胡攀 (1984-)
男,湖北鄂州人,硕士研究生,主要研究方向计算机控制与自动化网络。
摘 要:通动态定量称重系统是一种非线性、大滞后、时变性的系统。PID控制应用广泛,但其参数整定仍未得到很好的解决。因此采用神经网络与PID控制理论相结合,为动态定量称重系统设计了一种神经网络PID控制器,以及提出了新的智能控制策略。该控制器算法简单,通过自学习、记忆功能在线调整PID控制参数Kp、KI、KD,来实现具有最佳组合的PID控制。
关键词:动态定量称重系统;神经网络;PID控制器;控制策略
Abstract: The dynamic quantitative weighing system is a kind of nonlinear ,large delay,time-varying system. PID controllers are used in a large number of industries. However,there are no satisfactory solutions about the turning of PID parameters.Therefore the neural network PID controller is designed by means of the neural network theory combined with the PID control theory for the dynamic quantitative weighing system,and proposed the new intelligent control strategy.The designed algorithm is easy.The optiml combination of PID controller can be realized by self-learning and memory fuction adjusting the control parameter Kp、KI、KD of PID online.
Key words: dynamic quantitative weighing system; neural network r; PID controller; control strategy
1 引言
食品、医药、化工等行业的生产过程中都需要对产品进行定量包装。动态定量称重的两个关键问题:一是称重精度;二是称重速度。这两方面需要综合考虑,两者兼顾。在工业连续生产过程中,如何同时提高动态定量称重精度和称重速度,一直是企业和计量领域亟需解决的难题之一[1,2]。智能算法采用基于BP神经网络的神经网络PID预测控制算法,发挥神经网络的自学习、自适应特性,按照控制要求自主调节PID控制器Kp、KI、KD的参数,以得到最优的PID控制参数,从而达到称重精度和称重速度的最优化。本文将PXA270微处理器为核心的系统硬件与神经网络PID控制器自学习相结合,针对动态定量称重系统提出了一种新的智能控制策略。
2 动态定量称重系统模型
系统采用螺旋加料机进行加料。在0—tn时刻螺旋给料机出料的总重量为Q(t)与物料的流量A(t)的关系为: (1)
对上式进行拉式变换可得到
(2) 则螺旋给料机向称量容器加料过程的传递函数为
(3)
ρ为物料的密度。
假定对象是一阶惯性的, 则螺旋进料器的运动方程为[3]
(4)
则根据上式可推导螺旋加料器的传递函数为:
(5)
其中,a1和b1为对象参数,k1为转速与流量之间的变换系数。
图1为神经网络PID混料控制结构框图,物料密度ρ=k。
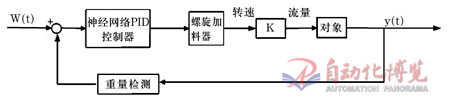
图1 神经网络PID混料控制结构框图
3 神经网络PID控制算法
BP神经网络具有逼近任意非线性函数的能力,而且结构和学习算法明确。通过神经网络自身的学习,可以找到某一最优控制规律下的P,I,D参数。基于BP神经网络的神经网络预测PID控制器的结构,如图2所示,控制器由两部分组成:① 经典的PID控制器:直接对被控对象进行闭环控制,并且三个参数为在线整定;② 神经网络NN:根据系统运行状态,调节PID控制器 Kp、KI、KD的参数,以期达到性能指标的最优化。
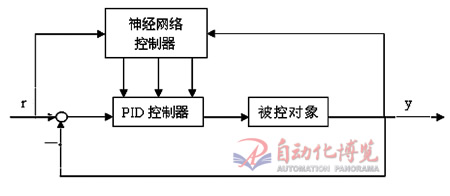 图2 神经网络预测PID控制框图
(6)
式中 Kp、KI、KD分别为比例、积分、微分系数,将为系统运行状态的可调参数时,可将式描述为
(7)
式中 是与Kp、KI、KD,u(K-1),y(K)等有关的非线性函数,可以用BP神经网络NN通过训练和学习找到一个最佳控制规律[3]。
3.1 神经网络算法
神经网络预测控制器采用的是BP神经网络。BP网络在应用于预测预报之前,需要一个网络学习过程。网络根据输入的训练(学习)样本进行自适应、自组织,自学习,确定各神经元的连接权W和阈值。经过多次训练后,网络具有了对学习样本的记忆和联想的能力。网络学习过程包括信息正向传播和误差反向传播两个反复交替的过程。
在正向传播过程中,输入信息从输入层经隐含层逐层处理,并传向输出层,每层神经元的状态只影响到下一层神经元的状态。信息正向传播过程可由第k层第j个神经元的输入输出关系来简单地表征 (8) (9)
式中 为第(k-1)层第i个神经元到第k层第j个神经元的连接权因子; 为该神经元的阈值;f(x)为网络节点作用函数,通常为一非线性函数,如sigmoid函数;nk为第k层神经元的数目,m为神经网络模型的总层数。
误差反向传播的学习过程是将从输出层到输入层向后传播并修正相应网络参数的过程,通过修改各层神经元的权值,使网络的误差信号最小。
权向量和阈值的修正采用梯度法,根据该法分别得到权向量和阈值的迭代式为
(10) (11) η为网络学习率或学习因子,α为动力因子。
上述各式构成了BP神经网络模型。根据神经网络的训练学习算法,可确定网络的连接权向量和阈值等参数,即确定输入向量与输出向量的对应关系,使实际输出与计算输出的误差达到最小[4]。
3.2 神经网络算法的结构
神经网络控制器均采用3层的BP网络。BP网络有3个输入节点、1个隐含层、3个输出节点,激发函数取tansig,BP网络结构[5]见图3。神经网络输入选为:
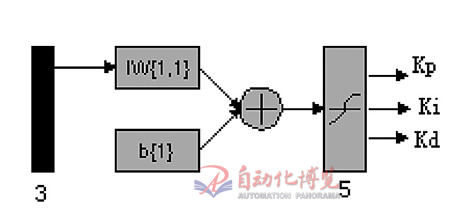
图3 BP网络结构[5]见图3 (12)
4 控制策略
4.1 硬件系统设计
系统采用的嵌入式工控主板,它是在PXA270微处理器的基础上附加SDRAM(64MByte),FLASH(32MByte)、以太网(10/100MEthemetcontroll)CPLD等外围芯片和外设接口组成的。PXA270是英特尔公司的PXA27x系列嵌入式处理器。这是一款高性能,低功耗的XScale处理器,最高频率可达624MHz。系统主要用到以下的外设接口:USB Host、USB Device;UART;JTAG;LCD;PC104;触摸屏。嵌入式的特点为之一是硬件设计与软件设计紧密联系,在设计过中需要考虑二者之间相互的影响。
系统硬件设计框图如图4所示。在本动态称重配料控制系统中,重量信号经放大变送后送到模拟量数据输入模块中进行转换处理,后送微处理器,CPU根据该信号的大小来确定物料的重量,并通过数字量I/O模块控制电机和阀门动作。控制系统可通过串行通讯模块或以太网与上位机进行通信;嵌入式工控主板与数据采集模块采用PC/104总线进行通信。
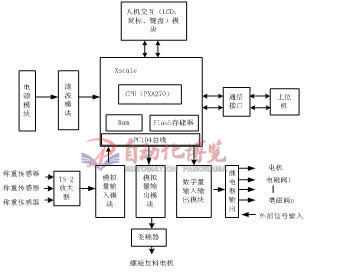
图4 系统硬件框图
4.2 控制方法
神经网络PID控制器自学习过程(如图5为神经网络PID控制器自学习过程图):
(1)确定称重物料在静态下的重量为x千克(其中水y升,固态物料z千克),作为系统训练的目标值。
(2)设定停止加料工作点a(k)千克(模拟量数据输入模块采集到的物料称重重量)时,数字量I/O模块控制下料电机停止工作,系统不再加料。
(3)下料电机停止工作t(t>tp,tp为空中落量下落时间)秒后,模拟量数据输入模块采集n组称重数据,并通过中位值平均滤波法求得此次称重过程的实际输出值r。
(4)停止加料工作点的调整采用二分法,即a(k+1)=a(k)+ [x-a(k)]/2。
(5)计算反向误差与权值的学习。
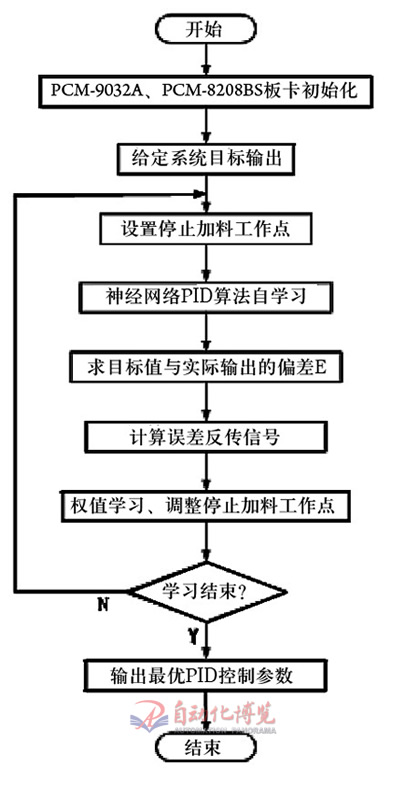 图5 神经网络PID控制器自学习流程图 (13) (14)
(6)判断经神经网络PID控制器自学习自训练后,是否得到满足要求的实际输出值。如果满足要求,输出Kp、Ki、Kd;不满足要求,继续下一轮训练。
(7)在确定了停止加料工作点 以及最优Kp、Ki、Kd后,即可定量称重重量为x千克的物料。
5 结语
本文针对动态定量称重系统设计了一种神经网络PID控制器,提出了一神经网络PID控制器为核心的新的控制策略。该控制策略已在本文所设计的硬件系统条件下通过程序调试并投入运行。
其它作者:梁岚珍(1957-),女,教授,硕士生导师;李靖(1982-),男,山东临沂人,硕士,中国重汽工程师。
参考文献:
[1] 白瑞林,李军,白瑞祥. 基于神经网络技术的动态定量称重控制方法的研究[J].自动化仪表,2000,21(7),8-10.
[2] 王书鹤. 螺旋加料控制方法的研究[J]. 山东大学学报,2003,38(1),83-85
[3] 杨新志. 粉状物料称重系统的预测控制[J]. 上海大学学报,1999,(5),414-418.
[4] 易继锴,侯媛彬.智能控制技术[M].北京:北京工业大学出版社,1999.
——转自《自动化博览》 |