熊伟(1965-) 男,云南文山人,自动化仪表高级工程师,工学学士,(红河学院信息科学与电子工程学院,云南 蒙自 661100),现就职于红河学院信息科学与电子工程学院从事自动化专业教学工作,研究方向为生产过程自动化及计算机控制系统。
摘要:本文介绍了基于PLC与组态软件的自动配料系统的设计与实现,并举例说明。
关键词:PLC;组态软件;配料系统;设计
Abstract: This paper introduces the design and implementation of automatic ingredient system based on PLC and configuration software by an application example.
Key words: PLC; Configuration software; Ingredient system; Design
1 概述
自动配料系统在冶金、建材、化工及食品等行业应用非常广泛,近几年来随着计算机技术和PLC技术的飞速发展,国内外的组态软件不断完善,自动配料系统控制方案也在不断改进,本文着重介绍利用PLC及监控组态软件来实现自动配料系统设计与实现的方法。
由于PLC的迅猛发展,实现了工业控制领域的飞跃,其功能从弱到强,实现了逻辑控制到数字控制的进步;其应用领域从小到大,实现了单体设备简单控制到胜任运动控制、过程控制及集散控制等各种任务的跨越。今天的PLC正在成为工业控制领域的主流控制设备,可以用于各种规模的工业控制场合,在各个领域发挥着越来越大的作用。除了逻辑处理功能以外,近年来PLC的功能单元大量涌现,使PLC从逻辑控制渗透到了生产过程控制、运动控制等各种工业控制中。加上PLC通信能力的增强,使用PLC组成各种控制系统变得非常容易。
监控组态软件是伴随着计算机技术、网络技术的突飞猛进发展起来的,监控组态软件是面向生产过程的监视、控制与数据采集的软件平台工具,具有实时多任务操作,设置项目丰富,使用方便、灵活,功能强大,监控组态软件通用性强,解决了人机图形界面的问题,通过监控组态软件对控制系统进行组态,可以把生产工艺上的参数在流程图上显示出来,处理数据报警和系统报警,存储历史趋势,各类报表的生成和打印输出,在PC机的屏幕上进行整个生产过程的操作,接口开放,方便数据共享,支持多种硬件设备。因此监控组态软件得到了广泛的应用。PLC与监控组态软件的完美组合,通过监控组态软件对PLC及其它智能设备的I/O数据进行监控,应用越来越广泛。
2 设计实例
2.1 工艺介绍
整个配料系统的工艺流程如图1所示。有5种物料分别装在1#~5#料斗中,要求按一定的比例进行自动配料,经过配料后的物料由1#~5#料斗通过1#~5#皮带下到6#皮带上,两台混料机A、B互为备用,只能运行一台。当开动混料机A时混料机B禁止运行,由6#皮带(正向运行)将物料运到6#料斗进入混料机A混合后的物料通过8#料斗进入7#皮带送出;当开动混料机B时混料机A禁止运行,由6#皮带(反向运行)将物料运到7#料斗进入混料机B混合后的物料通过8#料斗进入7#皮带送出。
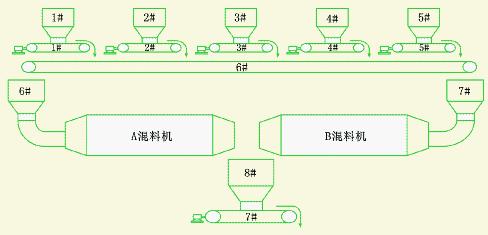
图1 配料系统工艺流程图
2.2 控制要求
(1) 逻辑顺序控制部分
整个配料系统的电气设备启动停止顺序为逆序启动,顺序停车。从流程的最后开始启动运输设备,停车时从开始进料的设备依此顺序停车,具体停车、启动时各台运输设备中间的间隔时间可以在调试时进行确定。
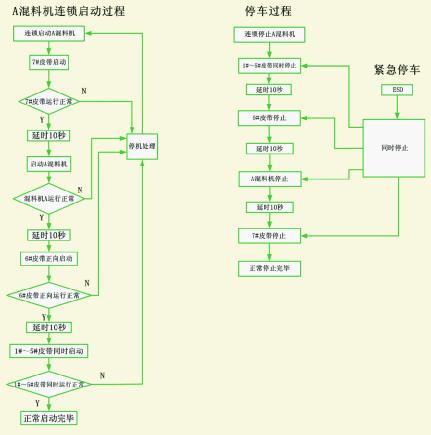
图2 配料系统运输电气设备启动、停止顺控逻辑图
当正常开动混料机A时:7#皮带运行 → 延时10秒 → 混料机A运行 → 延时10秒 → 6 #皮带运行(正向运行)→ 延时10秒 → 1#~5#皮带同时运行。设备正常开动完毕。
当正常停止混料机A时:1#~5#皮带同时停止 → 延时10秒 → 6 #皮带停止 → 延时10秒 → 混料机A停止 → 延时10秒 → 7#皮带停止。设备正常停止完毕。
当正常开动或停止混料机B时的顺序和正常开动或停止混料机A时的顺序相同。
1#~7#皮带每台设有4个防止皮带跑偏的检测的装置(行程开关),在运行过程中,无论1#~7#皮带中任何一台跑偏时,系统正常停车。图2是配料系统运输电气设备启动、停止的顺控逻辑图。 紧急停车:当有下列紧急停车信号出现时,所有设备同时停车。
7#皮带故障;
混料机A或混料机B故障;
6#皮带故障。
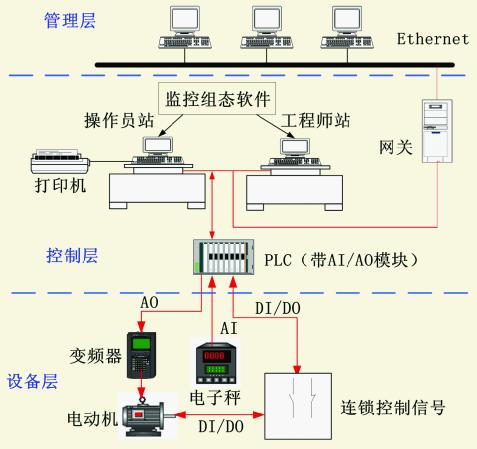
图3 控制系统构成示意图
手动操作:每台在设备在现场设一个操作控制箱,通过转换开关进行手动、自动切换,所有设备要求能在现场进行手动操作(启动、停止)。
(2) 模拟量信号的处理
对于模拟量信号的测量,主要是针对每条皮带上物料瞬时流量,这里采用皮带电子秤来完成,输出与瞬时流量成正比的4~20mA的标准信号送到PLC来完成配料比的控制。
3 控制方案及系统构成
图3是控制方案及系统构成图。组成:PLC(带模拟量输入输出模块)+ 上位机及监控组态软件。
所有的数字量和模拟量过程检测参数及控制都由PLC来完成,数字量控制部分由PLC通过编程来实现所有连锁控制信号、电器设备的逻辑顺序控制;模拟量的处理由PLC的模拟量输入输出模块来进行处理,由上位机及监控组态软件来完成过程参数的各种控制、显示及累计等。所有模拟量、数字量的监控由监控组态软件根据工艺监控要求进行组态,在计算机上完成所有工艺参数的显示、操作。PLC与上位机的通讯由监控组态软件中进行设置。最后通过网关将控制层和设备层的网络与该厂的内部局域网相联接,使管理者在网上可以实时观察到整个生产过程。
3.1 组态王软件的网络结构
组态王完全基于网络的概念,是一种真正的客户服务器模式,支持分布式历史数据库和分布式报警系统,可运行在基于TCP/IP网络协议的网上,使用户能够实现上、下位机以及更高层次的厂级连网。TCP/IP网络协议提供了在不同硬件体系结构和操作系统的计算机组成的网络上进行通信的能力。一台PC机通过TCP/IP网络协议可以和多个远程计算机(即远程节点)进行通讯。组态王的网络结构是一种柔性结构,可以将整个应用程序分配给多个服务器,可以引用远程站点的变量到本地使用(显示、计算等),这样可以提高项目的整体容量结构并改善系统的性能。服务器的分配可以是基于项目中物理设备结构或不同的功能,用户可以根据系统需要设立专门IO服务器、历史数据服务器、报警服务器、登录服务器和WEB服务器等。
3.2 控制系统组态
图4是用组态王6.5所做的配料系统主流程监控画面。在配料系统主流程监控画面上可进行手自动切换、对所有的电气设备进行开停操作、设备运行指示、各种物料的瞬时流量、累计显示等;在该配料系统中,共计制作了十余幅不同功能、形式的流程图画面,以菜单、按钮等不同的形式进行链接,操作非常方便。
(1) 对数字量的处理
组态王软件可对PLC上的DI、DO进行读、写操作,将所有电器设备的运行状态在监控画面上进行显示,在自动状态时,所有单台设备的启动停止按钮自动隐藏,只能按PLC程序进行顺序开停,在手动状态时,所有单台设备的启动停止按钮自动显示出来,可在计算机上对所有的电器设备进行启动、停止操作;当检修时可将现场的转换开关打到手动状态在现场进行操作。
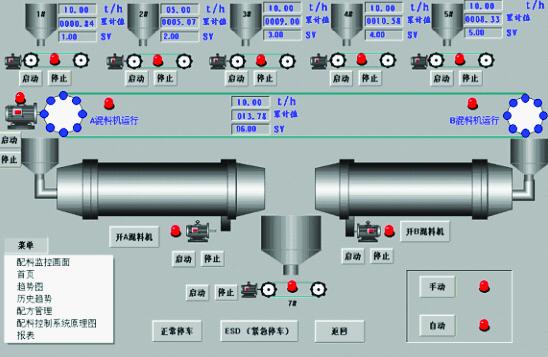
图4 配料系统主流程监控画面
(2) 配料比的控制
在监控画面上,可显示每一种物料的瞬时流量、累积值和给定值,配料比的控制,是配料系统的关键所在,在组态软件上有二种方法来实现。
方法一:用组态王中的“配方”功能来完成,在组态时先定义好变量、配方种类,使用起来相当方便,在投产之前,技术人员通过化验,检测物料成分,确定几种物料之间的配比关系及每种物料所含水分的多少,再通过管理人员向配方库中输入各种配方。系统运行时,监控系统自动计算和称量各种配料,保持配比的准确,操作人员根据不同的物料选择不同的配方,操作人员只需从配方库中调用需要的配方,这样监控软件就可根据配方情况进行协调控制,实现各种物料按预定的配方进行配比。
方法二:用组态王中的KingACT软件来完成,KingACT基于PC机上建立的实时控制软件,提供符合IEC1131-3标准的2种PLC编程语言,包括梯形图(LD)、功能块(FBD)。可方便地实现简单和复杂的控制系统,利用组态王的功能块(FBD)很容易的就可以实现一个比值控制系统来满足配料系统的要求。
3.3 其它功能
(1) 控制分组、趋势图及报表
在上位机的监控组态软件上实现控制分组,主要完成许多实时性的操作,如控制系统的手/自动切换,PID参数的调整等;趋势图分为实时趋势和历史趋势,是将一些重要的工艺参数作详细的记录,通过查看趋势图,可帮助操作人员调整工艺参数,为操作控制和事故分析提供重要的依据。报表制作可根据用户的需要把一些重要的参数分类统计制作成班报表、日报表、月报表、季报表和年报表等,定时输出到打印机,方便记录和查询。
(2) 系统安全管理
安全保护是应用系统不可忽视的问题,必须解决好授权与安全性的问题,系统必须能够依据用户的使用权限允许或禁止其对系统进行操作。组态王提供一个强有力的先进的基于用户的安全管理系统。在“组态王”系统中,在开发系统里可以对工程进行加密。打开工程时只有输入密码正确时才能进入该工程的开发系统。对画面上的图形对象设置访问权限,同时给操作者分配访问优先级和安全区,运行时当操作者的优先级小于对象的访问优先级或不在对象的访问安全区内时,该对象为不可访问,即要访问一个有权限设置的对象,要求先具有访问优先级,而且操作者的操作安全区须在对象的安全区内时,方能访问。以此来保障系统的安全运行。
4 结语
利用组态王软件与PLC相结合可以方便的实现配料系统的控制,软件上组态灵活,控制方案也可适应不同层次用户的需要,修改方便,硬件上支持与多种设备相连接,可以组成不同的控制系统,利用通信网络可将生产过程数据送到管理层,实现数据共享。与传统的控制方案相比,操作简单,维护方便,控制精度高。整个配料系统经过一年多的运行,设备故障率低,实现了生产、操作全过程的自动控制,大大减少了人为的误操作,完全满足生产工艺的要求。 |