关键词:磨煤机制粉系统自动控制;模糊控制;分散控制系统
1 概述
作为制粉设备的钢球磨煤机广泛应用于国内外火力发电厂中,但使用中由于存在多变量耦合、多变量时滞和模型时变的特性,造成了磨煤机无法实现自动控制,不能在最佳经济工况下出力。
镇海发电有限责任公司4×200MW机组制粉系统为中间储仓制粉,热风送粉,配2台DTM380/720钢球磨。同样由于多变量强耦合和磨煤机内载煤量难以检测,无法投入自动,使磨煤机单耗高、制粉效率低。99年利用机组自动化改造的机会,对磨煤机控制系统进行改造,采用模糊控制技术,在北京和利时系统工程股份公司生产的HS2000 DCS系统SENT网上挂接计算站的方法,把模糊控制算法嵌入DCS系统中,以达到数据共享、集中管理,实现了磨煤机模糊控制在DCS系统中的应用,突破了以前的磨煤机模糊控制只能作为一个独立系统来实现的局限性,为磨煤机模糊控制的推广应用又开辟了新的途径。
2 模糊控制系统的设计
2.1 模糊控制系统
所谓模糊控制,就是在控制方法上应用模糊集理论及模糊逻辑推理的知识来模拟人的模糊逻辑思维方法,用计算机实现与操作者相同的控制。要设计一个模糊控制器以实现语言控制,必须经过以下三步:
(1) 精确量的模糊化
它是把语言变量的语言值转化为某适当区域上的模糊子集。设误差的基本论域为[-e,e],误差所取的模糊集合的论域为X={-n,-n+1,…,0,…n-1,n},这时需要通过量化因子进行论域变换,误差e的量化因子ke的定义如式(1)所示。

一旦量化因子选定后,系统的任何误差e总可以量化为论域X上的某一个元素。从上式可以看出,一旦给定论域X,量化因子ke的取值大小可使基本论域[-e,e]发生不同程度的缩小和放大,即当ke大时,基本论域缩小,反之基本论域放大,从而提高了误差控制的灵敏度。
同样,对于误差变化的基本论域[-ec,ec],若选定量化n档论域Y,则误差变化ec的量化因子Kec定义如式(2)所示。

对于系统控制量的变化u,基于量化因子的概念,比例因子如式(3)所示。

(2) 模糊推理算法
它是通过一组模糊条件语句构成模糊控制规则,并计算模糊控制规则决定的模糊关系。模糊控制规则的一般形式为:
如果E是Ei,EC是ECj,那么U是Uij(i=1,2…,m1,j=1,2, …,m2)。
这里Ei、ECj、Uij是模糊子集;E表示被控量的设定值R对其实际值Y的偏差e=R-Y所对应的模糊子集,EC用来表示偏差变化的模糊子集,U表示输出控制量的模糊子集,m1是E的模糊子集划分数目,m2是EC的模糊关系R,即:
R=[Ei* ECj]*Uj
式中符号“*”表示Cartesian积。
根据模糊推理合成规则,输出的控制量应当是模糊子集U:
U=(E* EC)T。R
式中符号“。”表示模糊合成运算。
这样,若已知输入量E、EC和输出控制量U,就可以根据上述规则把相应的模糊关系R求出来;反之,若系统的模糊关系R为已知时,就可以根据E和EC求出模糊控制量U。
(3) 输出信息的模糊判决
它完成由模糊量到精确量的转化。模糊控制器的输出是一个模糊子集,但被控对象只能接受精确的控制量,因此需要解决将模糊量转化为精确量的问题。方法很多:如最大隶属度法、取中位数法等,下面介绍一下隶属度加权平均法。
设模糊集U=[μF(u1)/U1, μF(u2)/U2,…,μF (un)/Un],则控制量U由下式决定:
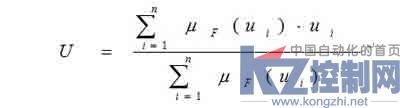
在实际控制系统中,并不需要把一个关系矩阵存入计算机,然后再实时计算控制作用,而只要离线算出卡式积E*EC上每一点的控制作用,列成表格形式,称它为Fuzzy控制查询表存入计算机,进行查询控制。这种方法即节省主机的工作时间,又节省内存。
2.2 多变量模糊解耦控制
磨煤机制粉系统多输入与多输出变量之间耦合程度比较强,必须采用多变量控制策略。对于多变量被控过程,如果采用模糊控制,即模糊集合表达的控制规则,则其表达形式与单变量系统的模糊控制基本相同,所不同的是多变量控制规则更难提取;同时,由于多变量系统变量增多,用于表达多变量控制规则的计算机存储容量增大。为此,在算法中设计了解耦补偿器,通过改变耦合因子,使耦合对象变成一个耦合程度极其轻微的控制对象,系统才能投入正常运行。
3 磨煤机模糊控制系统的基本原理
磨煤机运行调节的目的是在保证磨煤机安全运行的情况下,使磨出力达到最大,处于最佳经济工况。其基本原理图如图1所示。
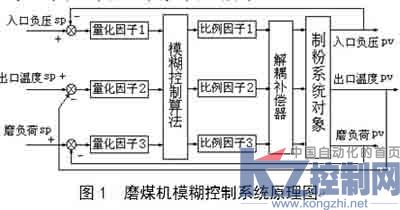
3.1 磨再循环风调节
一般说来,入口负压是由再循环风量调节的,但再循环风量的变化直接影响锅炉燃烧,故采用热风量作为辅助调节,若再循环风量已经超出一定的范围而负压仍达不到要求,则使用热风参与调节,再循环风量限制范围可根据不同磨煤机的具体情况由运行人员设定。使负压值尽量小,以最大限度地减少漏风量,应充分利用热风,提高磨出力。
3.2 磨出口温度调节
出口温度不但与热风、冷风量有关,而且与磨内存煤量有关。当存煤量多时,改变热风量,出口温度变化很慢;反之,变化很快。磨正常运行时,出口温度变化很慢,增减热风量可保持出口温度在一定范围内。在异常情况下,如断煤、满煤,则出口温度变化很快,需要在异常调节算法中处理。
3.3 磨负荷调节
因磨出入口差压受风量及其它一些因素的影响很大,不能够很准确的反映磨内存煤量,故采用磨前轴的振动能量信号和磨出/入口差压信号相结合来判断磨负荷的方法。在入口负压和出口温度都正常时,尽量加大给煤量,寻找最佳经济工作点。
4 系统构成
DCS采用HS2000分散控制系统,磨煤机模糊控制系统作为计算站挂接在HS2000的SNET上。系统组态、参数调整在工程师站上完成,监视画面、操作画面和参数显示在操作站上完成,不另设CRT,与DCS实现信息共享。系统结构图如图2所示。
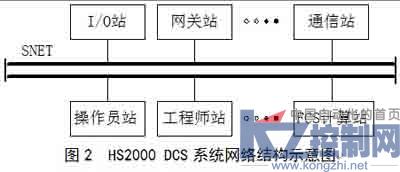
4.1 硬件组成
磨煤机模糊控制系统采用一台工控机作为计算站,同时对甲、乙两台磨进行控制。
为完成模糊控制与HS2000 DCS系统的数据发送、接收任务,采用系统网卡(型号HS2P31)和相应的电缆进行连接。
为解决磨煤机内载煤量难以检测的难题,采用了新型的LT—420负荷变送器和负荷传感器;在不同的负荷下,钢球、筒壁和煤之间碰撞的强度与几率不同,形成了不同的噪声频谱,来测定负荷。
4.2 软件组成
软件部分包括通讯接口软件和模糊控制系统计算软件。
通讯接口软件中包括该公司提供的访问数据库所需的头文件(.h)和库文件(.lib)及C语言编写的数据交换软件。用Write和Read函数直接对DCS的数据库进行访问,简单、快速,有效利用了DCS的网上资源,实现了信息共享。
模糊控制系统软件是实时控制程序,能完成磨煤机的整个控制过程。当系统处于手动状态时,控制器输出指令跟踪阀位信号,能实现系统的手动与自动的无扰切换;当系统处于自动状态时,通过模糊控制算法,输出相应的控制指令,使球磨机安全稳定地运行,防止事故的发生,并保持磨煤机的最大出力。
5 系统特点
(1) 各参数采样准确、快速,抗干扰能力强;各控制回路可全部投入自动或单独投入自动,并实现手/自动的无扰切换,自动投入率达100%。
(2) 利用HS2000 DCS组态功能可完成:实时流程图显示、操作器画面显示、实时趋势画面显示、历史趋势画面显示、统计报表、报表打印等。
(3) 利用HS2P31系统网卡和通讯接口软件,高效完成数据传输、资源共享。
(4) 负荷传感器和新型负荷变送器来测量磨煤机内存煤量,测量准确、灵敏。
(5) 能保持磨煤机出口温度、入口负压及磨煤机优化运行工况,使制粉系统能安全、经济运行,有效地防止了球磨机满煤、跑粉等事故的发生。
6 结论
运行实践证明,这种模糊控制系统对于磨煤机制粉系统这类复杂系统的控制是可行的。它不但保障了运行的安全,提高了经济效益,而且解决了制粉系统长期不能投入自动控制的难题。磨煤机进口负压能控制在-1200kPa±200kPa,出口温度控制在72℃±2℃,制粉系统单耗由平均28.5kWh/t煤,下降至平均26.5kWh/t煤,节能达7%,经济效益非常显著。
因此,磨煤机模糊控制技术的成功应用,不但提高了国产200MW火力发电机组自动化水平,降低了厂用电,而且为机组DCS的应用提高到了一个新的台阶。
|