内容 | 活动链接:2012年控制网技术专题---实现石油与化工的信息化
1. 项目背景介绍
新疆油田地处荒漠,成千上万口采油井分布在广阔地域上,被按照采油井—计量站—转油站—联合站—采油区—采油厂—石油公司这样的多层次结构、按照“三级控制、两级管理”的模式进行生产管理。每一层级的控制,都需要大量的人员跑现场、抄表,效率低下,现场环境恶劣、员工工作负担重;同时,地面集输系统站点多、管线复杂,这些又都导致了采油成本增加。
石油物联网项目基于物联网技术、无线遥感遥测技术、先进通讯技术、计算机及其网络技术,结合先进的工业自动化软件和工业实时历史数据库软件,实现采油生产、管理自动化、信息化、智能化。
2. 项目目标与原则
依靠技术创新与突破,转变思想,改变传统工艺模式,最大限度的取消计量站,配水间等中间环节设施,优化采油区集输管网部署结构,按照统一规划、分步实施的方式,组织开展综合研究,重点做好示功图求产与单井计量、数据远程采集与传输、注水井的远程自动化技术、设备远程监控与维护管理、增产措施预案与执行等,达到优化工艺、节能降耗、辅助管理的目的,打造具有“两化融合”特色的数字化、信息化、智能化油田。为此确立技术与管理两方面的建设目标。
技术目标
(1) 建立集团公司统一的生产数据信息平台,逐步实现油田公司、二级单位及基层单位的生产信息共享。
(2) 建立统一的生产业务管理平台,实现真正的网上业务数据流转,而不仅仅是数据的存储和查询,更要为决策支持等提供高层次应用。
(3) 建立统一的设备管理平台,实现实时在线的设备状态监控,准确定位设备故障,及时处置,降低计划外停机时间。
(4) 在集团公司统一的生产业务平台基础上,实现任意地理位置可对生产信息进行详细的查询。
(5) 实现采油生产历史数据综合分析,研究采油生产各类地质状况下的最佳生产实践。
(6) 借助网络实现集团公司生产自动化、管理信息化、现代化和规范化。信息系统本身的目标,必须具备快速、便利的系统维护功能,可远程维护、远程升级,适应油田生产的地区分散性和业务的多变性及复杂性这些特点;
管理目标
(1) 提高生产管理水平,增强对油田生产的宏观监测、分析、指挥调度,科学管理石油增产措施;
(2) 推进企业信息化经营,宏观调控生产结构,合理控制生产管理,提高生产效率;
(3) 建立统一、开放、竞争、有序的生产秩序,不同层次、工段对比最佳生产实践;
(4) 建立统一指挥、管理顺畅、权责一致的油田管理体制;
(5) 利用信息系统随时提取、加工、汇总,及时掌握油田生产动态;
3. 项目实施与应用情况详细介绍
3.系统架构
为达到中石油采油生产物联网系统建设目标的要求,并保证系统的先进性、稳定性、易操作性等,中石油采油生产物联网系统架构采用数据采集层、存储层、应用层三级结构设计,每个层级使用亚控科技对应的相关软件产品,完成对中石油各石油开采生产单位的实时在线数据及图像监控及对各类生产、设备运营的数据统计分析以及增产措施管理等功能。
3.1.功能介绍
3.1.1数据采集
KingIOServer数据采集与设备控制工程采用专门定制开发的设备驱动与设备实现连接,通过解析设备的通讯协议,读取设备的实时数据,同时根据组态系统的授权检验和确认结果向设备发送控制参数和开关指令。
北京亚控拥有10余年工业控制领域软件开发经验,先后开发过千余厂商的3600多种大中小型智能设备的通讯驱动。拥有智能模块、RTU、PLC等各类国内外知名工控设备厂商设备的实际设备测试环境。
KingIOServer即作为KingSCADA软件的默认配置软件单元,又可以作为独立设备数据采集软件。它支持的数据采集包括:
模拟量:对温度,压力,位移、载荷、流量等数据进行实时采集及处理;
开关量:对状态信号,事故信号等进行实时采集及处理。
支持在线设备维护管理
无论是计划安排还是意外故障,生产停机维护、设备更换是必可避免的,KingIOServer软件支持系统在线状态下进行设备维护管理,能自动响应设备的更新。
支持多种硬件设备的通讯
虽然系统中主要采集的设备是各类传感器,由于现场智能仪表繁多且每种设备的可选余地较大,因此项目中所采用的数据采集软件能够快速、可靠的与市面上常见的生产商的硬件设备实现通讯,此外还支持各种通讯规约、通讯协议及总线。
数据采集软件除了能通过各种各类通讯方式(如有线网络、3G、WiFi等)和通讯链路(如串口、以太网及现场总线)通讯之外,还可以通过一些通用的软件接口(如API、COM、ODBC、OPC)与第三方系统进行数据交互。
灵活的采集控制
系统中支持灵活的数据采集方式控制,提供用户周期数据采集、数据变化采集等各种采集方式控制,支持用户为不同的测点设置不同的采集频率。
基于数据块的高速采集
在面对大量的实时数据采集时,传统的以变量为单位的方式,从变量,到包,是需要花费时间的,变量越多,这部分时间越长。对于采集速度要求较高的现场,这种方式显然并不合适。
项目中所采用的数据采集软件基于“数据块”来进行数据的组织和传输,可将重要的参数设置在一个数据块中,还可以对重要的数据块设置采集次数。这种以“数据块”为最小通讯单元的特点可提高数据采集和传输的速度。
与中心调度系统的交互
从系统整体架构上看,各油井、分站的数据采集系统不但担负着采集数据的工作,同时还肩负着与调度控制中心进行数据交互的工作。从数据传输的快速、安全、可靠角度考虑,此时不应采用OPC方式(OPC方式每次通讯时都需要建立组,在组中建立项,然后再进行每个项内数据包的请求与回应。数据帧还附加了OPC协议所要求的很多包头和包尾,较为复杂,容易出错,速度缓慢)。
各油井、分站与调度控制中心间的交互应该通过平台软件自身的内部接口来实现快速、可靠的数据传输与交互。
数据缓存
各油井、分站与调度控制中心间的出现网络中断、网速过慢情况并不多,但是一旦出现必将导致调度控制中心因数据缺失而造成分析的误差、决策的不准确。因此,系统需确保即便网络中断也不丢失数据。基于这一目的,数据采集系统提供了对于采集设备硬件的数据缓存的采集读取功能,当网络异常时,系现场设备可将数据缓存在本地存储,待恢复后,再自动将缓存的数据采集传送到数据库中。如此一来,可最大程度的确保数据的万无一失。
冗余
由于数据的统计、分析工作是建立在大量连续历史数据基础上的,因此如果出现数据丢失将造成分析的误差,因此为了保证数据连续性此处的两个数据采集系统互为冗余。为了减少因网络不稳定导致的误切换,将采用专门的冗余状态探测通道,通过配置专用网卡实现快速的切换,做到1S内的切换。
故障诊断
在数据采集过程中,数据采集系统会对各监控点进行通讯性能诊断和统计,如:连接成功时间,当前使用数据块个数,最后一次更新成功时刻等。当某个设备发生数据通讯异常时,数据采集系统会迅速诊断出并产生能够产生相关报警,以通知相应人员进行处理。
数据采集系统向操作人员提供一个直观的监视窗口,操作者不用再通过观察界面数据刷新情况来判断,提高故障诊断的效率,为尽快排除故障争取了时间。
3.1.2SCADA系统
KingSCADA作为整个系统的工程核心,完成站控的图形界面组态、设备控制授权检验、设备控制确认过程组态、系统实时历史状态分析等功能。
画面监视
操作人员可通过SCADA系统的图形界面对系统进行监控,控制权限由登录的用户角色确定,分别分为管理员、操作员和工程师三种角色。将整个组态系统分为调度管理、系统监控和系统维护三个模式,不同角色和权限的用户只能进入授权的安全许可的模式。
如管理员可以控制整个系统,可以:在指定的系统监控模式工作,应能执行:
对系统内的所有设备实施控制;
接收和确认来自整个系统的报警;
所有显示的监视;
指令和设定值。
如工程师可以设置整个系统的配置参数:采油各类报警参数、注水各类报警参数、注水量控制参数等。
还可以做配置用户,退出系统等高权限的操作。操作员只能进入调度管理模式。而工程师可以进入系统维护模式。
大画面漫游及无极缩放
SCADA系统图形展示的直观逼真与否将关系到操作人员作出判断的及时性和准确性。为了便于操作人员日常的监控,SCADA系统提供大画面漫游及无极缩放的功能。其目的是在一个界面上可以进行总体的全局的监控,也可放大到某一局部环节进行精细的监控,监控画面无需来回切换。
丰富的动画效果
SCADA系统具有多种动画连接,如鼠标特性、过渡色、透明色等,图形界面采用GDI+技术。利用这些动画效果,在上位机即可再现现场的工艺环节,帮助操作人员快速准确作出判断。
画面集成
在油井、站控的SCADA监控画面中,将把视频信号集成进来,目的是画面中的工艺流程能与现场实际动作情况实现对应。比如,当操作人员通过画面监控某油井、某输入管道的运作情况时,能同时观察到该位置的视频图像,以便进行状态的核实。如此一来,操作人员无需再到现场观察控制情况。
报警处理
SCADA系统可以对生产过程中设备状态及运行参数的变化进行判断,当发生异常时予以及时的报警,如越限报警等。
当产生报警时,在控制界面上有相应的指示灯闪烁,同时可发出报警声响加以提示。报警的笛声在确认后可。
当产生报警时可以有实时报警窗弹出,也可以事先实时打印一条报警信息。
报警分999个报警级别。不同的级别可用不同的颜色表示,如流量橙色预警。
报警信息在报出的同时也一并存入报警数据库。记录这些内容:
报警事件生成的日期/时间;
报警组;
报警标记名;
报警标记的类型(实型/整型/布尔型);
报警类型(低低,低,高,高高,计数,偏差等);
操作员,确认报警的节点名,报警优先级等;
如果需要可以对报警信息进行查询,具有条件查询的功能,如按报警时间查询、按报警类型查询、按记录类型查询等,可以实现多条件组合查询,为了方便查询条件的组合,支持基于SQL的标准化查询语句。查询结果可按需要进行打印。
报警通知
报警发生时,可以通过播放语音,拨打电话,发送短信,发送Email等形式通知各级人员。通知的重要说明都是具体的文字说明而事件代号。被通知的人员按照不同的级别,得到的内容各不相同(如可以将级别划分为:领导层、指挥层、用户层、操作员层、供应商层等),操作员得到的消息可能是某某事故,请速采取何措施。而领导者可能会得到更为详细的消息,如某某事故,请速采取措施,未来5分钟之后,管线泄漏将是如何的。
趋势分析
SCADA系统提供的趋势分析包括:实时趋势分析和历史趋势分析两种。
实时趋势: 来源于一系列的采样值,这些采样值按时间划分,然后组合成图形直观的显示过程情况.。
历史趋势: 通过历史趋势曲线使操作人员直观的了解设备的历史运行状态.操作人员可以自由设置曲线的起始时间,时间跨度,以及趋势浏览翻动的跨度.通过左右游标定位当前趋势点的值.并且提供趋势打印功能.
实时趋势分析、历史趋势分析均通过SCADA系统提供的趋势曲线控件来完成,控件除支持常见的曲线添加、隐藏、删除、打印,游标设置,滚动、缩放的功能外,还具有一下特点:
横向、纵向比对
系统趋势分析,不单是简单的曲线观察,还涉及到趋势对比的要求,对比可以是横向的也可以是纵向的。
纵向对比:比如,对一个输入管进行检修以后,可将其当前的流量趋势与一个月前的流量趋势进行对比,以了解检修的效果。
横向对比:比如,两个完全相同的管线,可以通过观察相同参数的趋势曲线,了解两者的性能的差异。
为了保证该功能的实现,SCADA系统提供的趋势曲线控件具有多个绘图区,每个绘图区域提供多条X轴与Y轴,每个绘图区域至少支持16条趋势曲线。
分组分类
可对参数进行分组、分类,操作人员可通过数型控件进行选择,实现曲线的快速替换。分组分类的目的是快速查找、快速选择、快速绘制。
冗余
系统中除了数据采集系统实型双冗余之外,为了保证系统监控的安全稳定,SCADA系统也采用双冗余的方式,当主系统故障的时候,备份系统将立即接管主系统的工作,不至于造成上位机监控的瘫痪。冗余功能的重点:
快速切换
切换速度是否快速是衡量SCADA系统性能的指标之一。从各站控运行安全角度考虑,冗余切换速度应尽可能快。SCADA系统与数据采集系统部署在同一个服务器上,因此SCADA系统也将采用独立的探测通道,通过配置专用网卡实现快速的切换。当服务器出现故障时冗余系统能够自动完成切换,切换时间小于1秒。
不丢失数据
在冗余切换过程中应保证实时数据、历史数据、报警数据的完整,这些数据是不允许丢失的,以便操作人员随时利用。因此在故障恢复后,两个SCADA系统将进行数据同步,同步的数据包括:实时数据、历史数据、报警数据。
系统的开发与维护
当现场运行的软件工程难免会需要修改及调整,要想轻松的完成工程的修改,软件产品的开发环境的功能一定要强大,其目标是:尽量减少工作量。SCADA系统的开发环境具有下列功能特点:
提高开发效率
不受限于显示器的分辨率,支持无极缩放功能,可在泵闸总貌与局部之间漫游,方便工程的开发。
提供数据模型。对于存在多个相同设备的场景,通过模型复用的方式快速新建设备、数据点、逻辑脚本等,避免重复性的建点、添加逻辑关系的工作。修改时通过修改模型,传播至所有对象上,达到一劳永逸的效果。
提供图形模型。对于存在多个相同图形对象的场景,通过模型复用的方式快速建立图形对象以及对象中的属性、动画连接等。在修改时,通过修改图形模型,可传播至所有图形对象上,以减少工作量。
开发环境提供批量建点、变量导入、导出、合并功能。当变量点数达到一定数量之后,为避免查找变量的困难,开发环境提供变量的快速搜索定位功能。提供全中文变量名和函数名的定义方式,方便开发人员的识别。
实现好的开发效果
提供水行业图库精灵,开放过滤色、透明色等图形属性,提供位图联播、鼠标特效等动画连接,以便实现水行业特有的工艺特效。
提供脚本开发平台,可以就系统事件、数据改变、报警、热键触发、调度等多重事件编写脚本,以类C语言作为内置编程语言(C语言简单且普及性高)。
开发环境提供各种函数,如三角函数、数制转换函数、报表函数、数据库操作函数、权限函数等。
保证工程的安全性
工程的开发环境可进行加密,没有权限的工程人员无法进入修改。
工程开发完毕后,为避免开发的失误造成运行的错误,开发环境提供编译功能,自动提示错误个数及错误位置;在参数设置时若设置错误(如数据类型错误),在编写脚本语言时若出现语法错误,系统会自动提示;
3.1.3数据库系统
3.1.3.1数据库建设要点
数据库建设要遵循以下要点:
1.根据系统有关的空间数据、属性数据、运行数据、业务管理数据等数据的要求,设计合理的数据库体系,使之在范式水平、冗余度和可操作性上有一个合理的平衡和可扩充性;
2.各类数据分类与编码、数据精度、作业规程等应符合现行相关国家标准、行业标准的规定;
3.数据库的设计应考虑实施中与各分调度中心等相关系统的数据交换与接口;
4.进行数据库设计时,根据该系统情况分别对管理数据和其它数据的量进行估计,合理设计数据库结构。
数据库系统建设,要坚持从大局着眼,用系统工程的思想方法把握全局。数据库设计应在规范化,标准化的前提下,在稳固和安全的基础之上,重灵活性、开放性、先进性等。同时要面向调度中心未来的业务发展需要,注重资源配置、数据标准化、资源共享、数据更新、以及数据库系统的可扩展性与安全性,统筹规划、严格管理,使整个数据库系统建设具有突破性和前瞻性。
3.1.3.2数据库组成
根据中心的业务功能需求,数据库从建库内容上来说主要包含以下几个方面:
运行实时数据
设施类数据
设备类数据
监测类数据
业务类数据
管理类数据
系统类数据
其他数据
数据之间的关联主要依靠地理位置关联、属性ID 关联、时间关联以及业务功能权限关联。建立数据库主要工作是分清数据库的概念组成,定义数据库逻辑结构,包括空间数据的分层、属性数据关系表定义、属性与空间数据的关联定义等,最后将这些数据库的逻辑设计在数据库中加以物理的实现,包括存储策略、分布策略、索引策略等。
3.1.3.3数据库的部署
在调度控制中心的工业实时历史数据库服务器上部署工业实时历史数据库KingHistorian,用来存储海量的、具有时间特性的过程数据;使用用户自定义关系数据表存放的是一旦确定不会经常性变化的数据,如工作班次、管理类数据等。
3.1.3.4工业实时历史数据库系统
数据采集
数据压缩过滤方案
经过分析项目中数据可以根据数据变化的频率区分:变化快速且不规律的,需要进行快速采集;变化较少的,只需变化时进行存储;存在一定比例关系的,可以在过滤后进行存储。工业实时历史数据库在数据采集时便提供3种以上的压缩方式,如死区压缩、旋转门压缩等。
下层数据订阅方案
对于工业过程数据采集,通常采用两种方式:周期轮询、订阅。对于变化频繁的数据,一般采用周期采集,可设置采集周期;而对于变化较少的数据,通常采用订阅方案,即只有数据值发生变化时,才会采集并存入工业实时历史数据库中。
数据存储
针对非常高数据采集密度的需求,数据采集方案可使实际到达数据库数据得到降低。同时对于如此庞大的数据,最终进行归档时,适当的数据压缩也是必要的。工业实时历史数据库在数据存储时同样提供死区压缩、旋转门压缩、改进的死区压缩等多种压缩算法,在保证数据压缩前后趋势不变得前提下使得所消耗的磁盘空间下降。
存储瓶颈
普通磁盘系统,硬件的存储速度约为20M Byte/1秒,这样的存储速度,一秒钟存20万点数据,以每条数据8Byte计算,存储需要的机械速度是1.6M Byte/1秒,完全是符合需求的。工业数据主要的组织格式是以变量为索引的时间顺序,因此,当一次写入不同变量的数据时,也需要相应的磁盘寻址时间,而并不是20万点数据及时一次写入磁盘的连续区域。
真正耗费时间的是磁盘寻址,也就是磁头在磁盘面上转动和伸缩的时间,而真正用来读写数据的时间是小部分。而数据查询则是需要磁盘寻址最频繁的操作。由于硬件的操作才是整个系统的瓶颈,本项目所采用的工业实时历史数据库采用了采集缓存机制,只有整个工业库的缓存数据区满后,才一次性写入到磁盘上,尽最大可能减少磁盘寻址时间和硬件交互时间。
为了解决数据存储的瓶颈问题,工业实时历史数据库采用批量数据写入的存储机制。如上图所示,采用非Windows系统缓存的工业数据库专用缓存,保存实时数据,只有当累积到一定的数据量只后才会一次性的将数据写入到磁盘上,这种机制可减少磁盘寻址,避免数据存储瓶颈对数据存储的负面影响。
归档数据压缩
对于一个变量的一条记录,按变量名id 4Bytes、数据值8Bytes、时间戳4Bytes、质量戳1Byte、数据版本1Byte计算,一条关系数据记录有18Bytes组成。对于工业实时历史数据库而言,经过压缩以后,实际上一条工业数据库记录大约只有7Bytes,因此整个工业实时历史数据库可以节省非常多的磁盘空间。
数据检索
数据处理查询
数据库的最终价值体现在它能够支持数据处理与数据分析,使其它系统如决策支持和专家调度系统获得有用的信息,而这些获取信息的过程,必然伴随数据的并发查询与检索。
实现高速并发历史数据查询的方案
访问历史数据唯一的制约因素就是硬盘访问速度。工业实时历史数据库专门开辟了一个内部缓冲区,查询数据时首先在缓冲区查找符合条件的数据,若不能,再到硬盘上读取相应的数据。在有大量客户多次并发查询时,有很多次查询可以在内存缓冲区中完成,这样做可以减少磁盘寻址的次数和规模。
统计、分析数据查询
有些数据查询是伴随着对这些数据进行计算,如某个时间点上的开关量,单纯的这个数据值只能说明测点处在开或关的状态,没有其他的意义。但是当数据经过处理分析,如对机泵运行时间进行统计、累计流量进行统计等,对调度决策就具有另一种意义了。它要求系统提供便于设置的计算平台工具。对数据的统计分析见“调度计算平台”。
开放性接口
工业实时历史数据库支持以SQL方式对历史数据的查询,它采用开放的系统结构,支持API for VC ++/VB/.NET、OLEDB、ODBC、COM等数据接口,可满足系统二次开发的要求。此外还可以与关系型数据库进行数据互访。可以从其他的应用程序或其他数据库中导入数据到历史数据库当中,例如SQL Server、Oracle、Excel、Access等。
在线\离线方式的灵活设置
支持单独或者批量组态标签点,包括创建、更新、删除、查询标签点以及相关属性;为了平衡控制系统的数据通讯负载,系统支持针对过程数据特性,进行单独或者批量定义标签点采集频率;支持在线新增、删除标签点,修改标签点属性;支持离线和在线两种方式进行数据库组态和配置。
安全性、可靠性
工业实时历史数据库采用角色权限(读数据角色,写数据角色,配置变量角色等等)、用户权限相互配合双层安全管理体制,保证数据安全。
另外,项目中所采用的工业实时历史数据库还支持冗余与镜像的系统架构,保证系统的稳定与可靠,其原理如下图所示:
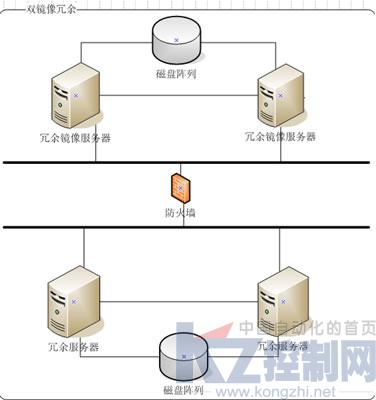
图 冗余结构
通过这样的镜像冗余系统,可以保证存储、分析数据与网络展示用的数据分开,即使网络上使用的数据遭到破坏,只是镜像系统的损毁,只要更新进行镜像就可以恢复数据,保证整个数据系统的高可靠性和高可用性。
3.2数字化油田与最佳生产实践管理
系统提供专业的石油采油分析功能,提供针对于采油设备的专业示功仪数据采集、存储、分析与展示,提供专门的增产措施管理,利用宏观控制图提示增产措施方式。
3.2.1示功图
系统实现采油生产实时监控与管理,通过专业的抽油机功图,完成功图求产与抽油机故障分析检测。系统将示功图、电流图原始数据在工业实时数据库进行长期管理,后期分析不需要任何加工就可以直接调用。依据载荷位移关系,分析抽油机产液量、分析采油生产是否正常,实现生产管理与控制的自动化与信息化。
分析主要诊断结果为:气体影响,游动凡尔漏失,抽油杆断脱,卡泵,供液不足,固定凡尔漏失,气锁,连抽带喷,固定凡尔卡死,泵严重磨损,完全液击,柱塞脱落出工作筒,液体或机械磨损,泵上碰,泵下碰,泵工作基本正常等。
相关计算方法
Gibbs波动方程
求解该公式的算法:
1、通过位移差分法得到以下公式
根据位移边界条件,力边界条件 及初始值 可求得杆各点的位移,及载荷 并可以进一步绘出示功图。
2、通过速度差分法得到以下公式
通过对速度进行数值积分可以得到相应的位移。
3有限差分法得到以下公式
则任意节点i时刻j的动载荷以Fij表示
5.2宏观控制图
系统采用宏观控制图,完整分析油田生产潜力,为增产措施科学管理与实施提供技术知识和信息保障,为实现采油生产最佳实践分析提供有力工具.
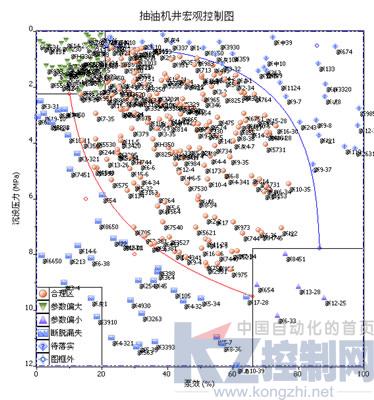
图 宏观控制图
4. 效益分析
通过采油生产物联网系统的建设,采油工将可以通过电子巡井、远程操控等手段,是每月野外工作量降低50%~70%;地面集输系统将优化掉站点30%左右,集输管线每年能节省资金过百万元。
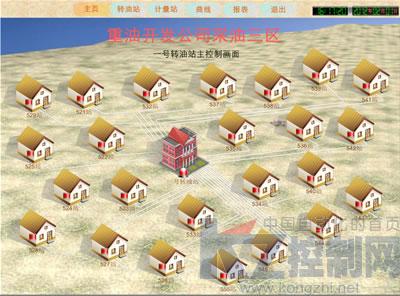 |