内容 | (浙江大学医学院附属邵逸夫医院消控中心,浙江 杭州 310016)胡 丹
(浙江大学工业控制研究所,浙江 杭州 310027)章 鹏
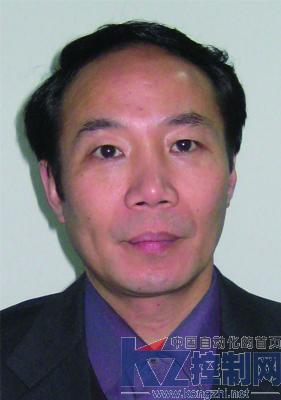
胡丹 (1964-)男,浙江杭州人,本科,助理工程师, 现就职于浙江大学医学院附属邵逸夫医院,研究方向为工业自动化控制理论研究。
摘要:针对加氢分馏装置分馏塔工艺特点,重点分析加氢分馏塔所面临的控制问题,采用多变量预测控制软件APC-Adcon,通过实验测试、模型辨识、控制器和切换逻辑设计等工作实现该工业分馏塔系的多变量预测控制,显著提高两塔运行参数的平稳性,有效降低操作人员的操作难度。实际应用的结果表明该多变量预测控制系统可有效地克服干扰、确保工艺参数的平稳运行。通过该系统的应用使在相同的负荷下,燃料气减少5%;显著提高分馏塔的分离能力,组分切割更为合理,航空煤油收率提高0.4%,取得了显著的经济效益。
关键词:预测控制;过程控制;加氢分馏装置;精馏塔
Abstract: For hydrocracking distillation chain, this paper analyses difficulties in process control of the industrial distillation chain. APC-Adcon, an APC software based on model predictive control strategy, is used to solve these problems of the distillation chain through experiments, model identification, controller and switching logical design. Successful application of APC improves disturbance rejection and product quality. The application of this system in the same charge reduces 5% of gas, increases 0.4% aviation kerosene, and therefore improves economic benefit of production.
Key words: Predictive control; process control; hydrocracking distillation chain;distillation
精馏过程是现代炼油、石化和化工生产中应用最广泛的分离过程,不仅决定着产品质量和生产能力,而且是耗能最多的过程之一。从控制的角度看,精馏过程通常具有非线性、动态响应慢等特性,且各过程变量之间存在着较强的耦合作用,是典型的难以控制的多变量过程。因此,精馏过程控制一直是过程控制理论界和工程界的重要研究内容。目前以多变量预测控制为代表的先进控制技术已经在工业精馏塔中取得了许多成功应用,可以实现提高精馏过程控制水平,平稳工艺操作、改善产品质量、增加目标产品收率和降低能耗等诸多目标,从而为企业带来可观的经济效益[1][2] 。
从加氢装置的控制现状分析,常规的控制技术没有完全适应该过程的复杂特性,存在大的纯滞后、多变量的耦合问题等。
因此,可以通过提高控制技术的水平来提高装置操作的平稳度,将关键工艺参数的波动幅度降低。采用多变量预测控制技术,是提高关键指标的平稳性,提高收率降低能耗的有效措施。APCAdcon是多变量预测控制软件包,该软件包已在连续重 整,催化裂化等大型石化装置中取得成功应用。[3]本工作根据加氢分馏装置的实际情况将多变量预测控制软件(APC-Adcon)应用于该装置,取得了良好的效果。
1 加氢分馏装置的工艺流程
1.1 加氢分馏装置
扬子石油化工股份有限公司芳烃联合装置中的加氢分馏装置主要是分馏塔、重石脑油气提塔和航空煤油塔。分馏塔对脱戊烷塔底油进行分离,生产轻石脑油,侧线采出物流经过重石脑油气提塔分离后,生产重石脑油;分馏塔塔底物流由航煤塔分离为航煤基础油和加氢裂化尾油。对分馏塔、重石脑油气提塔和航煤塔采用多变量预测控制技术。
1.2 加氢分馏装置控制状况分析
加氢分馏装置已采用了集散控制系统(DCS)。由于加氢分馏生产过程的工艺特点和常规控制系统的局限性,装置的平稳操作和高质量控制可以进一步提高;采用多变量预测控制技术能较好的解决这些问题。
加氢分馏装置目前存在的控制难点是:(1)许多重要的工艺参数需手动调节,存在控制不及时的问题,也不能达到平稳和一致的控制效果;(2)装置的干扰因素多,对塔的影响大,如:进料流量的变化、进料组分波动、加热和冷却系统的干扰以及环境条件变化等,这些因素均影响装置的平稳操作;(3)由于加氢分馏生产过程具有热量及物料平衡的工艺关系,因此许多变量存在着较强耦合关联性,带来操作与控制上的困难。
2 加氢分馏装置多变量预测控制方案
2.1 APC-Adcon的特点
APC-Adcon是基于预测控制原理的一种多变量模型预测控制工程化软件, 它以离散的脉冲响应模型作为内部模型描述待控制的多变量过程,根据设定的参考轨迹确定控制策略;通过局部优化确定未来控制作用,预测控制只实现本时刻的控制作用,下一个采样时刻,首先检测对象的实际输出,并利用这一实时信息对基于模型的预测进行修正,然后再进行新的优化。控制通过一个滚动启发式的计算过程来进行,输入按照基于内模的预测输出值与参考轨迹尽可能靠近的原则来确定[4]。
2.2 APC-Adcon的模型结构
APC-Adcon采用线性离散脉冲响应模型为内部模型,算法允许存在一定的模型失配。假设模型和过程输出可以用脉冲响应模型表示,对于单变量过程,则模型输出为:
(1)
过程输出为: (2)
其中M指模型,P指过程,下标o指输出,u指控制输入,a为脉冲响应结构参数,n为当前时刻。过程和模型输出在时刻k的状态偏差为:
(3)
设过程和模型参数在时刻k结构参数的差的平方和为结构偏差,即:
(4)
以结构偏差最小化为目标,令
(5)
可得出模型结构参数变化律为:
(6)
一般引入常数T以抑制噪声,同时引入λ调整收敛速度。
(7)
一般取λ∈[0.01,0.1];T≈10-2。由此,建立了有效的结构参数修正的算法。
2.3 参考轨迹
假设常数C是预定的输出,Po(n)为n时刻的实际输出值。
参考轨迹由上一采样值Po(n)初始化并按照某种准则期望到达设定点C。设计的未来输出可以从预先设置的存储数据中取出或由期望的曲线方程计算得到,具体形式如下:
(8)
(9)
控制算法要求给出这样的一组未来控制变量:引入控制作用后,内模的未来输出值尽可能趋于设定点。在每一采样点重复这一过程。
实际过程的未来轨迹和内模跟踪的未来轨迹会因为模型失配而不同。这一问题的稳定性依赖于模型失配程度和需要跟踪的参考轨迹。
2.4 控制和优化算法
过程模型的控制问题如果有解,控制算法的工作就是给出控制量使得被控过程的输出尽量跟踪参考轨迹。
n时刻模型输出Mo(n)如下:
(10)
(11)
(12)
式中,A(n)为结构参数向量;U(n)为控制向量。

U(n)由实际的历史控制量给出。给定参考轨迹后,用目标函数对Po(n)进行优化,再根据约束和目标优化的要求计算出下一步的控制输入。其中qi λi为多步预测输出误差和控制量的加权系数,yr(k+i)为参考输入轨迹。
为了保证未来控制输入的合理性,可以引入控制约束和执行器限制
(13)
(14)
式中,Umin,Umax 为执行器的上下范围,Vmax 为控制器每步最大输出。为了消除控制作用的振荡,实现优化目标,还可以定义内部变量或二级输出约束
(15)
式中,h为内部定义的约束向量,D为控制器输出范围约束。
根据约束和限制条件,重新计算合理的控制量。如果严格地考虑到约束,理论上所有的未来控制量必须计算出。但实际上,在性能损失不大的情况下,预测时间段可以缩短到几个点。基于以上原则,在给定的约束下计算出控制量并用于下一步的控制。
2.5 控制方案
针对加氢分馏装置生产装置和控制系统的特点,采用多变量预测控制技术APC-Adcon实施对加氢分馏装置的多变量预测控制。该预测控制系统由现场仪表、DCS、先进控制系统上位计算机组成。加氢分馏装置多变量预测控制系统控制方案见表1。
表1 分馏塔和变航煤塔量表
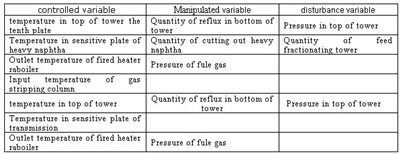
3 多变量预测控制系统的实施和效果
3.1 多变量预测控制系统的实施
加氢分馏装置多变量预测控制的平台是DCS,采用先控上位机方式实现。OPC(OLE for Process Control)通讯接口软件由OPC服务器和APC-Adcon软件的标准OPC 接口组成。OPC是与设备无关的标准软件接口,通过OPC服务器访问过程数据,可以克服各种网络结构和网络协议的差异,具有广泛的适用性。OPC服务器安装在工作站上,负责预测控制系统与DCS现场控制站FCS之间的数据通讯。加氢裂化分馏装置先进控制系统则作为OPC客户端,通过以太网实现与先控工作站上OPC服务器的数据交换。
通过实验设计和测试,得到关于过程的大批真实有效的实验数据,利用这些数据,采用APC-Adcon 中的过程辩识软件进行数据处理并辩识得到过程的矩阵形式的脉冲响应模型,然后根据过程的实际工艺特点、用户指标和要求选取合理的参考轨迹、操作变量及被控变量约束和控制器结构,得到过程的多变量预测控制器。在对测试得到的控制器内模和设计的多变量预测控制器进行仿真测试、安装调试后,控制器投入实际运行。[5]
3.2 多变量预测控制系统应用效果
加氢分馏装置多变量预测控制系统投运后,具有更好的抗干扰性,能综合协调各个过程控制变量,使生产过程更加平稳,实现了下列控制目标:(1)提高主要变量的稳定性,分馏塔重石脑油灵敏板温度、重石脑油采出温度、分馏塔塔顶回流温度、分馏塔塔釜温度等过程控制变量的均方差减小20%以上;(2)提高分离效率,重石脑油及航煤基础油的收率有一定的提高;其中航空煤油收率提高0.4%;(3)降低能耗,分馏塔的塔顶回流量降低8%以上,在相同的负荷下,燃料气减少5%;(4)提高产品质量,重石脑油产品合格率达99%,航煤基础油合格率达99.5%;(5)稳定运行,常规控制和多变量预测控制可双向的无扰动切换。
(1)重石脑油灵敏板温度
多变量预测控制系统使用前后重石脑油灵敏板温度运行稳定性大幅提高。从图1、图2的曲线和表格的统计数据看,灵敏板温度TC1265.PV在先控投运前波动较大,投入多变量预测系统后,得到有效控制,标准方差值显著减小。
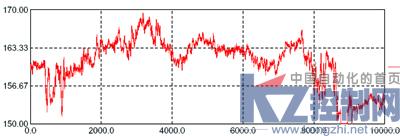
图1 TC1265.PV先进控制系统投运前(0~167h)
图2 TC1265.PV先进控制系统投运后(0~167h)
具体统计分析见表2。
表2 系统使用前后重石脑油灵敏板温度运行稳定性的比较

方差减少幅度:TC1265标准方差减少幅度=(2.789-1.067)
/2.789*100%=61.74%
效果图的采样时间为1分钟,效果图数据长度为6天23小时左右。
(2)分馏塔塔釜温度
分馏塔塔釜温度运行稳定性较大地改善,从图3、图4的曲线和表格的统计数据看,塔釜温度TC1278.PV在先控投运前波动较大,投入多变量预测控制系统后,得到有效控制,标准方差值显著减小。

图3 TC1278.PV先进控制系统投运前(0~167h)
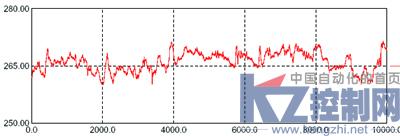
图4 TC1278.PV先进控制系统投运前(0~167h)
具体统计分析见表3.
表3 分馏塔塔釜温度运行稳定性对照表
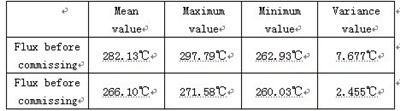
方差减少幅度:
T C 1 2 7 8 标准方差减少幅度= ( 7 . 6 7 7 - 2 . 4 5 5 )
/7.677*100%=68.02% 。
效果图的采样时间为1分钟,效果图数据长度为6天23小时左右。
(3)航煤塔航煤灵敏板温度
进料流量和前后塔液位运行稳定性也较大改善。从图5、图6的曲线和表格的统计数据看, TC1803.PV在先控投运前波动较大,投入多变量预测控制系统后,得到有效控制,标准方差值显著减小。
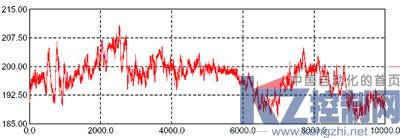
图5 先进控制系统投运前(0~167h)
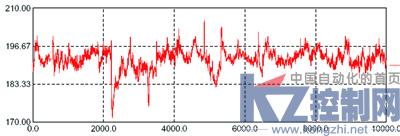
图6 先进控制系统投运后(0~167h)
具体统计分析见表4。
表4 进料流量和前塔液位运行稳定性对照表

方差减少幅度:
T C 1 8 0 3 标准方差减少幅度=(4.360-3.453)
/4.360*100%=20.80%
效果图的采样时间为1分钟,效果图数据长度为6天23小时左右。
4 结论
(1)在加氢分馏装置上的DCS平台上可实现多变量预测控制,多变量预测控制系统采用APC-Adcon软件实现。
(2)多变量预测控制系统通过通讯连接,实验测试,模型辨识和控制器设计等工作实施。
(3)多变量预测控制系统当有外界干扰,塔系各主要工艺参数能自动跟踪调整,使塔系的操作更平稳,在平稳操作的基础上降低能耗,提高主要产品的收率。
(4)多变量预测控制系统带来了显著的经济效益。
其他作者:章鹏(1975-),男,浙江杭州人,博士, 浙江大学工业控制研究所。
参考文献:
[1] G. D. Martin, et al. Closed-loop optimization of distillation energy[J].Chemical Engineering Progress,1981,9: 33-37.
[2] P.S.Fruehauf and D.P.Mahoney. Distillation column control design using steady state models: usefulness and limitations[J]. ISA Transactions,1993,32: 157-175.
[3] J. B. Riggs. Improve distillation column control[J]. Chemical Engineering Progress,1998,10: 31-47
[4] 睢刚,陈来九. 多变量模糊预测控制及其应用研究[J],控制与决策,1997(12),1.
[5] 汪涛,郑琪美,徐灿. 蒸馏过程先进控制与在线优化[J],石油炼制与化工.
摘自《自动化博览》2010年第四期 |