引言
当前汽车冲压件制造行业采用机器人代替人工搬运的应用已逐步普及,并且其需求量呈上升趋势。国内冲压自动化行业从90年代末发展至今,机器人冲压自动化生产线凭借柔性、性价比高等优势在国内冲压自动化领域占据了很大部分的比例。可以预见,随着汽车产能的不断提升,未来具备高性价比、高柔性的机器人快速冲压自动化生产线将在各大冲压件零部件厂商内占据重要地位。同时,进一步改善并发展以机器人为搬运平台的柔性冲压自动化生产线,并且在此基础上提高生产输出节拍、优化布局、减少占地面积将成为一个重要发展方向。
本文通过对传统典型机器人冲压自动化生产线各个关键工艺环节的分析,来进一步研究探讨方案改善方向;通过采用FANUC高性能冲压自动化设备来提高生产节拍,优化方案配置实现6000mm以下压机间距的自动化设备布局,从而协助客户节约场地面积,提升单位面积产出比。
存在问题
国内采用传统6 轴机器人为搬运平台的冲压自动化生产线,压机间距通常大于6500mm,一般为6500~8000mm,其侧围件通常最高节拍为7~8spm,中小型零件通常最高生产节拍为8~10spm,通过分析得知其主要影响生产线布局及输出节拍的因素在于拆垛、对中以及压机间搬运等环节。
(1)拆垛环节
传统机器人拆垛布局方案中,拆垛机器人J1轴作循环往复旋转运动,搬运中小型零件如顶盖及引擎罩等零件时,拆垛节拍最高可达10spm左右,当零件重量提高,由于搬运轨迹以及惯量等诸多因素的限制,导致运行周期时间增长。以侧围件为例,按传统拆垛搬运方案,其拆垛搬运节拍较顶盖、引擎罩等零件慢20%左右,因此按此种拆垛方案配置,拆垛节拍提升存在瓶颈。
(2)对中上料环节
目前冲压自动化生产线对中方式主要有重力对中、机械拍打对中以及视觉对中。随着机器视觉的发展,视觉对中凭借其简洁的硬件配置以及对各种板料的柔性适应能力,目前在机器人冲压自动化线上配置普遍,但其存在视觉识别和机器人姿态调整的延时。同时在生产一机双模类对称板料时,机器人需要进行两次拾取动作,其搬运节拍将受到进一步的限制。
(3)压机间搬运环节
当前以机器人为搬运平台的冲压自动化生产线,压机间搬运方式主要有机器人6轴旋转搬运、机器人附加平行连杆机构搬运以及机器人附加旋转7轴搬运。采用以上搬运方式,由于机器人运行空间需求,通常压机间距至少需要6500mm以上。
【线首拆垛方案分析】
1 常规拆垛区域布局(如图1所示)

图1 常规拆垛区域布局
传统机器人拆垛区域,拆垛台车呈平行布局,机器人搬运轨迹为J1轴关节作±90度旋转往复运动,当搬运中小型板料时,其生产节拍最高可达10spm左右,但当生产侧围板料时,按此常规布局,预计最高节拍只能达到约8~9spm。分析原因,主要归纳有以下几方面:
(1)机器人主要作旋转运动,运行轨迹距离长;
(2)侧围料片间油膜粘连导致机器人Z方向提取时候受到负压影响;
(3)板料表面积大,机器人拆垛快速提升时,加速度越大受到空气阻力随之增大;
(4)随着板料被不断拾取,料垛高度随之下降,机器人在Z方向上的运行距离也逐渐增大,增加运行时间;
(5)一般手腕负载为100kg级的6关节机器人J1轴最高转动速度通常为90度/秒~110度/秒左右,在拆垛运行过程中,J1轴为主导轴,当机器人搬运重量较大的侧围板料时,因惯性增大,导致J1轴马达加减速时间增长,影响输出节拍。
2 改善布局讨论
2.1 优化布局,减少机器人运行距离
2.1.1 传统拆垛区域布局:机器人J1轴关节作循环旋转±90度运动(如图2所示)。
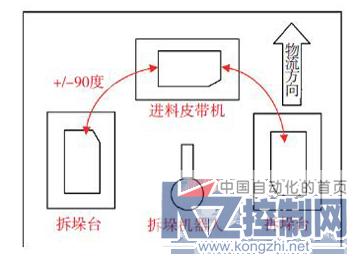
图2 传统拆垛区域布局
2.1.2 改善布局:机器人作循环直线运动(如图3所示),减少机器人运行距离。
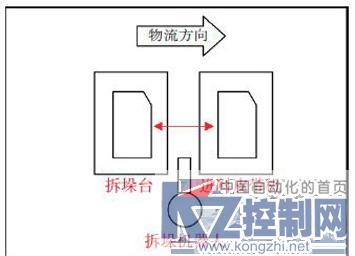
图3 机器人作循环直线运动
2.2 结合以上优化布局,根据机器人特性,选择性能匹配最佳的机器人型号
目前行业内负载100kg级6轴关节机器人J1轴最高转动速度通常为90度/秒~110度/秒左右,直线运行速度通常为2000mm/s左右,鉴于改善后布局,机器人运行轨迹为直线,因此方案选择FANUC M-900iA/150P作为拆垛机型,其手腕负载为150kg,工作半径为3500mm;关键其加速性能优良,直线运行速度达4000mm/s,因此能很好地匹配改善后布局中高速循环的直线往复运动。
2.3 减少机器人在料垛侧拾取时Z方向的运行距离
传统拆垛机器人运行时,通过其程序控制来调整板料拾取点位置,机器人拾取一张板料,机器人自动往下运行一片料厚的距离,依次循环往复。这种通过软件实现板料拾取位置调整的方法能满足实际生产的需求,但随着料片被不断拾取,料垛高度随之不断降低,机器人在Z方向上的运行距离也逐渐增加,这直接导致机器人运行周期时间增长。
为缩短拆垛机器人在Z方向上的无效运行时间,本方案采用自动顶升机构,随着料片被不断拾取,自动顶升机构自动将料垛顶升至既定的板料拾取高度位置,确保料垛上表面板料始终与进料皮带机基本保持同一平面上。这样,机器人的板料拾取点始终被固定在一个稳定的高度上,这也意味着其在Z方向上的运行距离始终是最小的。与传统方案相比,采用料垛自动顶升功能的方案节省了机器人在拆垛工程中Z方向上的无效运行时间。
3 小结
根据以上若干重点环节的改善,以及通过FANUC Roboguide模拟仿真软件进行理论节拍分析,最终形成优化后的机器人拆垛技术方案。
以上布局的方案,使机器人运行距离降到最短,其趋于直线的运行轨迹有效利用并发挥了M-900iA/150P机器人高直线运行速度的优势,避免了板料惯量对搬运产生的阻碍。同时料垛自动顶升机构的配备,有效缩短了机器人在拆垛过程中Z方向上的无效运行时间,最大程度的降低了高速提升运动时气压阻力造成的不利影响;通过FANUC Roboguide仿真推定,生产效率较传统配置方案能提升约30%。
【对中上料区方案分析】
1 常规方案分析
常规机械拍打对中因其结构复杂,且后期维护保养不易,目前逐步被视觉对中所取代;相比前者,视觉对中具有柔性化程度高,周边硬件配置简单,后期维护保养容易等优点,目前已广泛应用于冲压自动化生产线上;对于单片板料对中定位,其柔性适应的优势突出明显。但同样也存在不足之处,其每个工作循环均需损耗0.5~1s的视觉识别和机器人姿态调整时间,生产线受到每分钟1~2件的产能制约;同时,在生产一机双模的双片板料时,若采用视觉对中,则机器人须分两次拾取板料,虽能实现生产功能,但较一次拾取板料至少还要多花费1s左右的运行时间,生产线预计将受到每分钟1~2件产能的损失。
2 方案优化讨论
针对以上常规视觉对中的功能不足,本方案在原有视觉对中系统的基础上做了改良优化,最终目标是确保在上料机器人拾取板料前,板料须处于能从既定位置被直接搬运拾取的就绪状态,这就需要三套系统能进行协同工作。第一,视觉识别系统完成板料的偏差识别,并将偏差数据传送至对中系统;第二,对中系统根据识别系统获得的偏差数据执行并完成板料的位置补偿调整;第三,机器人快速拾取并将板料送入第一工序模具。这样,上料机器人只需将板料从对中台以最快的速度搬运至第一工序模具,从而简化了上料机器人的搬运程序,同时也避免了原先方案中的视觉识别等待时间以及上料机器人姿态调整时间。
2.1 偏差识别系统
本方案板料偏差识别系统采用FANUC iRVision视觉系统,该系统最大优势在于精度可达1.5mm/pixel,工作范围能达到4000mm×2000mm,基本能覆盖并满足所有车身冲压板料的视觉对中需求;同时区别于其他第三方视觉系统,FANUC iRVision视觉系统能与FANUC上料机器人无缝对接,同时硬件配置相当精简,通过机器人TP示教器即能完成整套视觉系统的标定和配置。
2.2 对中系统
为了确保上料机器人能快速直接地完成上料工作,要求料片必须在上料机器人取料前完成板料的对中调整;本方案采用两台FANUC平行连杆机器人实现料片的对中调整,此种配置的优势在于:第一,能为整套上料工艺环节节省0.5~2s的周期运行时间;第二,其伺服柔性调整功能可以满足各种不同形状板料的对中调整,较机械拍打对中有更广泛的适应性;第三,此种对中机器人作为成熟标准设备导入生产线,简化了系统配置,有利于后期维护保养工作。
2.3 上料机器人系统
类似于拆垛机器人,上料机器人运行轨迹同样是循环往复的直线运动,因此机器人选型同样采用FANUC高性能冲压专用搬运机器人M-900iA/150P,通过FANUC Roboguide动态仿真软件分析,推定其能很好地匹配优化后视觉系统,并完成高速直线往复上下料运动。
3 小结
通过采用FANUC iRVision视觉系统以及伺服对中机器人,使整套上料自动化系统更加柔性,能满足各种形状单片板料及一机双模双片板料的识别定位;并有效解决了常规视觉对中过程中视觉识别和机器人姿态调整造成的时间延时;同时视觉识别、板料对中以及机器人上料等各工艺环节,环环紧扣,衔接更加紧凑;根据生产板料不同,较传统视觉对中方案能节约0.5~2s的周期运行时间。
【压机间方案分析】
1 现状分析
目前各大冲压件制造厂商纷纷都在努力提高单位面积产出比,冲压线的压机间距规划愈加紧凑,如德国SCHULER配备其Crossbar Feeder的机械压力机自动化生产线,其压机间距压缩到了5200mm,其紧凑程度相当于在国内常规5台压机所占面积内布置了6台压机。
采用传统6轴机器人旋转搬运方式或旋转7轴搬运中小型零件时,通常要求的压机间距为6500mm以上;但当生产零件为车身侧围或一机双模零件时,其间距要求更大;同时为了避免与压机立柱和模具导向斜楔等机构的干涉,机器人轨迹较为复杂,这同样也影响了输出节拍。
需要解决的问题主要有以下几方面:第一,避免因复杂轨迹导致的输出节拍下降;第二,目标6000mm以下的压机间距布置;第三,实现正面上下料,避免机器人在工作过程中与压机立柱和模具发生干涉;第四,简化机器人运行轨迹,使机器人以最短最快的路径达成最高生产节拍。
2 专用设备导入应用
本方案根据压机间一系列搬运工艺要求和特点,采用上海发那科冲压直线搬运机器人,利用其手腕部直线倍速机构的运行原理,实现零件在压机间高速直线的搬运。
3 小结
通过有效利用冲压直线搬运机器人的运动特性,提高了压机间零件的整体传输效率,运行轨迹趋于直线,避免了与周边设备的干涉,同时利用FANUC Roboguide软件最优位置计算功能,本方案最终优化达成了5600mm的压机间距布置。据仿真分析测算,按搬运零件不同,其生产输出节拍较传统方案提升3~4spm。
结语
通过对冲压自动化生产线各个关键工艺环节特点的优化和分析,采用FANUC一系列高性能自动化设备,使生产节拍得到有效提升,压机间距缩小优化至5600mm,同时因本方案基于FANUC标准成熟机器人搬运平台,整线配置投入较目前国外昂贵的专机搬运生产线,更能满足国内广大冲压件零部件厂商对冲压自动化生产线的需求。
摘自《自动化博览》2月刊
|