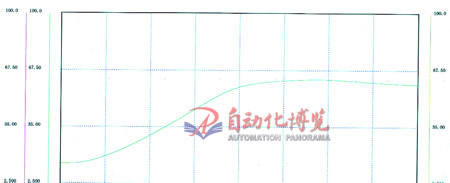
图7 程序升温控制曲线
3.2.2 滴加控制
当温度达到反应温度且釜内压力保持稳定时,判断反应是否发生的依据是:温度快速上升,且其斜率曲线较陡;具体则以连续的3个变化率数值来判断,即在连续5个周期(每个周期为0.5s)内取一个变化率值,我们连续观测3个变化率值,如果这个值大于一个定值(此定值由经验所得的最小值),则可以判断已经发生反应;接下来就是迅速把循环冷却水调节阀开至100%,再通过PID根据该品种配方名表单设定的温度值进行自动调节。根据管径大小及所设定的滴加完毕的时间进行初始滴加调节阀门开度的换算,即在开始滴加的时候其阀门的开度,这样物料的加入速度在开始就能控制得比较平稳,在此基础上进行滴加调节、控制,确保整个过程都能按照设定量滴加。滴加主要是控制计量槽内物料重量的下降速率与计算所得的下降速率,调节其阀门的大小,滴加的平稳性好(平稳匀速滴加),其釜内的温度控制也比较平稳,如果滴加出现大幅整荡,釜内的温度也难以控制,且不易稳定。其滴加曲线如图8所示。
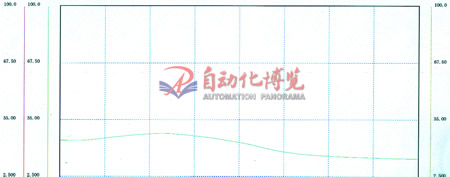
图8 滴加控制曲线
3.2.3 保温控制
滴加结束接下来进行保温控制,在设定的时间内保持温度的稳定,要求釜内温度与设定温度基本一致,其误差为±1℃,温度的设定值由配方数据表单一起管理,其值随着配方的不同而相互不一致。为了达到工艺的精确控制要求,我们采用了多参数动态监控的方案来实现温度的控制。
釜内温度具有滞后、积聚的特点,当温度出现上升或下降时,如果我们采用常规PID回路来调节,超调或迟缓往往经常发生,致使温度难于调节,无法满足工艺的要求。经过不断的实践摸索发现,当温度无论是正向偏离设定值还是负向偏离设定值,只要出现变化的趋势,调节阀必须马上跟着动作,调节冷却循环水的大小,以适应这种变化,防止温度随着正向偏离越来越多产生积聚效应,使反应急剧放量增快,越往后越难以控制,即使把冷却循环水控制阀开足100%也压制不住这种积聚反应,严重的将造成釜内物料溢出,甚至爆炸等;同时,如果温度负向偏离的时候,冷却循环水控制调节偏慢或调节幅度偏大,将使反应釜温度负向偏离越来越多,最后反应釜因为温度过低,达不到反应的温度,使反应变慢或停止反应,这样将造成产出量低,反应不完全,品质不能满足要求。
通过对工艺的分析和实际生产的情况来看,我们把釜内温度分为六个阶段:
·釜温度高于设定值+0.5,温度处在上升阶段;
·釜温度高于设定值+0.5,温度处在下降阶段;
·釜温度低于设定值-0.5,温度处在上升阶段;
·釜温度低于设定值-0.5,温度处在下降阶段;
·釜温度处在设定值的±0.5范围之内,温度处在上升阶段;
·釜温度处在设定值的±0.5范围之内,温度处在下降阶段。
在这个控制过程中,采用了釜内温度的变化率来控制冷却循环水的大小,以冷却循环水的温度作为参考指标,这样,只要反应釜温度产生正向或负向偏离,冷却循环水控制阀就开大或开小,开度变化的大小根据釜内温度的变化率、反应釜的实际温度、冷却循环水的温度三个参数量动态监测、运算,实现自动寻找对应的阀门开度值。这种动态模型的建立实现了反应釜温度控制稳定的第一步,紧接着在调试过程,摸索各种实际工况的参数,在生产过程中的总结各种经验值都是至关重要的,在笔者不断的总结和探索下,最终实现了温度的平稳控制,满足了生产的精确控制要求。如图9所示。
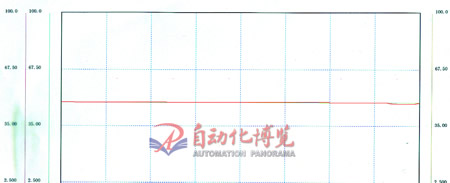
图9 釜内温度实际曲线
多参数动态监控模式的自动控制是否能够顺利投入运行,关键在于自动程序是否紧跟现场实际需要,是否很好地理解了其生产工艺特点;如果工艺控制条件的随意性大,将给编程增加很大的难度,也给经验参数的摸索带来一定的困难;经过现场两年的运行证明,其编程思路是可靠的,其控制方案是可行的;多参数动态监控模式的投入大大降低了操作工人的劳动强度,产品稳定性也得到了很大的提高。
3.3 控制方案的编程语言的实现
下位机控制器的编程采用符合IEC61131-3可编程控制器编程语言标准的ST、LD、FBD、SFC四种编程语言,通过自由组合方式混合编制实现,再通过编译、下装到现场控制站中的控制器中去执行,从而达到精细化工间歇式批量生产工艺所需要的控制要求。上位机的SCADA人机交互界面程序则根据操作员实际的操作需求采用类C语言编制而成,再编译成最终的二进制代码后和配方名表单、工艺执行顺序表单、人机交互信息表单等DBF数据库一起在Windows Server 2008 系统的配方服务器上运行。上下位机通过预先定义的全局变量实时地进行数据交换、传递和校验,保证上下位程序能够同步执行。下位机控制器编程语言环境的典型示例如图10所示。
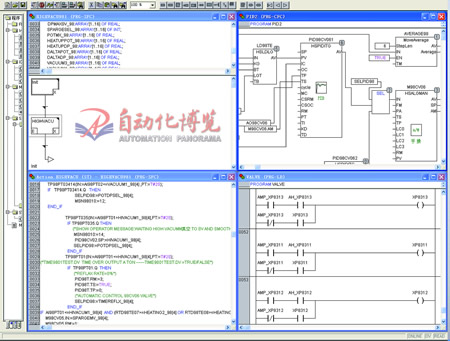
图10 下位机控制器编程语言环境
而上位机的SCADA人机交互界面程序的编程语言环境典型示例如图11所示。
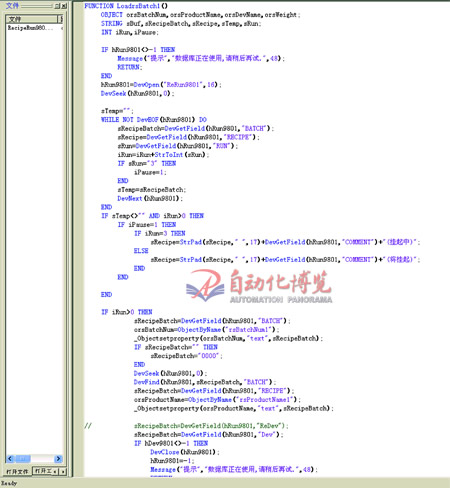
图11 上位机的SCADA人机交互界面程序的编程语言环境
4 结语
精细化工间歇式批量生产的全自动控制由于受工艺、设备、编程方式等多方面的因素制约,一直是自动控制系统的难点;国外大多数DCS厂家都是单独开发相应的批量控制软件包,并且单独计算费用;HOLLIAS-MAC_DCS系统在精细化工间歇式批量生产项目中的成功应用,利用其自身具有的灵活性和可靠性,达到了自动控制的要求,为企业节约了时间,避免了额外费用的开支;该项目的成功运行为其他间歇式生产提供了可行的编程思路,HOLLIAS-MAC_DCS系统为间歇生产工艺提供了可靠、灵活的硬件和编程软件。
参考文献:
[1] 王常力,廖道文. 集散控制系统设计与应用[M]. 北京: 清华大学出版社,1993.
[2] 王常力,罗安. 分布式控制系统(DCS)设计与应用实例[M]. 北京: 电子工业出版社,2004.
[3] 何衍庆,黎冰,黄海燕. 可编程控制器编程语言及应用[M]. 北京: 电子工业出版社,2006.
[4] ISA S88批量管理标准.
——转自《自动化博览》
|