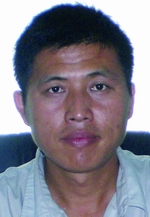
高玉坤(1975-)
男,吉林省吉林市人,1998年毕业于吉林化工学院工业自动化专业,现工作于中国石油吉林石化分公司乙烯厂仪表车间,工程师,从事化工装置控制系统的运行维护管理工作。
摘要:文中以吉林石化70万吨/年乙烯装置裂解气压缩机为例,介绍了机组控制系统冗余功能的设计方案及实现方法,阐述了冗余控制对机组系统可靠运行的重要性。
关键词:压缩机;控制;冗余;可靠性
Abstract: Taking the Cracked Compressor, which serves Ethylene Plant of JiLin PetroChemical
Company, as an example, this paper introduces the design scheme and implementation of
redundant functions of control system.. The importance of redundant control to reliable
running of compressor is also emphasized in this paper.
Key words: Compressor; control; redundancy; reliability
现代化工装置中,透平压缩机组的控制是比较复杂的控制。如何有效地保证控制系统的安全性,减少由于控制系统硬件原因导致的机组停车事故发生,是保证装置稳定运行的重要前提。文中以吉林石化70万吨/年乙烯装置裂解气压缩机为例阐述了机组控制系统冗余功能的设计方案及实现方法,从设计上提高了控制系统运行的可靠性。
1 机组简介
吉林石化70万吨/年乙烯装置裂解气压缩机组控制系统采用的是GE公司的Micronet 5009 TMR 集成机组控制系统(Integrated Turbine &Compressor Control)。该控制系统将调速控制、性能控制、防喘振控制、联锁控制等集于一身。为了确保机组的运行安全,该控制系统从供电系统、ITCC硬件、软件设计、操作等几方面均作了冗余考虑,能够避免由于单一控制元件的损坏而造成的非计划停车事故发生,并在实际应用中收到了良好的效果。
2 冗余功能的实现
2.1 硬件冗余
2.1.1 ITCC硬件冗余
乙烯装置裂解气压缩机组控制系统的主机架有三个独立Kernel单元,任意两个Kernel单元正常工作都能够保证系统的运行。每个Kernel单元由电源模块、CPU模块、串行通讯SIO模块、远程XCVR模块、I/O模块等组成。每个I/O模块连接独立的端子板(FTM)。每个CPU模块在运行前均进行硬件自诊断,相互间进行时钟同步。CPU卡件上部的状态指示灯会显示CPU的当前运行状态。自检通过后,“RUN”灯点亮。否则,相应的故障指示灯点亮。任意一个CPU所采集的数据都要经过三个CPU的计算,计算后对输出结果进行双向数据表决,最后分别由单个CPU输出正确的计算结果,并通过FTM送出(如图1所示)。当任意一个CPU计算结果出现错误时,另两个CPU会通过对计算结果的表决剔除坏值,实现了控制功能的冗余。
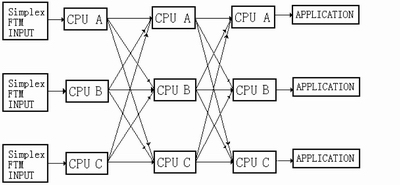
图1 CPU容错系统示意图
由于机组的控制及联锁信号较多,如果都采用三重冗余将占用大量的硬件资源。为有效地利用系统资源,吉化乙烯装置裂解气压缩机组控制系统的I/O信号分为两个等级:
一类信号是可以导致整个机组的失控、停车、设备损坏等,这类信号我们采用了三取二表决来实现。三取二信号主要由三个Kernel单元内的CPU分别对现场采集的信号进行处理(如图2所示),计算后再分别输出到执行元件,可避免单一测量元件和传输线路引发的故障,实现了回路完全冗余。这是和系统本身的单个FTM实现的三取二表决是有区别的。用于调速、联锁、防喘振、超速保护的输出信号均通过此发生实现冗余。如转速控制、控制油压力联锁、复水器调节阀、控制油跳闸电磁阀的输出等。
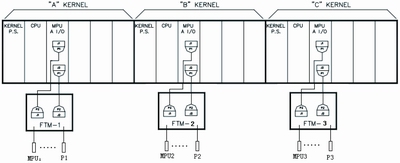
图2 I/O冗余示意图
另一类信号主要是用于显示、报警功能的信号,采用双重冗余。这些信号如果出现故障,不会引起严重的后果,我们把这些信号只通过B、C两个CPU进行处理。
2.1.2 电源冗余
为保证供电系统的稳定,供电系统采用了双重冗余设计。冗余的每个电源功率都能够满足负载的要求,正常工作时根据负荷分配负载。两路220VAC UPS5通过两个主开关输入到开关电源“#1”、“#2”,开关电源输出的24VDC经二级管、熔断器后给三个Kernel 单元的供电模块。Kernel电源供出的5VDC电源供给各自的卡件(如图3所示)。为了避免干扰,系统还采用了浮空对地的设计,提高了信号传输的可靠性。现场I/O的电源则是通过两路独立的外部电源来提供的。
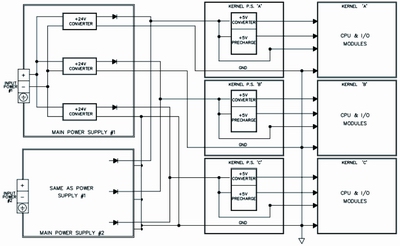
图3 冗余供电系统图
2.1.3 操作界面、通讯系统的冗余
为保证操作人员能够对机组进行有效的操作,乙烯装置裂解气压缩机组的人机界面系统也采用冗余设计。DCS和上位机系统均能进行操作,每个系统的操作界面均设有一个“Local/Remote”的切换开关,能够进行相互间的切换。所不同的是上位机采用的IFIX软件作了SOE系统,能够对机组的首出报警和控制系统诊断及工艺过程、机组运行状态的报警进行记录,而DCS系统的是只能记录工艺过程报警。这两个操作界面,无论哪一个出现故障,均能保证操作员对机组的正常监视、操作。
由于系统之间数据量交换较大,若都采用硬接线的方式,会极大的增加系统的容量,导致系统负荷过高,另一方面也会导致系统的成本增加。为了降低成本,ITCC和操作界面、其它控制系统之间的数据交换统一采用了冗余的RS485通讯方式。如DCS系统和ITCC系统之间、Bently 3500系统两机架之间、上位机和Bently 3500系统之间等(如图4所示)。由于RS-485通讯协议只能对整数进行传送,数据按照数值的大小,在发送端对数据进行升幂处理,然后在接收端进行还原,保证了数据传送的精度。并由软件自动进行冗余通讯回路间的切换。

图4 冗余通讯示意图
2.2 控制冗余
2.2.1 转速控制冗余
转速控制是机组的核心控制。通过DCS、HMI的速度设定,ITCC对转速进行调节,使透平的转速和速度设定值的偏差尽量减小。乙烯装置裂解气压缩机组的转速是通过三个安装在透平非驱动端的转速探头测量的。测量到的速度脉冲信号输入到FTM中(如图5所示),系统中的“SS_01”模块对数据进行处理。脉冲的数量除以测速齿轮的齿数,得出透平的转速。当转速超过测量的高低限时,“SS_01”模块输出FAULT,经过“MPUA_FLT_M”模块判断后剔除坏值,处理后的数据输入到“SPEED_MON”模块。当一路信号故障,“SPEED_MON”模块取另两路的转速信号取最大值参与控制;当两个转速信号出现故障时,“SPEED_MON”模块取剩余正确的信号参与控制。三路信号均出现故障时,“SPEED_MON”模块发出停机信号,从软件上实现了转速输入的冗余。
为了保证调速阀的可靠动作,乙烯装置裂解气压缩机组的电液转换器采用双线圈驱动。线圈分别由“A”、 “B”两CPU所带的FTM进行驱动。控制通道分AA、AB、BA、BB四个控制输出通道,每个通道正常输出为80 mA,当一个CPU故障时,另一个CPU的两个通道每个输出160mA。下面以AA、AB为例介绍调速阀冗余功能的实现(如图6所示)。
转速信号经过控制器、限制器,计算比较后,输出调速阀控制信号。AA、AB两个信号分别由一个A CPU 的FTM103的两个AC通道输出,输出的信号经压接在一起(如图7所示)。输出电流叠加,驱动电液转换器的线圈工作。当BA、BB组出现故障时,输出的信号由“ACT_A_SEL”模块,根据正常工作的数量,对输出电流进行处理,最终由“ACT_01”模块送出。四个控制回路均正确时,每组输出1/4的工作电流,当其中一个线圈或CPU故障时,另一个CPU所带的FTM,每个通道输出1/2的工作电流,能够保证一个CPU或回路出现故障时,调速阀仍能够正常工作,实现了调速输出的冗余。
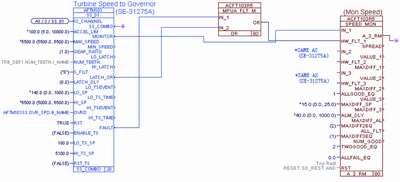
图5 转速控制MOE框图
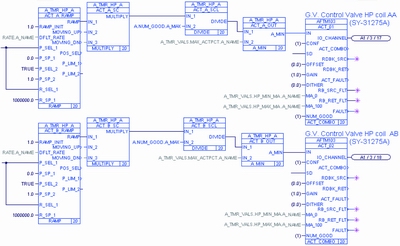
图6 调速阀冗余输出MOE框图
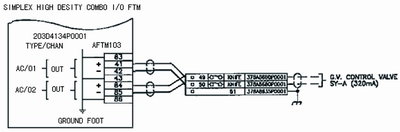
图7 调速阀冗余输出接线图
2.2.2 调节功能的冗余
乙烯装置裂解气压缩机组调节回路采用独立的现场测量元件,ITCC内部进行三取二冗余处理。如段间压力、流量信号、复水器液位控制信号等;其它非关键的显示、控制信号采用双重冗余的设计原则。如复水器的液位高报信号、密封器差压控制信号等。FTM接收的模拟信号可以为0~25mA或0~5VDC,这可以通过FTM上的电流/电压跳线选择来实现。由于电流冗余设计比较繁琐,我们采用了0~5V电压输入模式。电流电压的转换通过端子板内的200Ω电阻来实现(如图8所示)。为了防止过流,每个输入端子设有100mA的熔断器。数据冗余的处理通过CPU之间的同步数据交换和表决来实现。
通过软件对每个FTM通道的输出电流进行分配。对重要的控制回路,采用三重冗余进行控制;对不会引起严重后果的密封气差压调节、油箱温度控制等采用双重冗余进行控制。如三重冗余的调节阀,由每个AO通道提供1/3的电流。当一个通道故障时,由另两个通道每个通道负责1/2的电流。实现输出的冗余。通道故障的判断原理同调速阀类似。调节回路从输入到输出,实现了全回路冗余,大大降低了由于控制原因引起机组故障问题的发生。
2.2.3 联锁功能的冗余
为了避免由于采用结点开关容易受环境因素影响、回差大、故障率高的缺点,乙烯装置裂解气压缩机组的压力、温度、流量报警及联锁系统均采用变送器的测量方式。三个独立的测量元件经变送输出的4~20mA信号,输入到三个“Kernel”的不同通道,经过“Calc_plus”模块判断后,输出三个模拟信号的平均值。通过“A_Compare” 模块进行报警、联锁值的设定,比较后输出开关信号,参与逻辑的判断。机组的密封气泄漏流量联锁、控制油、润滑油压力低联锁登均采用这种设计思想,提高了安全性能。
数字量的输出均采用继电器进行隔离。三个”Kernel”的不同端子板上的继电器,通过硬线三取二表决来实现(如图9所示)。当其中的一个信号出现错误时,系统三取二表决后仍能够输出正确的结果。避免了由于继电器接点接触不良,信号电缆端子松动,卡件通道故障等原因造成的故障停机事件。
另一方面,为了保证机组运行的安全,对所有的联锁逻辑均采用“故障安全型”设计(正常工作时状态为“ON”,报警时状态为“OFF”),防止由于逻辑失效而导致危险的发生;为了防止机组超速,除设计两级电子超速外,机组还设计了独立的3取2超速保护控制器。三个独立的磁感应探头(MPU)将速度信号送入到ProTech 203系统中,系统可根据需要对MPU信号进行判断,发出停机或报警信号,参与跳车逻辑(如图9所示);对执行机组停机任务的泄油电磁阀,采用冗余并联方式,防止由于电磁阀故障,导致的危险发生。

图8 模拟信号冗余输入线路图

图9 联锁信号冗余输出线路图
3 结束语
在实际维护工作中我们也碰到过多次冗余系统避免故障的应用事例。如Kernel“C”FTM的浮水器液位调节阀输出通道出现故障,由于我们作了输出冗余设计,另两个冗余的通道每个输出1/2的工作电流,没有影响到阀门的正常工作;二段吸如罐液位开关LS_31504A出现的故障报警,由于冗余的设计,均没有影响到机组的平稳运行。在2008年装置大检修过程中,我们也对乙烯装置裂解气压缩机组控制系统做了CPU冗余试验,在任意停掉一个CPU的情况下机组均能够正常运行,用实践检验了冗余的可靠性,为乙烯装置的安全稳定生产起到了至关重要的作用。 |