活动链接:2013年控制网技术专题---中国工业迎来机器人时代
ABB机器人部汽车工业-冲压自动化系统项目经理杨宝剑
这是中国首条全自动化重卡冲压生产线。他诞生在国内重型汽车领域的龙头企业,年产量超12万台,居世界首位的中国重汽集团济南卡车股份有限公司。这条生产线主要用于生产目前国内技术最先进、品质最高的新一代自主研发重型汽车HOWO-A7。作为中国重汽2009年的主力车型,HOWO-A7已经出口到国际市场。它的投产标志着中国重型卡车生产的一次重大技术飞跃,整车制造水平得到全面提高,进而提升中国重型汽车在海外市场的竞争力。

中国重汽集团济南卡车有限公司冲压经理 马兆岭
中国重型汽车集团( 中国重汽)为了全面提高整车制造水平,为其最先进、品质最高的新一代自主研发重型汽车HOWO-A7搭建国际领先的制造设备生产平台, 规划完成了中国首条全自动化重卡冲压生产线系统。ABB机器人部作为行业领先的冲压生产线系统集成供应商,根据客户要求,结合国际最先进冲压自动化技术,高标准,严要求设计、安装、调试并以最短的项目周期成功实施了该项目。
技术创新—将最先进的技术带入中国
建成后的自动化冲压生产线共分为材料存放区、板料拆垛区、清洗涂油区、位置校正区、冲压成型区、成品件检验区、工艺废料打包区七大区域。厂房占地面积4000平方米,投资额1.2亿元人民币。整条生产线由7台瑞典进口ABB IRB6600型机器人、德国SMT公司生产的1台清洗机和1台涂油机、5台压力机、一条废料输送线和一台打包机组成,由上海ABB工程有限公司采用先进的总线控制技术和DCS的控制理念对生产线的各个单元进行集中控制,充分保证了生产线的可靠性、稳定性。
该生产线在国内首次应用ABB先进的冲压视觉对中系统和全线监控系统等最新软件技术,将原有卡车生产中的人工手动操作提升为全线自动化生产。ABB机器人部汽车工业-冲压自动化系统项目经理杨宝剑总结说:“该冲压系统适用任何板材形状,可提高材料利用率;反应速度快,大幅加快生产节拍,提高生产效率;控制系统更加通用化,且易于维护。”
作为中国首条全自动化重卡冲压生产线,该系统实现了众多技术方面的创新:
(1)板料自动化拆垛系统
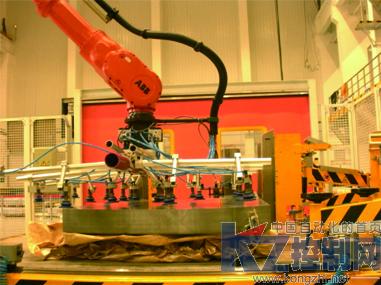
拆垛机器人准备抓取板料

板料位置校正准确被放入压机
拆垛系统由两台垛料小车和一台拆垛机器人组成。生产线正常运行时,磁力分张器将垛料小车上的板料自动分离开,拆垛机器人将板料抓起,通用端拾器上的双料检测传感器上确保机器人每次抓取单张板料,机器人将板料放到线首输送带上,完成拆垛过程。拆垛结束时,料垛末端的无料检测装置动作,拆垛机器人自动切换至另一台垛料小车。配置两台垛料小车保证了生产连续不间断进行。拆垛机器人携带通用端拾器,吸盘数量可以按照程序设定自由选择,使拆垛系统可以完成对不同大小和形状板料的拆垛。
(2)清洗、涂油系统
清洗、涂油系统是将拆垛后的板料进行清洗和涂油的过程。板料通过传送带进入清洗机,经刷洗、挤压等多道工序,能够有效清除板料表面的污物及轻微锈蚀,清洗后的板料表面光洁如镜。涂油机能根据不同产品件的涂油需求,对板料进行双喷射式涂油。涂油时可以在线编辑产品件的涂油轨迹,根据工艺需要更改喷油强度和喷油位置。
传统的冲压工艺,板料无法清洗,常常因为板料表面不清洁造成产品件硌伤。
而采用人工涂油方式,浪费时间长,消耗油量大,涂抹不均匀,还易造成板料的二次污染,无法保证产品件的质量。由ABB集成的整线清洗、涂油系统,速度快、成本低、效果佳,极大改善了产品件的外观质量,并能有效延长模具的使用寿命。
(3)视觉对中系统
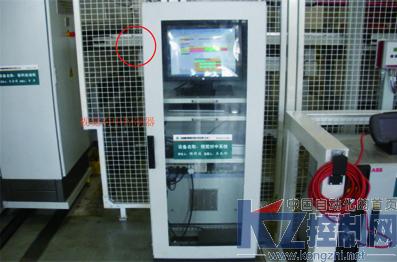
视觉对中控制器
视觉对中系统对清洗涂油后传送过来的板料进行位置校准,校准的重复准确性对板料在模具内的精准定位至关重要。中国重汽冲压生产线首次采用了世界领先的视觉对中系统,具有很高的科技含量。
清洗涂油后的板料经传送带传送至感应开关,当感应开关检测到板料到位后,PLC触发相机拍照,通过视觉处理系统,计算出该板料与标准模板的位置偏差量,通过以太网将偏差数据发送给机器人,机器人收到数据后调整运动姿态,将板料准确无误的送到模区内(位置定位误差≤±1mm)。
与传统的机械对中系统相比,视觉对中系统具有结构更合理、响应速度快、重复定位精度高、可靠性强等突出优点。
(4)生产方式的变革实现了产品件质量的跨越式飞跃
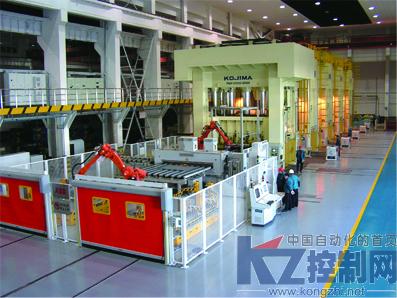
自动冲压系统
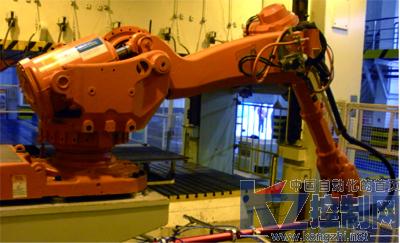
适用于冲压领域的ABB IRB6600系列机器人
全自动的连线冲压生产方式,实行生产全封闭管理。通过机器人的传递实现了板料的转运,由机器人和压机互相自动配合完成产品件的冲压过程,整条生产线除了线首需要人工上料、线尾需要人员装箱检验以外,其它区域基本不需要人员介入,大大解放了劳动力。由于人员不需要介入冲压作业,大大提高了人员的安全性,降低了安全事故。机器人单个产品件的连续传送既避免了传统单工序生产的产品件摞放造成产品件的磕碰划伤,又减少了中转工位器具和行车的使用,大幅度提高了生产效率和质量稳定性,降低了废品率,减轻了一线员工的劳动强度。
管理创新—以优秀的服务赢得用户
由于中国重汽建设的冲压生产线是国内重卡行业的首条全自动冲压生产线,缺少项目实施经验, ABB遵行一贯以客户为服务焦点的工作准则,在项目伊始就与中国重汽密切接触,就项目的具体细节问题进行反复研讨,并应其要求积极与其它配套厂家(如压力机生产厂家、废料线生产厂家等)进行电气控制方面的接口探讨,制定出切实可行的技术方案和工期规划。
项目启动以后,在项目建设前期,最先进行的是土建项目,然后压力机、废料线、打包机等厂家陆续进入,做为整个项目控制灵魂的集成者,上海ABB工程有限公司是最后进入施工现场的厂家。但为了保证进入现场后工作的顺利开展, ABB的工作人员不等不靠,做了大量的前期铺垫工作,项目经理和工程师多次到施工现场实地考察工程状况,了解工程进度,与客户和其它配套厂家进行现场交流,不断修订技术实施方案细节,解答客户疑问,并将本公司的工作进展情况及时通报给客户。
中国重汽冲压生产线项目于2008年3月20日开始启动,6月18日完成土建项目,同日开始设备安装,10月18日初步完成压力机、废料线、打包机等配套设备的安装,10月20日上海ABB工程有限公司正式进入施工现场开始工程施工,12月3日全线调试贯通并生产出第一批产品件,2009年1月20日正式竣工验收。3个月完成整个项目的全部工作体现了ABB快速高效的工作理念,也获得了用户的高度认可。
中国重汽集团济南卡车有限公司冲压经理马兆岭给予了这样的评价:“ABB细致周到的服务体现了这家世界500强企业对于用户的高度责任感!在项目实施中,我们所提出的任何问题都得到了及时有效地解决,在生产线完成之后,ABB 技术人员为我们进行了3个月的技术培训,使我们维护人员的技术水平得以大幅度的提高,解决了我们的后顾之忧。”
采访中,杨宝剑告诉记者:在此项目实施过程中,因为冲压车间配套设备的施工拖期,自动化系统的项目安装日期比原计划晚了一个月,为了配合用户的需求,ABB积极与用户沟通,增加人力,调整工期,最终按计划完成项目。杨宝剑认为这得益于整个项目实施过程中ABB在管理方面创新性的工作:
(1)实行项目经理负责制。项目经理全面驾驭整个项目的工程进展、人员调配、客户协调、服务培训、项目验收等方方面面的工作,并与绩效挂钩,充分调动项目经理的工作积极性和责任性。
(2)与客户建立良好的沟通平台。在项目启动之前就对客户进行培训,使客户对项目充分了解,与客户建立共同交流的语言,倾听客户的心声,了解客户的需求,不断修订项目实施方案的细节,大幅度降低现场施工中可能出现的返工现象。
(3)推行项目例会制。进入施工现场后,由客户牵头,所有配套厂家参与,每天早晚举行两次项目例会,就各个单位每天的工作安排和需要解决的问题进行协调,大幅度降低了现场各个厂家扯皮窝工的现象,有效地保证了施工进度。
(4)实行现场边施工边培训的服务理念。为了后期让客户能够更快更好地掌握整条生产线的使用并进行简单的设备维护,在施工过程中,现场工程师边施工边对客户的工程技术人员进行培训和讲解,让客户的工程技术人员掌握第一手施工资料,为后续的设备维护打下坚实的基础。由于施工和培训统筹进行,同时可以现场解答所有客户疑难问题,大幅度缩减了后续的培训时间并取得更好的培训效果。
(5)以客户为中心,重视项目的售后服务工作。项目竣工验收后,项目经理多次到客户处进行主动性回访,了解项目中可能存在的细节问题并以最快的速度进行反馈解决。派驻现场服务工程师对客户进行陪产,随时解决生产过程中可能存在的技术问题,解答客户疑问,培训客户员工,帮助客户进行备品备件的选型,解除了客户的后顾之忧,赢得客户的充分信任。
高效收益—一次成功的合作
目前该生产线承担着中国重汽HOWO、HOWO-A7两种产品系列30余种重要外覆盖产品件的生产,单班生产工人仅需7名(原为50人),单月产能超过10-12万件。
在没有建设该条冲压线之前,中国重汽在产能不足的情况下只能通过产品外协生产来保证焊装生产的需要,此举不但使成本增加,同时给全面质量控制带来困难。该条冲压线的及时建成,中国重汽将影响质量的关键外覆盖件全部有能力安排自己生产加工,2009年投产以后的10个月的时间里,该条冲压生产线实际完成产品件在85万件左右,除去辅料消耗、设备维护和人工费用外,实际为该公司创造效益在1500万元以上。
“节约人力、提高生产效率、产品质量得以保障、生产环境得以改观,企业的美誉度也得以提升。”马兆岭认为这无疑是一次成功的合作:“项目的实施效果出乎了我们的意料!
中国重汽自2002年开始与ABB的合作,目前已应用40~50台ABB机器人产品。ABB可靠的产品质量、先进的服务理念以及实现本地化生产后充足的备品备件,都让其成为我们越来越信赖的合作伙伴!”
摘自《自动化博览》2010年第六期 |