内容 | 摘要:结合SMT模块人工检测的工作过程和自动检测要求,本文介绍了检测装置的设计组成和控制原理,并详细说明了控制程序的设计思路和设计框架,实现了检测数据自动采集、检测结果自动判断、多工段实时共享检测信息等,极大地提高电能表生产企业的SMT模块检测效率、增强检测质量控制以及对加工故障的统计分析,并且为模块维修提供了较为清晰的故障原因便于维修。
关键词:ADAM模块;SMT模块;串口服务器;自动检测装置
Abstract: Based on the manual test procedures of SMT modules and its automatic testing requirements, this paper introduces the design and control principles of an automatic SMT modules test system together with a detailed description of the design ideas and framework of control software. The system supports auto acquisition of test data, auto check of test results, real-time sharing of multi-section’s information and diagnostic report of failed modules.Therefore, it can greatly improve the test efficiency of SMT modules in electric energy meter production enterprises. The system also provides statistical fault analysis to enable an enterprise to improve its manufacturing process.
Key words: ADAM(Advantech Data Acquirement Module); SMT (Surface Mounted Technology) modules; Serial server; Automatic test device
生产车间SMT模块加工完成之后,目前采用指针式表头、LED指示灯结合简易工装的办法进行检测,测试点一般设计较少,检测的结果采用模块加工流程单进行记录,检测质量主要依靠工人个人的素质与能力,检测效率较为低下,检测质量一般难以控制,并且品质部后期对检测记录做统计分析的工作量很大。
根据SMT模块检测的工艺要求,技术部提出了自动检测装置设计的基本要求,再结合车间当前人工检测的过程,设计出一款实用的SMT模块自动检测装置。
SMT模块自动检测装置采用ADAM模块作为AD信号采集、脉冲信号采集、开关量信号采集、开关量输出控制,检测类型丰富、测试点组合比较灵活,结合PC机自动检测软件,实现检测数据自动采集、检测结果自动判断、多工段实时共享检测信息等,极大地提高电能表生产企业的SMT模块检测效率、增强检测质量控制以及对加工故障的统计分析,并且为模块维修提供了较为清晰的故障原因便于维修。
1 SMT模块自动检测装置基本要求
1.1 结构设计基本要求
采用下面针床固定上面汽缸顶压方式,每次可同时测试4个SMT模块,具体可参考图1的工装结构。
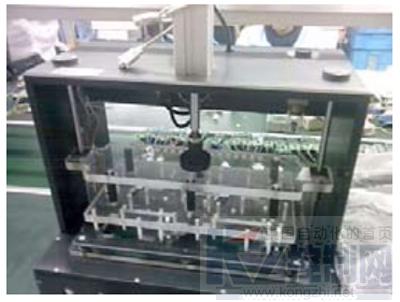
图1 工装结构参考图
1.2 硬件设计基本要求
(1)按键要求
前面板按键示意如图2。
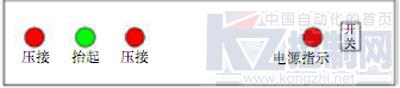
图2 前面板按键示意图
• 设置硬件手动开关,用于控制整个装置上、下电;
• 气动压接设计双压接开关,防止因不小心碰到开关引起误操作;
• 解除压接设计单开关。
(2)电源要求
• 检测装置采用隔离电源,电压可调(满足220、100、57.7VAC输出要求);
• 交流电压源0~2V,电压信号可调,用来提供计量电路采样输入测试信号;
• 直流24V、12V、5V、3.3V电源,电压精度控制±0.05V。
(3)信号量输出
• SMT模块自动上、下电控制信号,1拖4公用;
• 检测结果状态指示信号,不合格表位亮红灯提示,1×4分开控制。
(4)信号量输入
• 校表脉冲采集,1×4分开采样;
• 时钟脉冲采集,1×4分开采样;
• 无功脉冲采集,1×4分开采样;
• 报警继电器输出采集,1×4分开采样
• 拉合闸继电器输出采集,1×4分开采样。
(5)模拟量采集
• 485电源电压(5VDC),1×4分开采样;
• 时钟电池电压(3.6VDC),1×4分开采样;
• 稳压管前工作电压(7-30VDC),前端增加分压电路,1×4分开采样;
• 稳压管后工作电压(7-30VDC),前端增加分压电路,1×4分开采样;
• MCU工作电压(3-5VDC),1×4分开采样;
• 时钟电池电流(1-1000uA),前端增加电流放大电路,1×4分开采样;
• 停抄电池电流(10-2000uA),前端增加电流放大电路,1×4分开采样;
• SMT模块接线端子N电流(交流电流10mA以下),1×4分开采样。
(6)通讯测试
• 485 1通讯测试,1×4分开,响应应答模式;
• 485 2通讯测试,1拖4公用,响应应答模式;
• 红外通讯测试,1拖4公用,响应应答模式。
2 自动化检测装置系统硬件设计及控制原理
2.1 硬件设计
整个系统主要由ERP服务器、管理系统(PC机)、串口服务器、ADAM模块、信号调理板、汽缸和针床等几部分组成,将其中的串口服务器、ADAM模块、信号调理板、汽缸和针床制作成一套检测装置。
整个系统的网络拓扑图如图3所示。
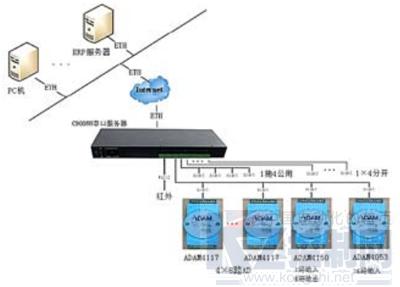
图3 系统网络拓扑图
根据自动检测装置硬件设计基本要求,主要部件选用如下:
(1)串口服务器
• 根据模块测试数量为4时至少需要端口数量为7,并且支持RS485/RS232可设,选用杭州冠科信息技术有限公司生产的C9008H系列8口三合一串口服务器。
(2)模拟量采集模块
• 根据模块测试数量为4时需要AD通道数量为8×4=32路,选用4个台湾研华远程I/O模块ADAM4117。
(3)信号量输入、输出模块
• 根据模块测试数量为4时需要信号量输入通道数量为20路、信号量输出通道数量为5路,选用台湾研华远程I/O模块ADAM4150(7路输入、8路输出)和ADAM4053(16路输入)各1个。
(4)信号调理板
信号调理板需满足以下几点:
• SMT模块上、下电控制;
• 提供多种规格隔离输出的交流测试电压;
• 提供多种规格直流供电电压;
• SMT模块通过针床顶针接触测试点检测的原始信号需要进行预处理才能接入到ADAM模块,如电流检测信号转换成电压信号、无源脉冲信号输出转换成有源输出、拉合闸控制脉冲信号转换成高低电平信号输出等;
• 各种引出线转接。
基于上述原因信号调理板采取自制,硬件设计原理图参见图4。
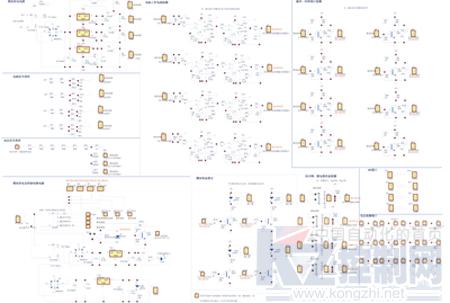
图4 调理板硬件设计原理图
2.2 控制原理
该检测装置通过汽缸从上往下顶压SMT模块使针床顶针接触各测试点,检测信号首先经过调理板转接或信号预处理,然后连接到ADAM模块,其中ADAM4117模块负责电压采样、ADAM4150和ADAM4053模块负责脉冲量、高低电平信号的采集,检测控制软件通过串口服务器读取ADAM模块采样结果,并根据加载的检测方案配置的阈值参数进行合格与否判断,判断的结果上传到ERP数据库服务器,最后由ERP系统提供数据共享。另外SMT模块的上、下电由检测控制软件通过串口服务器控制ADAM4150模块输出高、低电平信号控制调理板上电源控制继电器吸合、断开实现。
3 自动检测控制程序设计
3.1 编程环境、数据库选用
考虑到ADAM模块的驱动及样例采用C#语言,上位机软件编程环境选用 Microsoft Visual Studio 2008。
考虑到与ERP系统的数据接口,本地保存采用ACESS数据库,远程直接在ERP的SQL Server 2008中开放空间保存。
3.2 SMT模块自动化检测工作过程
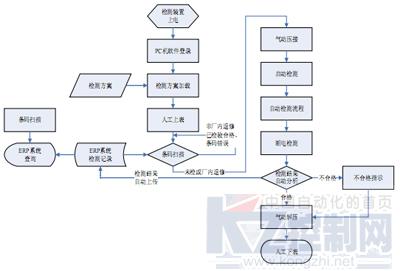
图5 SMT模块自动化检测工作过程
SMT模块自动化检测工作过程主要包括检测装置上电、PC机软件登录、检测方案加载、人工上表、条码扫描、气动压接、启动检测、自动检测流程、断电检测、检测结果自动分析、不合格指示、气动解压、人工下表等。
SMT模块自动化检测工作流程即为控制程序设计的基本工作流程,参见图5。
3.3 软件设计思路及设计框架
3.3.1 软件登录
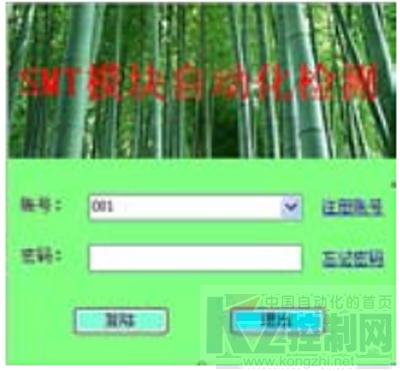
图6 软件登录界面
具备帐号、密码输入窗口;有注册帐号管理连接、忘记密码提醒连接;点击登陆按钮登陆系统,点击退出按钮退出登录。
3.3.2 检测方案加载
检测操作界面如图7所示,点击打开按钮加载预先配置的检测方案,参数配置包含如下内容:
• 工序名
检测方案系统参数,检测方案编制时可配置,主要用于检测记录数据保存的大类区分,工序名称如SMT功能检测。
• 整机物料编码
检测方案系统参数,检测方案编制时可配置,主要用于检测记录数据保存的大类区分。
• 条码段
检测方案编制时可配置,主要控制条码输入范围,如该检测方案对应订单条码段为123456789101至123456789901,那么此号码段以外的条形码将无法应用此方案进行检测。
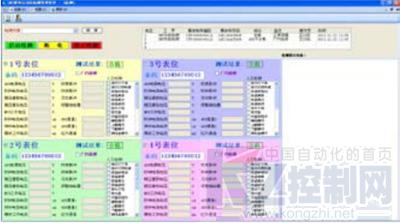
图7 检测操作界面示意图
• 485电源电压
检测方案编制时可配置判断阀值,并且该项目是否测试可选。
• 时钟电池电压
检测方案编制时可配置判断阀值,该项目是否测试可选。
• 稳压管前电压
检测方案编制时可配置判断阀值,该项目是否测试可选。
• 稳压管后电压
检测方案编制时可配置判断阀值,该项目是否测试可选。
• MCU工作电压
检测方案编制时可配置判断阀值,该项目是否测试可选。
• 485通道1
检测方案编制时可配置检测命令(含初始化命令帧),命令可以是一条或多条,并能配置返回帧判断内容,该项目是否测试可选。
• 485通道2
检测方案编制时可配置检测命令,命令可以是一条或多条,并能配置返回帧判断内容,该项目是否测试可选。
• 红外通道
检测方案编制时可配置检测命令,命令可以是一条或多条,并能配置返回帧判断内容,该项目是否测试可选。
• 校表脉冲
检测方案编制时可配置采样时间、采样脉冲个数范围,该项目是否测试可选。
• 无功脉冲
检测方案编制时可配置采样时间、采样脉冲个数范围,该项目是否测试可选。
• 时钟脉冲
检测方案编制时可配置采样时间、采样脉冲个数范围,该项目是否测试可选。
• 时钟电池电流
检测方案编制时可配置采集电流的延时时间、电流判断阀值,该项目是否测试可选。
• 停抄电池电流
检测方案编制时可配置采集电流的延时时间、电流判断阀值,该项目是否测试可选。
• 模块工作电流
检测方案编制时可配置采集电流的延时时间、电流判断阀值,该项目是否测试可选。
• 报警继电器输出状态
检测方案编制时可配置该项目是否测试可选。
• 拉合闸输出状态
检测方案编制时可配置该项目是否测试可选。
• 人工检测项目
检测方案编制时可配置人工检测项目,人工检测项目有:液晶、背光、LED灯、上下左右四个翻页按键、编程键、开盖开端钮按键等。不合格描述有:缺划、液晶黑点、液晶偏、背光不亮、背光有赃物、背光脚断、蜂鸣器不响等。
根据上述参数要求,检测方案数据库设计为三张表,表之间关联字段为方案编号,由数据库自动生成,具体如下:
• 检测方案表TXL_Scheme

• 检测方案具体内容表TXL_SchList
表1 具体检测类型对应参数
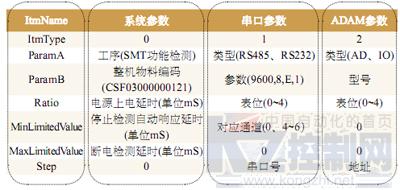
表2 具体检测类型对应参数
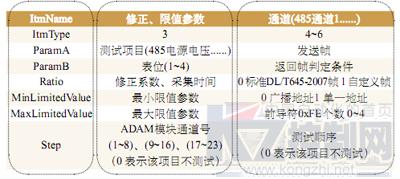
表3 具体检测类型对应参数
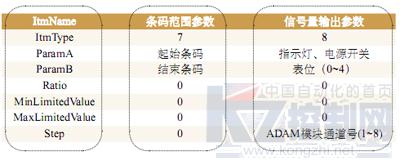
• 人工检测项目表TXL_SchList
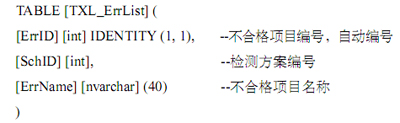
3.3.3 接口初始化
根据检测方案,自动配置串口服务器扩展的虚拟串口,并对ADAM模块初始化。
3.3.4 条码扫描
人工上表后用电子扫描枪手动扫描模块条码,条码输入注意必须将模块放入表位与界面对应输入窗口表位一致,保证测试数据保存信息的正确。如果是厂内返修模块,需勾上厂内返修选择项。
软件设计思路:首先根据扫描的条码判断条码的有效性(12位长度),长度不对,提示条码错误退出;长度正确,判断是否为厂内返修;厂内返修,进入下一步流程;不是厂内返修,根据条码、工序名读取ERP数据库进行验证;存在对应的合格记录,不允许进入下一步流程并提示条码已检;不存在合格记录,进入下一步流程。
3.3.5 气动压接
模块压接,采用气动操作,压接后微动开关触发软件启动电源控制端,被测模块上电。
3.3.6 启动检测
等待被测模块电源稳定(时间可设,缺省100ms),自动启动自动化检测流程。
设计思路:自动化检测流程按照检测次序依次进行,是否对某项目进行测试根据方案设置。
主要预设检测过程有:
• ADAM模块启动AD采样,测试值实时在界面上显示(测试合格的数值显示蓝色,不合格的显示红色);
• ADAM模块启动I/O采样,测试值实时在界面上显示(测试合格的数值显示蓝色,不合格的显示红色);
• 通过RS485通道1根据扫描获得的条码进行被测模块地址设置;
• 通过RS485通道1进行被测模块初始化,根据方案设置可选;
• 通过RS485通道1进行通讯要求项目测试,根据方案设置可选;
• 通过RS485通道2进行通讯要求项目测试,根据方案设置可选;
• 通过红外通道进行通讯要求项目测试,根据方案设置可选。
3.3.7 人工检测
某些项目无法通过本装置自动化检测,比如指示灯颜色错、液晶脏、按键不灵等,需通过人工操作目测,然后将测试结果在人工检测栏目上勾选出对应的不合格项目,系统自动记录并作为模块判定不合格的依据。
3.3.8 断电检测
当自动化检测流程项目检测完成后,断电按钮会闪烁,如果人工检测项目已经测试完成,那么可点击断电按钮进入停抄电池工作电流检测。
3.3.9 停止检测
在测试结果栏显示出合格或不合格,停止检测按钮会闪烁,可点击停止检测按钮,系统自动输出测试结果并将测试结果上传给ERP系统,如ERP系统连接断开则将测试结果保存在本地数据库中,同时清空4个表位的测试记录。如在5秒(根据方案可设)内操作人员不点击停止检测按钮,系统自动点击停止检测按钮。
3.3.10 气动解压
解除模块压接,气动操作,软件处于等待阶段。
3.3.11 人工下表
结束一组模块测试,手动拆卸已测模块,软件处于等待阶段。
3.3.12 检测下一组模块
重复人工上表、条码扫描开始的步骤,检测下一组被测模块。
4 结束语
采用基于ADAM模块设计的SMT模块自动检测装置,极大的提高了SMT模块检测的自动化水平,检测性能可以很好的满足生产工艺要求,可靠性令人满意。同时也极大的减轻了以往手动检测时操作工的负担,提高了检测效率,生产线单条产能将近提高50%,获得了比较好的经济效益。通过ERP系统实现多工段实时共享检测信息,增强了检测质量的管控以及对加工故障的统计分析,为模块维修提供了较为清晰的故障原因方便维修。
作者简介
朱信洪(1973-),男, 浙江义乌人,工程师,大学本科,主要从事PC机软件、嵌入式软件以及智能仪表的开发与设计。 |