内容 |
马竹梧 (1931-)
男,广州市人,教授级高级工程师,原冶金部自动化研究院副院长、总工程师,现中国钢铁协会信息化自动化推进中心顾问、中国自动化学会专家咨询委员会委员,主要从事工业自动化研究和设计工作
摘要:本文主要叙述炼钢过程检测夹渣的必要性,目前国内外检测夹渣的方法,包括电磁感应法和红外热成象法。根据这些方法存在问题及生产实际而开发一种采用测温仪表的低成本方案。此外,还进行仪表选择和在首钢进行试验并取得初步成功以及指出今后方向。
关键词:电磁感应;热成象;温度
Abstract: In this paper, we mainly describe the necessity of slag detection during steelmaking process and the slag detection methods including magnetic inductance or thermal imaging methods. According to the existing problems of these methods and practices in production, we develop a lowcost plan using measurement temperature instrument. In addition, we discuss the choice of instrument , get preliminary success in the test done in Shougang and then point out the future work.
Key words: Magnetic inductance; Thermal imaging; Temperature
1 引言
1.1 炼钢过程下渣检测的作用
在转炉或电弧炉炼钢过程中,为了除去铁水的其他杂质,如硅、磷、硫等,需要进行吹氧和添加一些副原料进行冶炼,生成钢水及钢渣。钢水较重,在炉中沉于底部,钢渣大多数为非金属氧化物,浮在钢水上面。当冶炼结束开始出钢时,钢水从出钢口中流到钢包中,钢水和钢渣在炉中液位逐渐下降。当钢水快要流尽时,钢渣逐渐流出,这时,钢水和钢渣呈混合体(夹渣)。由于钢渣影响钢水质量,此外,若夹杂物过多,钢水不洁净,易于堵塞出钢口和使钢包的耐火层磨损严重。因此,必须测出钢水下渣情况,以便及时挡渣或停止出钢。此外,在连铸过程中,在中间包浇铸末期,流出钢水会出现夹渣,如果进入结晶器会影响铸坯质量,进而影响轧钢后钢材质量而前功尽弃,而更迫切需要及时检测并阻止夹渣钢水进入结晶器。
1.2 炼钢过程下渣检测的效益
目前,国内大多数炼钢厂在出钢过程中, 出钢结束时间仍是由操作工根据钢水和炉渣的颜色进行判断和操纵的, 这需要操作人员具有一定的工作经验, 因此具有很大的主观性。而且炉渣刚在出钢口出现时很难由视觉判断出来, 即便对于有经验的操作工来说, 当钢流夹渣量为15%~20%时才有可能发现, 小于此值时就无法分辨夹渣现象, 再加上现场环境很恶劣, 影响操作人员的判断, 因此造成大量炉渣夹带的问题。从而不但影响产量, 而且影响钢的质量。实践证明若采用自动炉渣检测装置则可解决上述问题,而且可以获得很大的经济效益,据奥钢联统计,有效地出钢和探渣系统可以保证以下几点:① 下渣量最少;② 脱氧剂和合金用量减少;③ 回磷减少;④ 钢包耐材寿命延长;⑤ 改善钢水脱硫;⑥ 钢水成分更准确。其投资在几个月就可收回。日本NKK公司福山厂转炉采用了由德国AMEPA公司生产的TSD热成象炉渣检测系统后, 流入钢包的转炉渣量约减少了40%;本系统使用前, 钢包中炉渣的平均厚度为27.6mm, 标准偏差为11.4mm; 使用后渣的平均厚度为16.2mm, 标准偏差为7.6mm;使用本系统前, 高温出钢时有检验延迟的现象, 使用后则没有这种现象发生。国内宝钢300t转炉使用引进的AMEPA TSD热成象系统监视下渣情况也获如下的良好效果:① 使用TSD系统,脱碳阶段后下渣检测成功率是99.3 %,脱磷阶段后为88.7 %;② TSD系统效果与操作工目测经验判断的比较为平均响应时间短和标准偏差明显下降,即脱磷阶段后的平均响应时间从目测的4.8 s减少至TSD的3.3s,脱碳阶段后则从3.9 s 减少至2.3 s;③ 脱磷阶段后出钢时, 钢包平均渣厚从86.89mm减小到68.50mm,标准偏差大体相当;④ 熔剂消耗减少了12 %~21 %;⑤ 转炉脱氧Al 加入量约减少了19 %。因此装设下渣检测系统是迫不容缓了。
2 炼钢过程下渣检测研究的目标
开发目标包括:① 有效(准确的、易于安装的和可维护性好的等)的和功能齐全(有大小指示、报警、自动控制和能与计算机连接的和可多种选择等)的钢水夹渣检测系统;② 低成本的和便于推广的;③ 应用面覆盖广的,要不但适合转炉、电弧炉、感应炉等出钢过程及连铸过程而且要适合于重要铸钢如铸造轧辊过程等;④ 最好采用和考虑能覆盖或改头换面就可用于其它用途而不是单打一的技术和方案,如日本东芝的测长仪表改头换面就可成为测速仪或延伸率检测仪等,又如德国生产钢板测厚仪表改头换面就可成为测量横向厚度、板形等仪。这点很重要,因为这样易于形成批量、改善质量和降低成本,而在激烈的市场竞争中取胜,特别是钢铁专用仪表,难度大、批量少和成本高等,这是过去开发国内开发钢铁专用往往昙花一现的原因;⑤ 产品化和产业化,并采用与外商合作或合资方式,一次仪表采用外商先进的产品,二次仪表国内制造和国内成套组装,利用低成本的优势出口国外。
3 方案选择
3.1 目前国内外的几种下渣检测方法简述
3.1.1概述
国内外试验研究或生产应用的示渣方法大致有下列几种:① 电阻法。在出钢口外侧安装一对电极,出钢时,电极间电阻小,回路通过一定的电流,当钢流混渣时,电阻增加,电流急剧下降。② 噪音法。在出钢口和钢包分别安装微音器,根据出钢时钢流摩擦产生的噪音、钢流落入钢包液面产生的打击声,检测这两个微音器的电混成信号,并按其频率变化来确定钢流混渣。③ 光谱法。出钢时,向钢流投射激光,分析由激光激起钢液中钢、渣光谱的特征,并根据分析值的变化测知渣的流出。④ 振动法。在钢包或连铸中间包塞棒或滑动水口的连杆操作装置装设振动传感器,测量振动情况来判别出现渣时信号变化,这种方法国内也有成品。⑤ 辐射能法。连续记录出钢时钢流辐射能、温度的变化,依据在同一温度下,钢液、炉渣表面辐射能不同而表面黑度有差别的原理来判别钢与渣。⑥ 电磁法。⑦ 热成象法。
上述各种示渣方法虽然不少是获得专利的,但比较准确和达到实用化的主要是电磁法和热成象法。
3.1.2几种下渣检测方法的原理

图1 电磁感应式示渣测量原理图
(1) 电磁法示渣系统。瑞典Studsvik公司、德国AMEPA公司都生产类似的电磁感应示渣系统。目前大型钢铁厂大都采用AMEPA公司的电磁感应法下渣检测系统(国内也生产类似的系统)。其原理见图1,当向线圈通入交变电流时,在被测物体产生涡流,这种涡流的分布、相位是线圈几何形状、频率和被测物体电导能力的函数,这磁场由二次线圈测定,由这电磁场的振幅和相位可推测出被测材料和物体的形状。
AMEPA钢渣检测系统包括传感器、前置放大器和外显示控制器等。传感器由两个同心线圈构成,套在钢包水口上(图3a,对于转炉或电炉等,则如图2所示安装在出钢口,此时也有采用发射线圈和接收线圈方式;对于连铸,则如图3所示安装在钢包或中间包水口上),在钢水流过时,由于钢水与渣的磁导不同(炉渣的电导率仅为钢液的千分之一,如果钢流中含有少量炉渣,涡流就会减弱,而磁场则增强),而可区分钢与渣,出现渣时,发出带渣报警并显示。
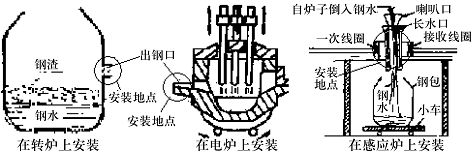
图2 电磁感应式示渣传感器在炼钢炉上安装图

图3 电磁感应式示渣传感器在连铸机上安装图
(2) 热成象式示渣系统。其原理如图4所示。用摄像机对准钢流摄像,监测出钢钢流表面,利用红外频率范围内钢水和炉渣的不同辐射行为,即红外线的范围内熔渣的放射率较钢水高的物理原理(即使钢水和熔渣有相同的温度,红外线传感器仍判定熔渣的温度较钢水高),用图像处理技术,通过计算机分辨钢水还是渣,当出现渣时,显示并报警。
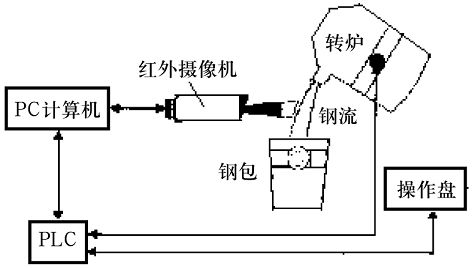
图4 热成象式示渣系统示意
3.2 方案确定与红外高温计的选择
3.2.1方案确定
根据调查表明:① 对于转炉下渣检测,开始不少工厂使用电磁感应法下渣检测系统,但都相继改为热成象式示渣系统,如日本NKK 公司福山厂3炼钢以前采用电磁感应原理, 在出钢口埋入线圈传感器的装置来检测炉渣, 由于出钢口形状的影响, 经常发生误报现象, 其可靠性成为问题,故采用了由德国AMEPA公司生产的热图像炉渣检测系统;奥钢联认为:常规的电磁探渣系统有一个线圈, 放在出钢口附近。由于暴露在高温环境下, 加上机械负荷较大, 一般要求的维修工作量也较大, 而这类维修一般在转炉砌炉时进行。系统一旦在计划砌炉时间之外出现问题, 就会降低系统的作业率或中断正常的转炉生产以进行维修。电磁探渣系统的另外一个缺点是用于新出钢口时其功能一般会受损, 直至出了若干炉钢之后才会正常, 往往头几炉出钢时不使用探渣系统的早期预警功能。为此, 开发了新型热图像炉渣检测系统;又如宝钢认为电磁感应下渣检测系统难以维护,或效果不尽理想,常常导致操作工必须使用肉眼来观察钢流下渣情况。然而,由于烟气、灰尘等的影响操作工很难及时发现转炉出钢过程中下渣的发生,故使用热图像渣检测系统(AMEPA TSD系统);② 目前,电磁感应法下渣检测系统主要用于连续铸钢过程的大包(钢包)往中间包(图4)或中间包往结晶器注入钢水时检测下渣和进行自动控制,但是也出现和用于转炉同样问题,而使用振动法下渣检测系统或光强度法等下渣检测系统;③ 普遍认为热图像炉渣检测系统太昂贵,对大型转炉较为适合。
基于以上调查和研究分析,特别是面对众多的转炉、连铸机组,应该寻求一种有效和便于安装维护以及低成本的下渣检测系统。因此,确定采用无接触、使用寿命长和工作可靠的系统,为此使用类似图4的系统,但采用直接测量钢流温度的方法,研究表明,由于钢水和渣的辐射率即黑度系数不同,故即使钢水和熔渣有相同的温度,红外高温计仍可判定熔渣的温度较钢水高而可以检测到熔渣出现, 熔渣和钢水的放射率差值越大, 高温计越易检测到熔渣的出现(如图5所示)。这样,便有可能用常用的红外高温计代替复杂的和昂贵的热图像系统。
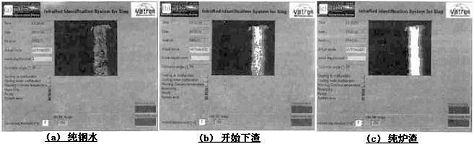
图5 钢水和熔渣和对应波长的放射率
3.2.2红外高温计的选择
红外高温计是辨别下渣的最终装置,因而它的选择是至关重要的。比较了多种红外高温计,我们选择了美国威廉姆逊公司(Williamson)的双波长红外高温计,它和传统工业双色高温计都是基于普朗克定律和维恩公式基本原理,测量相邻两波长的辐射能量,通过比值计算消除干扰,获得温度值。由于威廉姆逊双波长红外高温计在传感器的结构原理、波长选择及抗干扰能力的算法等方面有自己独特的专利技术,因此该产品具有测量精度高、长期稳定性好和抗干扰能力强等特点:
(1) 传感器的结构。传统工业双色高温计的两个滤光片对应于两个检测器,而且重叠放置,即称之为叠层双检测器。这两个检测器分别将过滤(λA&λB)后的辐射能量转变成电信号,输出到比例运算电路,从而获得与温度有关的信号。这种设计使波长λB的选择也受到了λA的带宽限制。另外,由于两个检测器的性能不可能做到完全一致,所以环境条件的变化会引起较大的误差,且不易修正。威廉姆逊双波长传感器的设计克服了上述的缺点,它将两个虑光片安装在同一个调制盘上,被测物体辐射的能量被调制成两波长(可根据应用任意选择)下的单色辐射能量,交替地投射到单一的检测器。
(2) 信号稀释因子。在实际应用中,测量光路中会存在着各种干扰介质,如烟雾、水雾、蒸汽、粉尘、氧化层、不干净的视窗或是机械障碍,致使传感器接受到的能量衰减。一般红外高温计对这些干扰介质都进行了补偿,不同厂家的红外高温计有不同的补偿能力,即补偿系数。这个补偿系数又称之为信号稀释因子η,它代表信号稀释的程度,它表示当传感器能够提供精确读数的同时所能承受的最大衰减比。例如:η=500:1表示传感器在测量光路中无干扰介质时正常检测到的能量为500,当因测量光路中存在着干扰介质致使传感器检测到的能量衰减到1时,传感器还能提供精确的读数。传感器的信号稀释因子越高,其抗干扰能力就越强。在传感器测量范围不同的测量段其η值是不同的。传统工业双色高温计在量程的上限η值最大25:1,即说明传感器在量程的上限接受到的能量衰减95%还能保证测量精度。而威廉姆逊双波长传感器在整个量程内任意点能量衰减95%都能保证精度。由于它在量程上限的η值为1500:1,所以即使能量衰减99.9%也能保证传感器的测量精度。因此,威廉姆逊双波长传感器具有较强的抗干扰能力。
(3) 波长选择。由于传统工业双色高温计的上层探测器既要对一个波段具有较高的响应,又要允许另一个波段通过。因此,它的两个波段的选择受到了一定的限制,在红外辐射测温实际应用中,影响温度测量精度最重要的干扰介质是水汽或水膜,所以在红外辐射测温仪的波长选择时主要考虑的是红外光对水的透过率。威廉姆逊双波长传感器可以很方便地避开水的吸收带分别选择两个波长。
(4) 传感器的长期稳定性。传感器的长期稳定性主要取决于硅探测器的热稳定性。硅探测器在波长大于0.96(microns)或小于0.6(microns)时,探测器的零点输出随环境温度变化而变化。对于普通工业双色高温计,由于波长选择在0.7-1.08(microns),部分波段大于0.96(microns)是导致了零点的不稳定的因素之一;另外采用的叠层双检测器也会因两个检测器老化引起的性能参数不一致造成零点漂移,有的厂家采用加热两个检测器来补偿这个稳定性,这样会降低传感器对于低温段的灵敏性,这也是它的稀释因子低的原因之一。威廉姆逊双波长红外高温计选择了0.7~0.8(microns)的波段,并采用单检测器,从而保证了传感器的长期稳定性。
(5) 根据不同用途,而有不同型号和应用软件。这也是威廉姆逊公司红外高温计与其他公司产品最大的不同点,它因不同用途,例如用于铝轧制、高炉热风炉、炼钢连铸、钢轧制(又分为板、管、处理线等)而有几十种型号,它根据实际现场不同点,如干扰、水气影响等而开发经过实际现场良好使用的不同软件,通常的高温计没有这种功能,而须操作人员调整仪表参数,如补偿系数等且可调手段有限,因而往往在实际现场不好用。
4 现场试验结果
本下渣系统是在首都钢铁集团公司二炼钢的210t转炉上及邢台轧辊厂铸造轧鲧进行的,该试验系统见图6。由于转炉出钢过程中,现场温度较高且环境恶劣,故使用的威廉姆逊双波长红外高温计被安放在距出钢流大约5米的距离,威廉姆逊双波长红外高温计经人工调整,对准出钢钢流1/2处,通过电缆将信号传送到5m以外的威廉姆逊数字式显示仪表并连接笔记本计算机。2006年共进行两次试验,结果是相同的。其结果如图7所示,可以看出钢水夹渣时出现明显的尖峰,与人工观察完全一致。
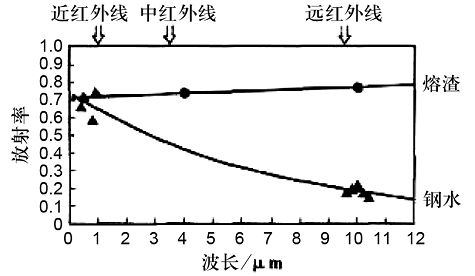
图6 新型下渣检测试验系统
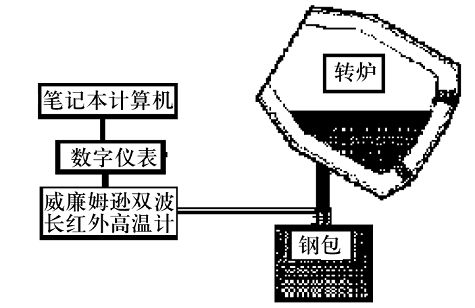
图7 新型下渣检测试验系统测定结果举例
5 结论及今后工作
从上述的试验可以看出,用双波长红外高温计直接测量夹渣是可能的,它比热成象方法成本是较低的。但还须进行进一步的试验,以获得更高的精度,包括最佳波长的选择,各种钢种的适应性,有无误报等。到完全实用化后,还得组成成套装置,包括自动控制系统(如报警、控制挡渣板等)。此外,由于现场环境恶劣,最好使用光纤远传(如图8所示),在有保护管的场合还得设计特殊安装方法(如图9所示)。
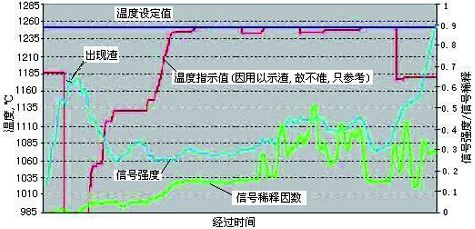
图8 带光纤远传的示渣系统

图9 辐射能式示渣系统用于保护管连铸生产
|