郑志强 1 项目简介 自二十世纪九十年代以来,火力发电厂广泛采用分散控制系统(DCS),使其成为机组安全、经济运行不可缺少的重要组成部分。但随着单机容量的不断增大,电厂现代化管理要求的日益迫切和计算机技术的不断发展,火力发电厂厂级自动化系统开始在电厂中得到应用。厂级自动化系统可分为厂级监控信息系统(SIS)和管理信息系统(MIS)。MIS用于完成电厂内部的日常管理工作,以及与上级部门的信息交换;SIS则用于厂级生产过程的自动化,它的下级控制系统包括DCS和辅助车间自控系统,选择合理的辅助车间自控系统既可以减轻DCS的负担、提高机组的综合自动化水平,又可降低工程造价。但是,什么样的辅助车间自控系统才叫合理,这是当前自控领域急需研究的重点课题之一。 在此形势下,广东省电力设计研究院与汕头经济特区电器仪表成套厂合作,设计开发出本套基于现场总线技术的PLC,并将其应用于韶关电厂#10机组锅炉除灰除渣系统的控制。 2 工艺系统控制要求 韶关电厂#10机组锅炉除灰除渣系统控制对象较多,工艺逻辑控制要求也比较复杂,它包括四个子系统。 (1) 电除尘器除灰系统
韶关项目电除尘器为双通道四电场,共有32个灰斗。每个灰斗下方设置闸板门、三通门、锁气器各一个。控制要求为:当灰斗灰位高或上位机要求程序启动时,启动锁气器→开三通门→开闸板门;当灰斗灰位低或上位机要求程序停止时,关闸板门→关三通门→停止锁气器。 (2) 炉底除渣和尾部烟道除灰系统 炉底除渣装置控制顺序为:开渣斗激流喷嘴→开碎渣机→开排渣门→排渣15~30分钟后关排渣门→关碎渣机→渣斗水位正常后再关激流喷嘴。 尾部烟道除灰系统的每个灰斗设有闸板门和锁气器,其控制要求为:当灰斗灰位高或上位机要求程序启动时,启动锁气器→开闸板门;当灰斗灰位低或上位机要求程序停止时,关闸板门→停止锁气器。 (3) 灰渣泵系统 此部分控制比较复杂,因灰渣泵共有5台,灰渣输送管却只有3根,因此需要装设很多阀门实施管间切换。本设计以灰渣管的运行方式来决定灰渣泵的运行状态。#1灰渣管上运行#1~3灰渣泵,#2灰渣管上运行#2~4灰渣泵,#3灰渣管上运行#3~5灰渣泵。控制逻辑为:根据选定的灰渣管和灰渣泵,先开泵前的灰渣阀,到位后启动泵,然后打开泵出口的各个灰渣阀。 (4) 冲洗、冲灰水泵系统 ① 轴封水泵,逻辑控制要求为:先开泵入口阀门,接着启动泵,泵启动后开泵出口阀门。关的顺序与开的顺序相反。两台泵互为备用,工作泵故障或泵出口母管压力低时,备用泵及相应阀门自动投入。 ② 冲洗水泵,逻辑控制要求与轴封水泵基本相同。 ③ 冲灰水泵,逻辑控制要求与冲洗水泵相同。 3 控制系统硬件配置说明 本系统按2×300MW机组容量设计,采用冗余配置,系统内任一模块故障,均不会影响整个系统的工作。自诊断功能可诊断至模块级,因此系统具有高度的可靠性。控制系统的硬件配置方案见图1。它由上位机(工业监控计算机)、双机热备Q系列PLC和远程工作站组成。上位机与Q系列PLC组成工业以太网络,Q系列PLC与远程工作站的信息通讯是通过CC-Link现场总线进行双向传递。
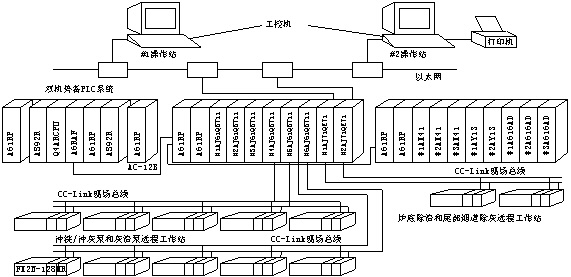 图1 除灰渣控制系统硬件配置图
3.1 上位机 上位机是人机界面的基本硬件平台,其性能及品质的好坏直接关系到整个系统的可靠性。本系统上位机冗余配置2台台湾研华610型计算机,CPU主频PII 300,内存128MB,美国3COM公司的10M以太网卡。CRT为PHILIPS的21寸彩色显示器,同时配置一台HP4L型激光打印机,实现对整个系统的监控、报警、报表打印和事故分析。 3.2 双机热备的Q系列PLC 这是本控制系统的一个重要组成部分,负责冲洗冲灰子系统的逻辑和联锁控制、部分模拟量输入和输出、通讯总线和CPU的切换等。 (1) 主基板 系统采用的A32RB主基板,是冗余电源双CPU配置用基板。板上插有下列模块: ① 电源模块A61RP,给主基板供电,主基板再为CPU和其它模块提供5VDC电源。模块额定电流为8A,输入电压为220VAC。 ② CPU模块Q4ARCPU,内置128KB的RAM存储器。 ③ 系统控制模块AS92R,用于监视:1)CPU的自诊断结果;2)CPU的操作监视器;3)AS92R的自监视器;4)5VDC电源电压;5)24VDC电源电压;6)电源模块故障。当发现其中任何故障时,AS92R提供信号给总线切换模块,使之实施系统切换,并给出相应的系统报警信号。 ④ 总线切换模块A6RAF,负责切换总线。运行状态下其面板设置一般为:A站为主控站,B站为热备状态。 (2) 扩展基板 扩展基板采用A68RB型冗余电源基板,通过AC12B扩展电缆与主基板连接,扩展基板上插有下列模块: ① 电源模块A61RP。 ② CC-Link通讯模块AJ61QBT11。 ③ 以太网通讯模块AJ71QE71,支持TCP/IP或UDP/IP协议,可选择固定的缓冲器、随机的缓冲器和PLC服务三种通讯方式。传输速率为10Mbps,传送的最远距离为2500m。 ④ 模拟量输入模块A616AD,可接收-10V~+10V电压信号或4~20mA电流信号。隔离方式是输入端子与内部电路之间光电隔离,但通道间不隔离。 ⑤ 开关量输入模块AX41,可接受32个信号。输入回路与内部电路间采用光电隔离,各输入回路均有LED显示灯。 ⑥ 开关量输出模块AY13,可输出32个信号。同样采用光电隔离,输出点容量2A。 ⑦ 温度输入模块A68RD3,可接三线制Pt100测温传感器。温度输入范围为-180℃~+600℃,分辨率0.025℃,输出可用16位或32位二进制数表示。 3.3 远程工作站 远程工作站是在常规的低压开关柜上增设智能控制装置,智能控制装置与开关柜之间的接口设计和制作是本控制系统研制的重点内容之一。 远程工作站(共12台)就地安装在被控对象附近,担负着各泵、阀门、锁气器等的数据采集、顺序控制和联锁保护等功能。 远程工作站内的智能控制装置选用FX2N-128MR,它是超小型、多功能的可编程装置,其主要功能和性能为: ① 数据采集和处理 输入64点,接收无源触点信号,查询电压24VDC。输出64点,外接交流负载,工作电压220VAC。输入输出均有状态指示灯。 ② 顺序和逻辑控制 可独立编程处理各个I/O信号,程序容量8K,可扩展至16K,指令运算速度0.08μs / 基本指令。 ③ 通讯速率 可选300bps~19600bps。 ④ 通信协议 可选RS232C/422/485、CC-Link或按IEC61158现场总线标准。本系统采用冗余CC-Link现场总线,通讯模块为FX2N-32CCL,共2块,24VDC电源。 ⑤ 自诊断 CPU或程序出错时由LED灯显示,可通过查看特殊数据寄存器来查询错误信息。 3.4 以太网 上位机和Q系列PLC的通信采用10Base5标准以太网络,总线型拓扑结构。网络硬件有50Ω粗同轴电缆,外部收发器,以太网卡。网络有4个站,包括2台PC,2台PLC,各站通过IP地址区分。 PC1的IP地址:192.0.1.11; PC2的IP地址:192.0.1.10; PLC1的IP地址:192.0.1.1(主PLC); PLC2的IP地址:192.0.1.2(备PLC)。 正常情况下,PC1和PC2均可监控双机热备的PLC。如PLC1出现故障,由总线切换模块将PLC2切换为工作主站。 3.5 CC-Link现场总线 CC-Link网络由主站、从站和通信网线构成。主站是Q4ARCPU,从站包括远程数字量I/O、远程模拟量I/O、远程高速计数器等。主、从站需设置站号、传输速率、占用站数等。主站与从站的通信由两块主/从通讯模块完成,主站靠站址辨识从站,即每个从站都有一个不同的站号,主站发送的信息,只有相应站号的从站才能响应。 CC-Link技术规范参见表1。 本系统中,Q系列PLC与远程工作站GCR(Z)柜间的CC-Link网络通讯采用冗余技术:① AJ61QBT11通讯模块,共6块,每个子系统各有2块,一工作一备用。正常情况时,通讯模块1采集现场信号,收发信息,如有故障切换到备用通讯模块。② FX2N-32CCL通讯模块的设置与对应的主通讯模块连接有关。 冗余总线上对应同一远程工作站,有2块开关设置相同的通讯模块FX2N-32CCL,一工作一备用。总线上的通讯模块站号依次为:01,05,09,13,17。模块的通信速率,按不同子系统的距离远近,设置成与对应的主通讯模块的速率相同。 CC-Link网络中所有站均要编程初始化,才能使网络正常工作。
表1
项目 |
规范 |
控制规格 |
最大链接点数 |
远程输入/输出(RX,RY):2048点
远程寄存器(RWw):256点(主站-远程/从站)
远程寄存器(RWr):256点(远程/从站-主站) |
每站的链接点数 |
远程输入/输出(RX,RY):32点(在一个从站中为30点)
远程寄存器(RWw):4点(主站-远程/从站)
远程寄存器(RWr):4点(远站/从站-主站) |
最大占用的站数 |
4站(最大输入/输出点数为128点,链接寄存器:32点) |
瞬间传送 |
最大1024个字节/站 |
性能 |
链接的扫描时间(10Mbps) |
3.9ms(远程输入/输出2048点)
6.7ms(远程输入/输出2048点,远程寄存器512点) |
通信规范 |
通信速度 |
10M/5M/2.5M/625K/156Kbps |
通信方式 |
广播投票方式 |
同步系统 |
帧同步系统 |
代码 |
NRZI |
传送通道 |
总线系统(遵照EIA RS485标准) |
传送格式 |
根据HDLC |
出错的控制系统 |
CRC(X16+X12+X5+1) |
可连接的模块数 |
(1H a)+(2H b)+(3H c)+(4H d)≤64站
a:占用1站的模块数,b:占用2站的模块数,c:占用3站的模块数,d:占用4站的模块数
16H A+54H B+88H C≤2304
A:远程I/O站模块数 最多64个模块
B:远程设备站模块数 最多42个模块
C:从站/智能设备站模块数 多26个模块 |
RAS功能 |
自动复线功能、从站切断功能、检查数据连接状态、离线测试(硬件测试、环路测试、参数校验测试)、后备主站 |
4 软件开发 4.1 PLC软件编制 本系统PLC控制部分采用三菱公司的GPPW编程软件,它提供指令表、梯形图和顺序功能图三种编程方法。 指令表是最原始的编程方式,它是将控制指令按顺序逐个排列,生成文本程序文件,因其编制方法落后,本项目没有用来直接编程,只是在程序检查时偶尔用之。梯形图编程是当前工业上应用最为广泛的PLC编程方法,其最大的特点是类似工业控制电气图的继电器逻辑,容易被习惯于看电气图的工程技术人员看懂,本系统的PLC控制编程正是使用这一编程方法。顺序功能图则将控制过程分成多个步序和传送,一步序代表一个具体操作或功能子程序,一个传送代表从一个执行步序过渡到另一个执行步序的传送条件,此种编程方式比较适应于查找故障点。 本系统编程的基本流程是:根据已经确定的工艺系统控制要求→画出流程图→标注各信息流之间的关系→安排输入、输出的配置→对输入、输出进行地址编号→画出信号端子和现场信号联络图表。控制程序的设计采用的是所谓的逻辑设计法,即根据生产过程中各检测元件(如行程开关,力矩开关等)状态的不同组合和变化,确定所应满足的中间环节,再按各执行元件的工作要求,用触点的串并联组合在电路上实现逻辑表达式,最终形成程序文件。 4.2 上位软件编制 本系统2台上位监控机的监控软件选用了当今市场上较为流行的美国Intellution公司的iFIX,它与PLC的数据交换如下述: 4.2.1 数据流向及过程数据库 iFIX实施监控所需的数据和相关信息取自于下层的PLC,PLC可供iFIX读取的数据源包含数据块变量、I/O地址、对象属性、历史数据、画面属性、VBA事件、全局变量和表达式。iFIX数据库与数据源的连接是通过I/O Driver来实现的(I/O Driver不从属于iFIX,需要另外安装),iFIX读取内部数据库的数据并将数据传送到应用程序的过程,则由驱动器映象表(DIT)和扫描、报警、控制程序(SAC)完成,无需操作干预。数据流向为: Process→PLC→I/O Driver→DIT→SAC→PDB→View iFIX的过程数据库由块和链组成。块是由iFIX提供的执行一定功能的指令集合,链是连接各个功能块的逻辑关系,块与链的合理搭配即形成所谓的逻辑块链,一系列逻辑块链连接在一起便生成一个控制或监视回路。块分两类:① 基本块 (Primary blocks) 逻辑块链的起点,一般用于处理数据库的输入或输出,如AI、AO、DI、DO等块;② 二级块 (Secondary block) 从前继块获取数据并执行某种类型动作或计算,如计算块CA。 例如:在灰渣泵房控制中,#1泵处于运行状态,#2泵被选为备用泵,当#1泵跳闸,#2泵自动启动时,其控制策略需要设置以下逻辑块链: #1泵跳闸信号处理块DI→跳闸/自起动控制计算块CA→输出#2泵启动信号处理块DO 4.2.2 报警处理 iFIX提供了一套功能完善的报警生成程序,它可通过设定报警区及报警区路径,将某一参数值超过预先设定值的基本块的报警状态传送至相应的报警汇总表或报警显示窗口。 在本项目的报警包括压力、温度、物位、电流、设备故障等。 4.2.3 数据安全设置 为了保护数据库不受未授权的写操作,iFIX提供了安全保护区,它可以将数据库内的数据块按安全级别分类存储。不同操作权限的人员只能对相应级别数据区写操作。本系统的上位机设置三个权限:① 操作员:只能在WorkSpace运行状态下操作;② 工程师:能进入WorkSpace组态模式编辑文件;③ 系统管理员:享受本系统的最高权限。 对数据安全的设置称为安全组态,这些工作在安全组态程序中进行,包括:① 允许/禁止安全系统;② 生成和编辑用户及组帐号;③ 建立启动时的自动登录;④ 定义用户使用程序功能的权限;⑤ 定义用户名和口令;⑥ 定义安全区名。 5 调试 所有的PLC控制程序和上位机操作画面编制完成后,系统曾在制造厂进行模拟调试,方法是用小型开关模拟远程工作站的输入,将远程工作站的输出接至显示灯泡,短接所需输入(即开关合上),观察程序的输出是否响应(即是灯泡亮否)以判断程序的正确性。调试时对所有被控对象的单操和程序控制分别进行试验。 装置在韶关电厂安装完成后又进行一次现场调试,期间曾根据现场条件的变化作过程序修改。 6 投运 经过近一年的设计、组态、编程和调试,系统于2000年7月装配完毕,同月交付韶关电厂工地施工,2000年9月,由广东省电力设计研究院、广东省试验研究所、广东省工程监理公司、汕特仪表成套厂及韶关电厂等单位组成验收小组,对本控制系统进行了验收,随后投入运行。从移交生产至今,控制系统运行正常,使用起来方便、可靠,维护工作极为简单,降低了运行和维护人员的劳动强度。这套控制系统投运至今已稳定运行一年多,电厂反映有以下几点优势: 通过CRT画面直接控制现场设备,操作方便且直观。 一些主要设备的正常启停与事故切换可由程序自动控制,无须人工逐步操作,体现高度自动化。 灰斗排灰由智能远程工作站根据灰斗灰位自成闭环控制,令控制周期缩短,减轻操作员负担。 监控系统具备过程数据的实时更新和存储,查看、打印运行报表方便及时。 采用现场总线技术节省了大量控制电缆,也令系统的安装、检修和维护更加方便。 |