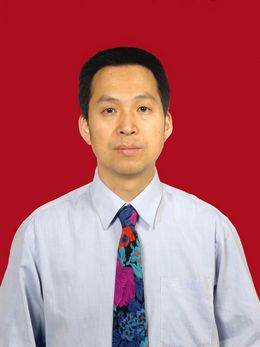
作者简介: 孙旨义(1965-), 男,河北正定人,高级工程师,1986年毕业于河北工业大学精密仪器专业,长期从事医药行业基础自动化、控制系统、先进控制系统应用、工厂综合自动化集成、BATCH柔性化生产管理系统应用等工作,现任华北制药集团倍达有限公司计控能源室主任。主持倍达有限公司ERP 应用开发、MES系统的应用与开发等河北省重点信息化建设项目。先后获得省部级科学技术进步二、三等奖多项,市集团级科学技术进步一、二、三等奖18项之多,并获得省新世纪“三三三人才工程”人选。
摘要:本文论述了制药行业如何借助自动化信息技术高速发展的契机,实现自身的跨越式发展。
关键词:自动化信息技术;先进控制技术;制药行业;柔性制造系统;MES;ERP;LIMS;质量管理系统
据统计数据显示,1978年,我国医药工业总产值只有72.8亿元,到2008年,我国医药工业累计实现总产值8666.82亿元,相当于1978年的123倍,2009年我国医药工业总产值有望超过1万亿元,实现利润总额有望超过1000亿元。一系列市场研究也表明,今后5年中国制药行业将以年均9%~10%的速度增长, IMS曾预测,2011年,中国将成为世界第五大药品市场,2020年,中国医药产业将仅次于美国居世界第二位。
我国制药企业虽然发展很快,但与发达国家还有相当大的差距,全球医药企业的前50强,全部集中在美国、日本和欧盟,我们的制药企业与发达国家制药企业相比,除了产品结构等其他因素外,一个重要的方面是自动化信息技术装备的落后,大量的人力作坊式生产模式,很难通过欧美发达国家的质量认证,进入国际主流医药市场。据有关资料统计,自动化信息技术装备投资比例占总投资的比例为:
西方发达国家约40%~50%左右;
国内的独资制药企业约30~40%左右;
国内合资制药企业约10%~20%左右;
国营大型制药企业开发区新建子公司约5%~10%左右;
国营大型制药企业旧生产线只有约3%左右;
从以上数据可以看出投资比例的差距,由此更可分析出自动化信息装备技术应用水平的差距。
制药行业发展到今天,日益注重生产的高效以及成本的节约,而自动化信息技术的应用当之无愧成为提高生产效率和优化管理的最强有力的手段,很多业界的成功案例也使我们深刻感受到自动化信息技术为制药业所带来的巨大变化,从某种意义上说,自动化信息技术应用程度的高低决定了一个药厂的竞争力和发展空间,制药行业着眼于过程控制和自动控制仍将是企业取得成功的关键。
世界20个顶尖的制药公司及一流生物技术公司,包括辉瑞公司、拜耳保健公司、诺华公司、默克公司、美国健赞公司等都在规划数字化工厂模型,实施MES(生产执行管理系统)及BATCH柔性化多品种生产管理系统,其中有些公司已经决定在其全球生产网络中采用该解决方案。
胡锦涛总书记在党的十七大报告中提出了“全面认识工业化、信息化、城镇化、市场化、国际化深入发展的新形势新任务”的战略思考和“大力推进信息化和工业化融合”的战略口号,“五化并举,两化融合”的新战略思想,是对信息化、工业化本身及其关系认识的深化,深刻地揭示了信息化和工业化相互促进、相互依存和融合发展的特点,将信息化的历史地位推到了一个新高度。我国的制药企业,要想踏上自动化信息技术高速发展的列车,挤身世界强企之林,必须加快以下几个方面的战略规划和建设。
1 加大基础自动化投资力度,广泛应用先进控制技术
加速企业的生产过程自动化基础建设步伐,使得生产过程的现场控制更加有序、高效,处理非常事件更加快捷、安全,提高工厂现场控制与监视的自动化水平。根据公司的生产过程关键工艺点的实际需要,重点进行专家控制、预测函数控制、多变量预测控制等先进控制算法的应用,解决常规控制不能解决的复杂控制问题。先进控制技术的应用是实现工艺优化和工厂综合自动化的基础。
比如:在合成制药生产工艺过程中,生产过程复杂,工艺较长,由于控制点较多,每步操作都需要有人工干预控制,同时,又包含一些复杂的控制对象如PH值控制等。PH值控制的好坏直接影响产品的质量指标如收率、产品晶型等。pH过程本身具有严重的非线性;在中和点的附近具有较高的灵敏度;难于建立准确的数学模型;环境(如温度、压力等)的变化以及其他干扰的存在都会改变pH过程特性;一般要求pH值跟踪一条预定的时变曲线。pH控制系统所涉及的生产装置多、需要控制的工艺参数多,同时存在的耦合性强、非线性严重。为此,人工操作的劳动强度大、人为影响生产的因素多,导致生产产量不稳定、质量不稳定,所有这一些表明常规的、采用固定结构、单一的控制器或采用变参数的PID控制,都难以达到工艺要求,不能满足生产过程控制的要求。因此对合成工艺生产中的PH值,采用先进算法和模态识别技术进行pH控制系统的先进控制,完成pH过程的自动化,具有十分重要的战略意义。
2 在制药生产线大力推广BATCH柔性化多品种生产管控系统,是快速适应市场多变的强有力的保证
BATCH系统是符合ISA S88国际标准的,用户管理和电子签名的组件是遵循联邦法规第21章11节(CFR 21 PART 11)的相关规定的,整个系统可以实现多品种的配方管理、配方验证、配方发布,生产计划的管理、验证、发布、实施,电子签名 (Digital Signature)、用户授权管理,一直到整个生产线符合FDA要求的批生产过程的管理与控制,并自动产生具有审计追踪(Audit Trail)功能的生产批报表管理系统,实现柔性化高效率的多品种生产。具有以下特点:
(1)机动灵活的引导式操作界面
·交互式操作过程,运行生产中的所有细节,相互交错地促进操作人员和设备之间的最佳操作。
·应用交互式过程引导方式,可以设计出一个通用的适用多种产品的生产程序,并定义生产过程变化。
(2)通览、控制、追踪生产过程每一细节的能力
·整个生产过程的每一步细节,生产操作人员与设备之间的运行,通过交互式人机对话的方式完成。保证生产过程的每一步执行情况与标准操作程序保持一致。
·跟踪及考核:权威性的批记录,提供一个具有可追踪性,并可分析的基本应用报告,量化了生产中的操作情况, 能够追踪到每一步操作,完全体现了GMP/FDA管理理念。
(3)快速多变的市场需求
·实现多品种的配方管理、配方验证、配方发布功能,通过科学的生产计划的管理,实现柔性化高效率的多品种生产。
BATCH批控制管理系统,其主要解决在一条以批操作为主,多配方(工艺)、生产不同产品生产线上如何进行订单管理、配方管理、批报管理等问题以及如何与过程控制系统相联共同控制整个的生产过程,使整个的生产完全按照既定配方进行,减少产品差异率,提高生产效益,以及确保生产线符合GMP等相关法规规定。
3 应用质量控制管理系统,是保证产品质量的重要手段
对在现代化的生产和制造过程中的质量部门,完善的质量控制当然是他们的首要任务,同时在此基础上,实现成本最小化,而且遵从相关的规则(比如GLP、GAMP、ISO、FDA等)的要求。质量控制管理系统是建立在ISA-95质量管理的模型基础之上,集成了多年来在各行业的经验,高效地利用生产或实验质量数据来保证产品质量,提高产品一致性,以有效达到成本控制的目的。
质量控制实验室主要涉及产品质量,因此与制造流程有着紧密的联系。从原材料的验收到生产的不同阶段,一直到成品装运给客户,都要对产品的质量和变化进行监控并做出有效报告,以便确定何时有必要采取过程控制措施,并确认所采取的措施是有效的。沿着生产流程,质量控制实验室还经常涉及环保测试、特殊的质量项目测试等。允许用户根据产品类型(原材料、在制品、产成品)、供应商或客户将产品分为若干组。对于每组产品或每个特定产品,应用管理人员可以确定需要进行哪些分析、分析的频率如何以及每种分析适用哪些技术规格。一旦样品已登录,就可以输入采样位置、采样时间、某个批号等特定信息。对于每个样品,可以使用不同的分析方法来确定分析参数。相互有关的分析(如化学分析或微生物学分析)将被合为一组。在自动计算最终结果之前,可以定义一系列的执行步骤作为分析的方法。一旦知道了分析结果,就将它与技术规格对照检查。如果结果数值超出了技术规格,质量控制部门经理可以做出几种决定:请求附加分析或再次分析、拒绝产品等。而对于在技术规格范围内的分析结果将会自动得到验证,从而节省了大量时间。一旦知道某个特定样品的所有参数结果,就可以生成证书或批准报告。报告也可以根据其他选择标准来生成客户化的报告,比如根据产品类型、供应商等。
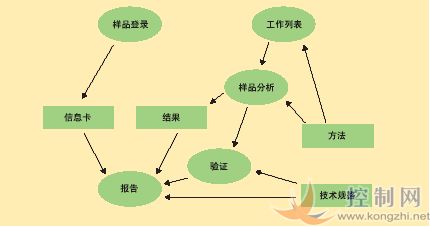
图1 质量控制管理系统执行步骤
(1)可配置的实验室对象模型
独特的面向对象的实验室模型使得这些配置好的对象可以不断重复使用。这会大大降低在LIMS配置时所付出的劳动,并提供了最大的灵活性。
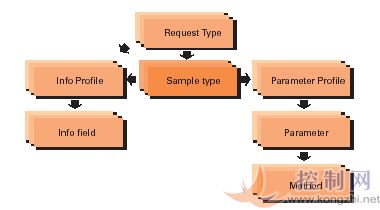
图2 面向对象的实验室模型
(2)利用LIMS改善实验室的运作
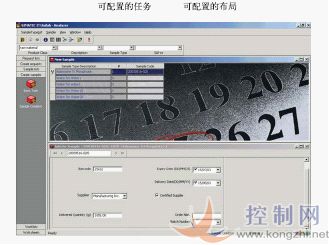
图3 改善实验室运作界面图
(3)趋势分析和统计质量控制(SQC)
由于全面质量管理需要进行统计质量控制,LIMS必须连续更新统计图表,才能对趋势进行度量。分析人员或实验室管理人员可以使用在线趋势分析或在线统计质量控制(SQC)来帮助做出质量决策。支持的SQC规则包括Western Electric Rules(西方电气规则),例如,x±3sigma的n次逐次值;n次逐点提升、上升趋势等,而且用户还可以进一步配置和自定义规则。

图4 在线趋势分析
(4)质量报告
所有数据都被存储在一个关系型数据库中。数据库的开放式结构允许您方便的使用任何外部报告软件。而且还提供了一个嵌入式报告引擎:“报告”。这是一种基于商业对象的完全集成的查询、报告和数据分析工具。报告具有一个完整的图形用户界面。它通过二层(客户机/服务器)和三层结构(Web) ,确保了对数据的快速和有效的检索和处理。
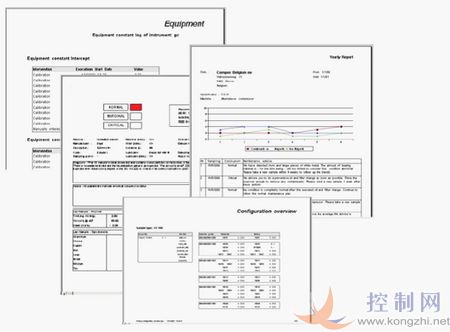
图5 质量报告
4 规划实施生产执行系统(MES),是实现生产过程管理创新的技术手段
这种结构结合了先进的工艺制造技术、现代管理技术和以先进控制为代表的信息技术,集成了企业的经营管理、生产过程的控制、运行与管理等各个方面,将其作为一个整体进行控制与管理,实现企业的优化运行、优化控制与优化管理,从而成为提高企业竞争力的重要技术手段。
制造执行系统MES(Manufacturing Execution System) 是一个立足于整个企业生产活动的计算机系统。利用MES的管理手段和信息,企业可优化其从制定生产产量到管理最终产品的整个生产流程中的各个环节。利用实时、准确的数据,MES指导、管理、记录企业各项生产活动,为企业提供及时准确的信息,使企业及时根据外界环境的变化调整生产。其结果是企业的无效益生产活动减少,企业生产效益提高、生产设备利用率提高、产品质量提高、库存降低、供货周期缩短,最终使得企业的盈利水平得以提高。
4.1建立模型
在建模阶段,主要的任务是了解应用范围和要求;工厂的结构如何;工厂中有些什么样的不同对象;这些对象完成什么任务;对象在结构方面是否进行了分组等。一种常用的方式是,从工厂中的物理和逻辑对象开始进行建模,然后用生产作业定义这些对象之间的相互关系。
4.2 物理工厂
在建模阶段,从基本对象开始建造一个物理工厂模型,这样的对象被称作“单位(unit)”。典型的单位,包括搅拌器、加热炉、熔化机、消毒箱等。当所有单位都进行建模后,它们可以组合成“单元(cell)”。一个单元可以包括一个或多个单位,并且它可以包含相同类型的单位,也可以包含不同类型的单位。不同的单元可以组合成区域(area),而区域可以组合成地点(site)。用户在用于工厂对象及其分组的术语与MES国际标准IEC62264-1(也被称作ISA-95第一部分)中所定义的术语是一致的。
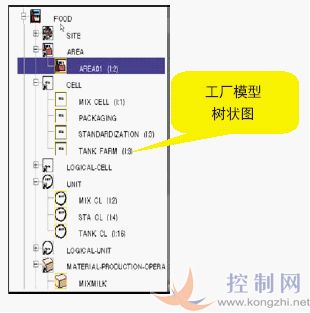
图6 建造物理工厂模型
这意味着物理工厂的模型具有一种分层结构,分别由单位(Unit)、单元(Cell)、区域(Area)和地点(Site)组成,如图6所示。
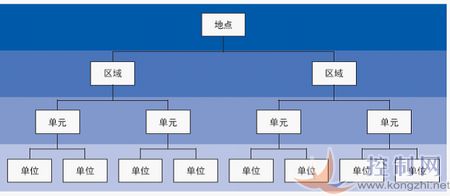
图7 建物理工厂模型的分层结构
物理工厂的建模可以用一种从下往上(如此处所述)的方式进行,也可以从上往下进行。在对物理工厂进行建模时,不必将注意力放在物理对象所具有的功能和/或性能上,也无须进入任何实施细节,这些都是在后面一阶段要完成的任务。
通过开发模式,可以很容易地对物理工厂进行建模。通常情况下,所需要的对象已经在系统中预先定义,而且显示在建模的屏幕上,这样就可以简单地通过点击面板上的对象并拖放到设计面板上,从而快速实现工厂模型化。如果某个所需对象没有作为一种预先定义的对象存在,则可以快速地创建或者从现有对象中推导出来。一旦已经定义,则它就出现在面板上,以后就可以重复使用这个对象单元。
4.3 生产执行
当建模和工程与系统建置阶段完成后,项目就可以开始执行了。不仅是一种强有力的工程环境,同时,利用它,还可以执行生产作业并实时监控它们的状态。由于执行过程是用颜色区分的,所以执行环境可以很方便地跟踪。如果某生产作业或生产作业的一部分为绿色,则表示它已经成功执行,红色意味着发生了错误,褐色意味着生产作业或生产作业的一部分处于暂停状态,而黄色意味着当前正在执行。图8就是一个实例。
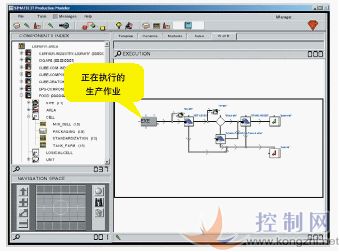
图8生产执行界面图
SIMA可以配置成对已经执行过的生产作业进行归档。如果需要进行分析的话,这样做就很有意义,并且,如果在执行过程中发生了任何故障的话,就可以对故障查找和排除进行深入的分析。生产作业的每一步都会按照执行情况用颜色标记。输入和输出参数也可以显示出来,以便简化故障排除作业。通过矩阵,还可以检索执行状态的直观视图,如图9所示。该矩阵在第一栏中显示已经开始的生产作业列表,在最上面一行中显示不同的工厂对象。该矩阵可以以不同的详细程度观察,例如:可以查看区域级的生产作业在相关单元中的执行情况,或者查看单元级的生产作业是如何通过相关单位执行的。
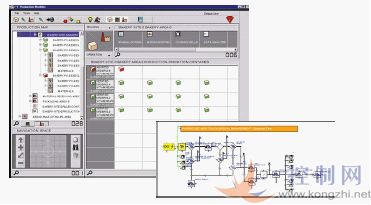
图9 执行状态的直观视图
例如:在物料验收区域中,对若干生产作业创建了模型。图10显示了其中一个生产作业是如何执行的。

图10 生产作业执行示意图
SIMA如果执行过程中发生了某种错误,那麽相应的步骤就会以红色标记,图11就显示了这种情形。
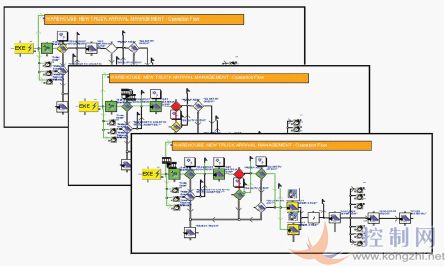
图11 生产作业执行中出现错误示意图
各个方法和事件的参数和自变量也可以显示,以便进行深入分析。
5 应用ERP(企业资源计划)系统,实现企业业务流程的优化
ERP(企业资源规划)系统围绕着三大流——物流、资金流、信息流,对公司核心业务流程进行优化,去掉不增值环节,严格规范流程中和节点的操作规范,建立符合公司业务需求和现代化管理要求的高效的业务流程。进行业务流程重组,对公司核心业务流程进行优化。
(1)物流系统
·建立公司内部的物料配送体系。
·建立公司对外部客户、供应商的原材料及产成品等物料的配送体系。
(2)资金流系统
·建立完善的应收、应付账款的监控系统。
·建立合理的成本管理及考核系统。
·建立公司全面的预算管理系统。
(3)信息流系统
·建立与生产过程控制系统紧密联系的数据采集系统。
·建立规范的报表数据处理流程。
·建立公司内、外部客户关系管理系统。
参考文献:
[1]孙旨义.MES在制药行业的应用研究[J]. 石油化工自动化. 2004,(5).
[2]孙旨义.制药行业自动化信息技术最新应用及展望[J].自动化博览.2008,(10).
|