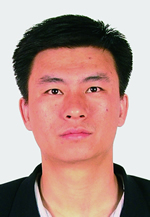
张冰(1975-)
男,宁夏中卫人,硕士研究生,工程师,研究方向为石化过程自动化,专业是控制理论与控制工程。
摘 要:氢氮比是合成氨装置最为关键的参数之一,保持比值始终处于最佳状态是提高合成氨产量的有效措施。中国石油宁夏石化公司化肥装置在实施该项目时,充分调研,针对目前国内氢氮比优化控制的三种主流方法进行比较。通过对其核心理论的分析,指明各种方案的优缺点,为生产实践奠定了理论基础。
关键词:氢氮比;优化控制;先进控制
Abstract: The H-N ratio in the production of synthetic ammonia is one of the most important parameters to increase the product yield which is an efficiency measure to keep the optimal production. In view of the present three main optimization control systems for H-N ration in domestic,we make an analysis and comparison, and point out the advantages and disadvantages for each strategy. By analyzing the core principles of each system, the production principle is confirmed.
Key words: H-N ratio; Optimization control; APC
1 问题的提出
在大型化肥装置中,氢氮比是合成氨装置最为关键的参数之一,保持其始终处于最佳状态是提高合成氨产量和降低消耗的有效措施。
氨合成反应方程式为:N2+3H2=2NH3+Q
特点是反应放热,体积缩小,反应可逆,有触媒,高温高压。
从氨合成催化剂的活性角度分析进塔气最适宜的氢氮比在2.5左右,而从平衡角度则以3为最高,所以氢氮比在2.5~3范围内最有利于氨的合成,正常的最佳氢氮比为2.7~2.8。低于2.5或大于3.5会使合成塔床层温度下降,若持续时间较长,可能导致床层温度跨掉,合成塔封塔。
目前我国大型合成氨装置的氢氮比控制系统大都由DCS实现,由于DCS控制系统的基本单元未能脱离常规PID控制算法,因此在波动较大、干扰较强、大时滞的情况下,PID参数不适应此状况,常规PID控制算法又不能实现参数自整定,故不能及时将工况控制在最佳状态,有时反而造成系统波动,操作工不得不及时将回路切到手动,导致现氢氮比控制系统投用率极低。而手动调节1次要10~40分钟左右的时间才能反映出调节效果,几个周期下来,就会使系统长时间处于非优化控制状态,以致于影响了系统的稳定和产量。
宁夏石化公司针对45万吨大型合成氨装置依靠人工调节和在工况出现波动的情况下装置现存的大时滞情况,实施合成氨装置氢氮比优化控制策略,研究出一套反应灵敏、调节及时、保证工况调整尽快处于优化状态的自动控制方案。
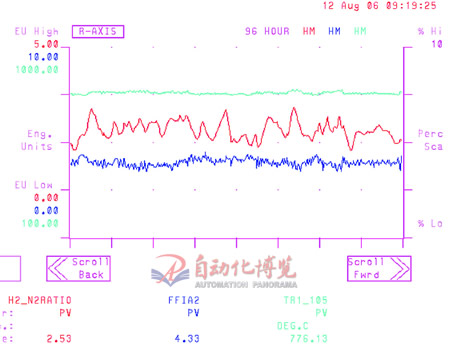
图1 目前宁夏石化公司合成氨装置三大控制参数历史趋势
目前氢氮比优化控制属于传统优化控制方法和先进控制方法都可以涵盖的范畴,在我国大化肥行业,目前实施较成功的装置主要有表1中的三家。由于三种技术方案的设计思路不同,各有特点,差别如表演所示。
表1
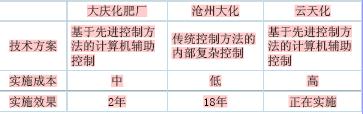
沧州大化是基于传统控制方法的内部复杂控制,通常被称之为一次优化;云天化是基于先进控制方法的计算机辅助控制,由HONEYWELL国外专业先进控制软件开发公司实施的,通常被称为二次优化,或先进控制,氢氮比控制只是它系统控制中的一个部分;大庆化肥厂采用基于先进控制方法的计算机辅助控制,针对单回路设计,结合传统优化控制的前馈算法,由大庆华创公司实施。从技术先进性考虑无疑先进控制的技术含量和先进性无庸质疑,企业最看重的是实际效果,哪种方案实施可靠性高,成本低。优化控制和先进控制在某些方面是不能互相取代的,二者是相辅相成的关系。以下仅从理论角度对两种方向进行探讨,为今后提高大化肥行业自动化控制水平提供参考。
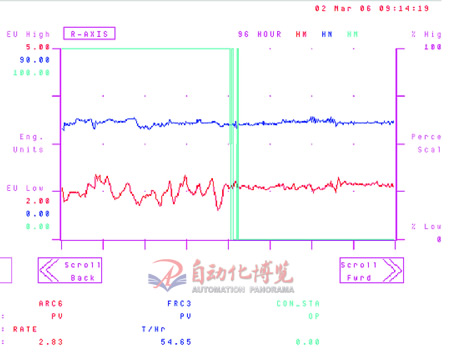
图2 大庆化肥厂氢氮比投用前后历史趋势
2 两种优化控制方案的核心技术比较
2.1 基于先进控制方法的计算机辅助控制
先进过程控制是基于现代控制理论在过程控制领域的应用,先进过程控制(APC,主要是模型预估控制MPC),其特点是:
· 实现较复杂
· 基于过程数学模型
· 适于大滞后多变量
· 适用于常规控制无法满足要求的复杂对象
模型预估控制(MPC)——基本原理
(1)模型预估
在建立生产过程数学模型的基础上,通过数学模型利用过程的过去和现在的输入输出信息可以估计出过程未来某段时间的运行状态,从而得到未来运行状况与期望目标的误差,用以指导和计算当前的控制作用就会得到比常规控制更好的控制性能和效果。因为常规控制是用实际误差来计算当前的控制作用,而预估控制是用未来预测的误差计算当前的控制作用。
(2)反馈修正
过程模型一般是经过多种假设简化和/或辨识估计参数得出的,它不可能完全准确,同时由于过程的非线性、时变和随机干扰等各种因素的影响,因此由模型做出的估计一定是存在偏差的。为了减小这种偏差对控制系统的影响,要将当前的输出与当前时刻的模型估计的偏差加到未来运动的预估结果上,从而实现对未来的预估值的反馈修正。正是由于反馈修正的存在,从而增加了控制系统的稳定性,一定程度地消除了建模误差,降低了对模型精度的要求,并且对不可侧干扰起到了抑制作用,最终使控制系统的鲁棒性得到提高。
(3)滚动优化
预估控制结合了优化控制策略。预估控制算法通过使某种控制指标达到最小而得到最优控制作用,且所得最优控制作用只实际执行当前第一步。随着时间的推移,每一采样时刻都会重新计算其最优控制作用,因此随着控制系统的运行优化控制是滚动进行的,也可以说是实时优化控制。
大庆石化公司化肥厂的合成氨装置氢氮比控制采用的广义预测控制方法核心是如下公式:
(1)
模型采用阶跃响应和脉冲响应作为预测模型,可以理解为已知以前时刻的输入与输出的对应关系,那么可以根据这个关系方程根据现在的输入推出将来的输出。 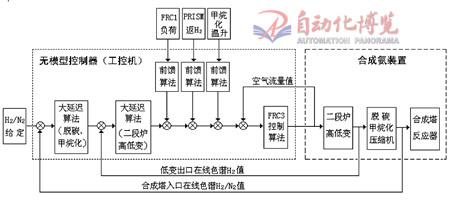
图3 大庆化肥厂氢氮比控制结构图
2.2 基于传统控制方法的内部复杂控制
常规过程控制(PID)的方法较成熟,特点是
· 实现简单
· 无模型
· 单回路
· 不能适应大滞后多变量系统
· 对要求较高的、复杂的过程不易有好的控制效果和性能
沧州大化的技术方案是使用传统的基于复杂控制回路的设计思想,利用DCS内部现有的功能块,搭出一个优化控制回路,这种方案工厂技术人员较容易理解,实施有把握,技术难点在各控制器之间的参数设计和系统各串级回路的参数设置。针对宁夏石化45万吨合成氨装置的设计控制结构图如图4、图5所示。
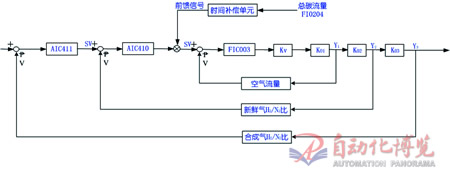 图4 H2/N2比控制系统方块图
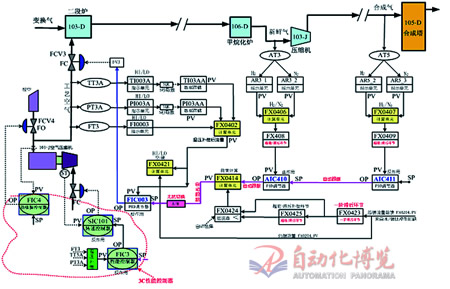 图5 氢氮比控制系统
沧州大化H2/N2控制系统是一套具有较强的自适应能力、抗干扰能力和克服大时滞现象的“前馈-比值-多串级”调节系统。本系统是以合成塔入口循环气H2/N2为主调(AIC411),以进入合成系统新鲜空气H2/N2为第一级副调(AIC410),以加入二段转化炉的空气流量调节器FIC003,以总碳流量FX0204 PV为前馈信号的“多串级-前馈-比值”控制系统。该控制系统共采用各种功能的DCS内部仪表20多块。该系统对进入二段炉103-D的工艺空气流量进行控制,以此来调节新鲜气H2/N2和合成气H2/N2 。
合成气H2/N2作主调AIC411;新鲜H2/N2作第一级副调AIC410;主调AIC411的输出作第一级副调AIC410的外给定(SP);第一级辐调AIC410的输出与总碳流量在FX0414进行前馈运算,得出所需的空气流量值,作副调FIC003的外给定,由空气流量调节器FIC003调节阀门FCV3,FIC003的输出控制进入二段炉的空气流量,达到最终控制合成气H2/N2的目的。
该系统对一次仪表均要设置正常工艺操作上下限报警值(HI、LO)、变化率报警值VL、输入断线报警值IOP,对PID调节器均要设置偏差报警值DV,目的是对一次仪表和主要调节器的故障和错误信息进行判断、识别,采取相应的安全保护措施,如输入开路、测量变化率大、输入信号越限、偏差报警等现象发生时,调节系统自动切除串级或自动状态,并报警提醒操作人员。
3 结论
综上所述,优化控制与先进控制完成的目标是一致的,但先进控制较优化控制层次高,它是借助于目前计算机的飞速发展,通过计算机高速的计算能力,利用现代控制理论,用数学模型模拟出装置的特点,预测出整个装置各个参数的关联变化,统一协调的优化整个系统,但对DCS的单回路控制水平要求极高,单回路应该调节灵敏准确,都投在自动状态,装置运行在高负荷状态,通过传统的控制手段已无法提高生产能力,节能降耗,所以借助于先进控制。比较而言,我们研发的优化控制更适合目前国内装置的运行水平,适合负荷大范围的波动,能够协调控制几个关键参数,实施成本较低,并且为最终实施先进控制打下基础。
——转自《自动化博览》
|